Master woodworking hand tools to create durable, timeless furniture with traditional techniques and expert guidance
Discover the timeless art of woodworking, where tradition meets innovation. Led by experts Bibbings & Hensby, Sandy Buchanan, Helen Welch, Matt Kenney, Tyler Shaheen, Urvi Sharma, and Alexandre Chappel, this comprehensive course covers a wide range of techniques, styles, and modern innovations. From mastering hand tools and traditional joinery to exploring the intricate Japanese Kumiko designs, delve into the world of woodworking with a variety of projects. Gain skills in crafting solid wood furniture, creating strong dovetail joints, and designing Mid-century modern pieces. Experience the blend of art and functionality by learning carving and dyeing techniques that personalize every creation.
Venture into modern possibilities with the integration of 3D printing technology, expanding your ability to design and build innovative furniture. Whether crafting a traditional three-legged stool, a Kumiko panel, or a modular shelving system, each project combines creativity and craftsmanship. Develop a deep understanding of materials, tools, and processes, empowering you to design and construct furniture that enhances any space. Embrace the journey from concept to completion, celebrating the beauty of woodworking in its various forms and styles.
What will you learn in this specialization?
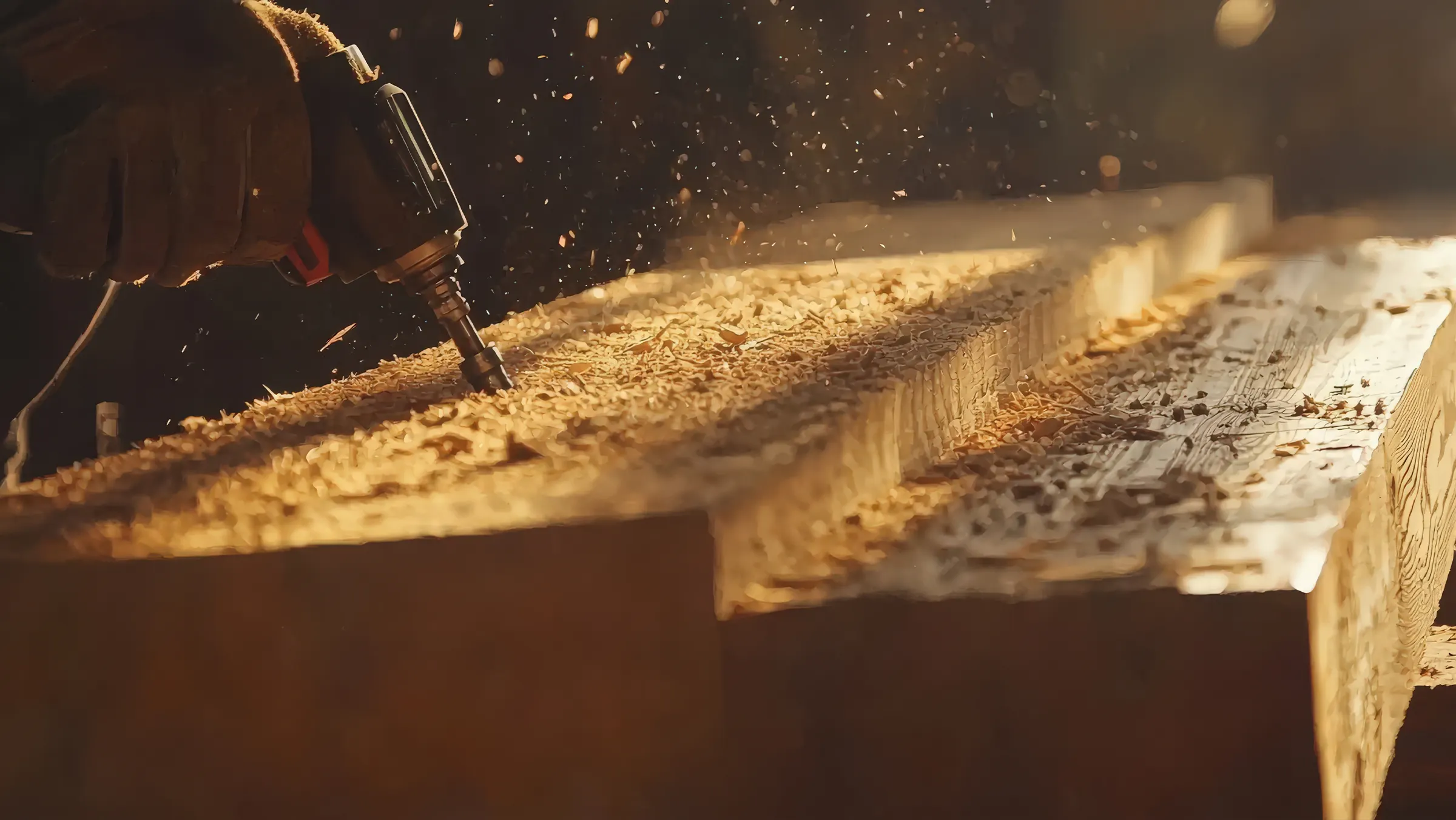
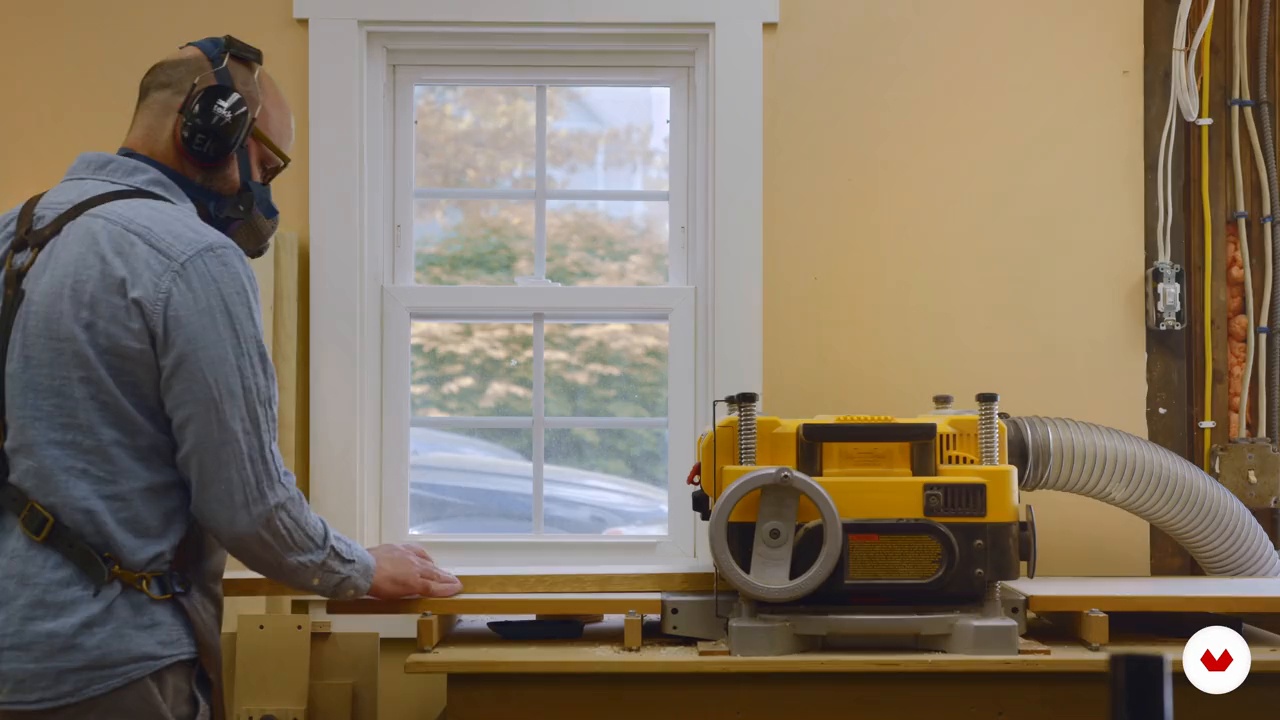
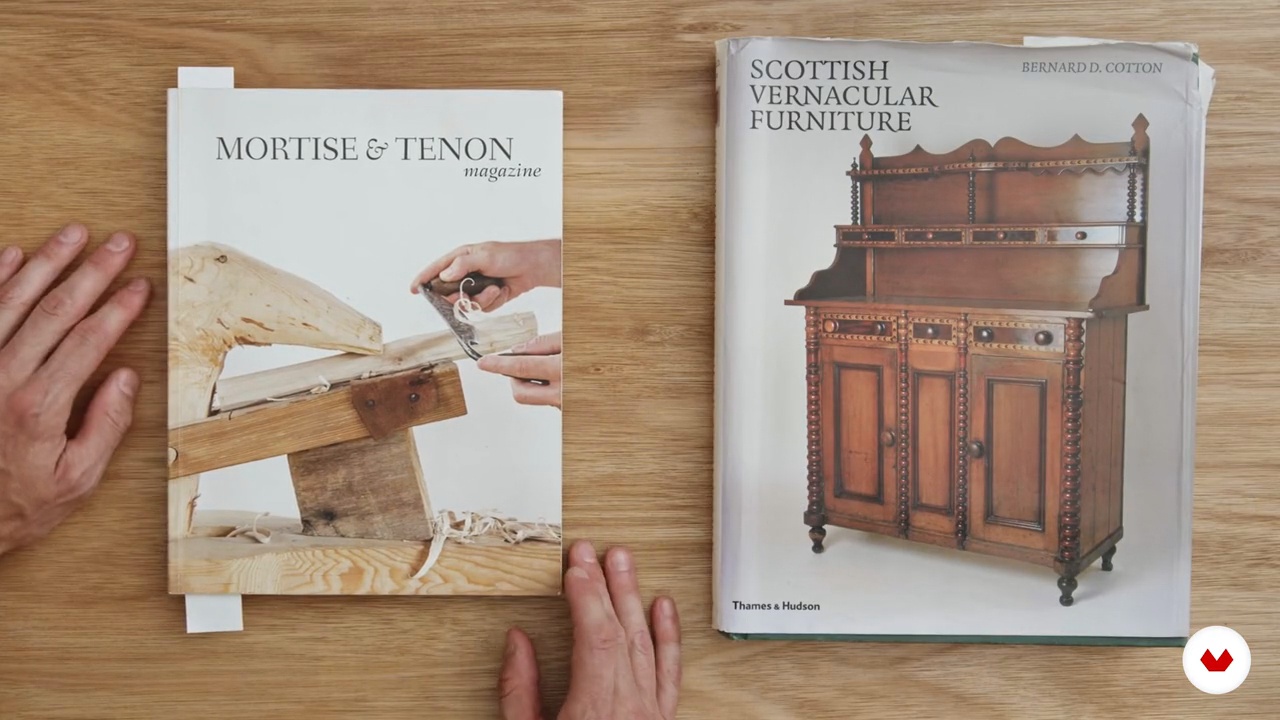
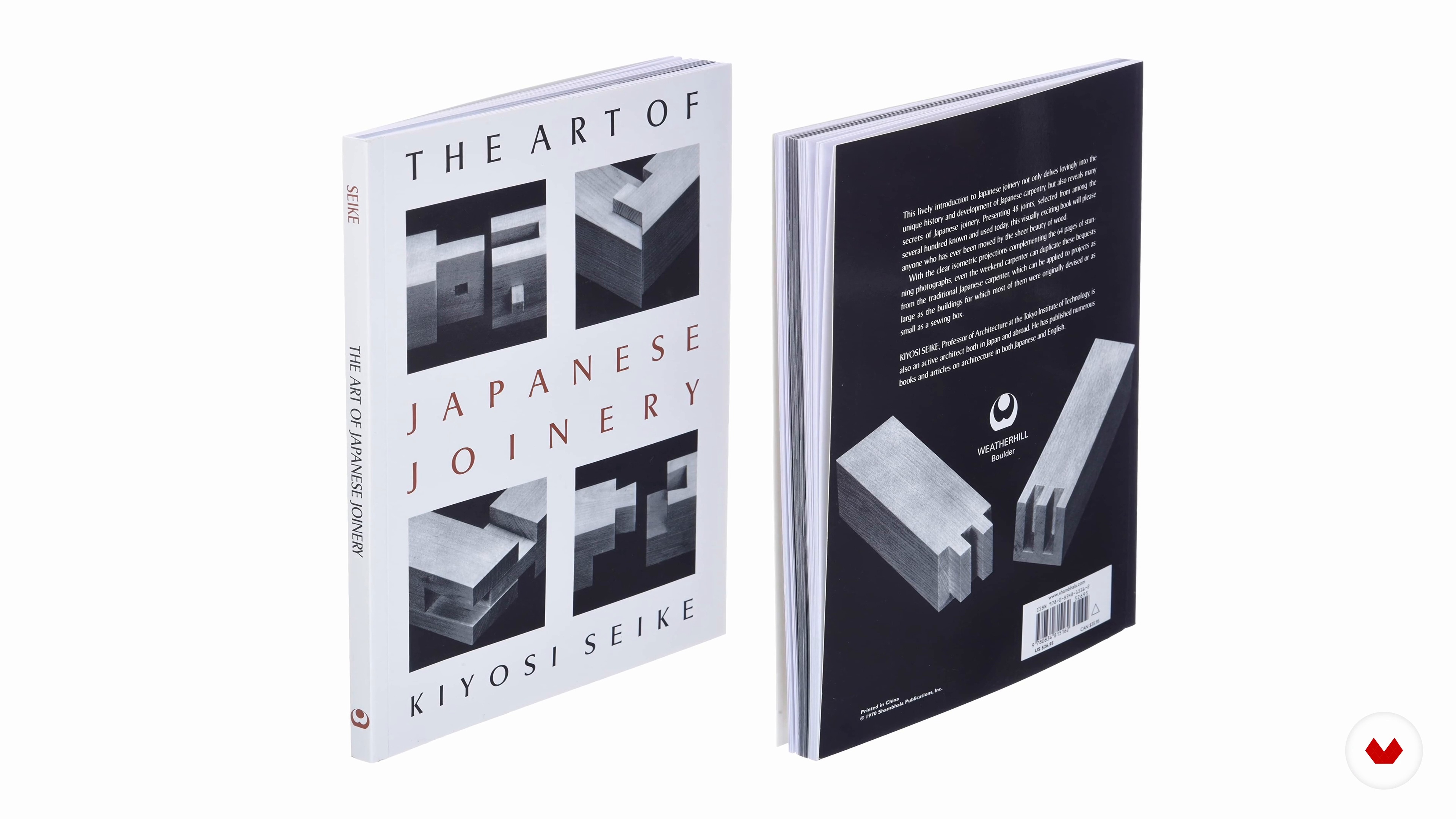
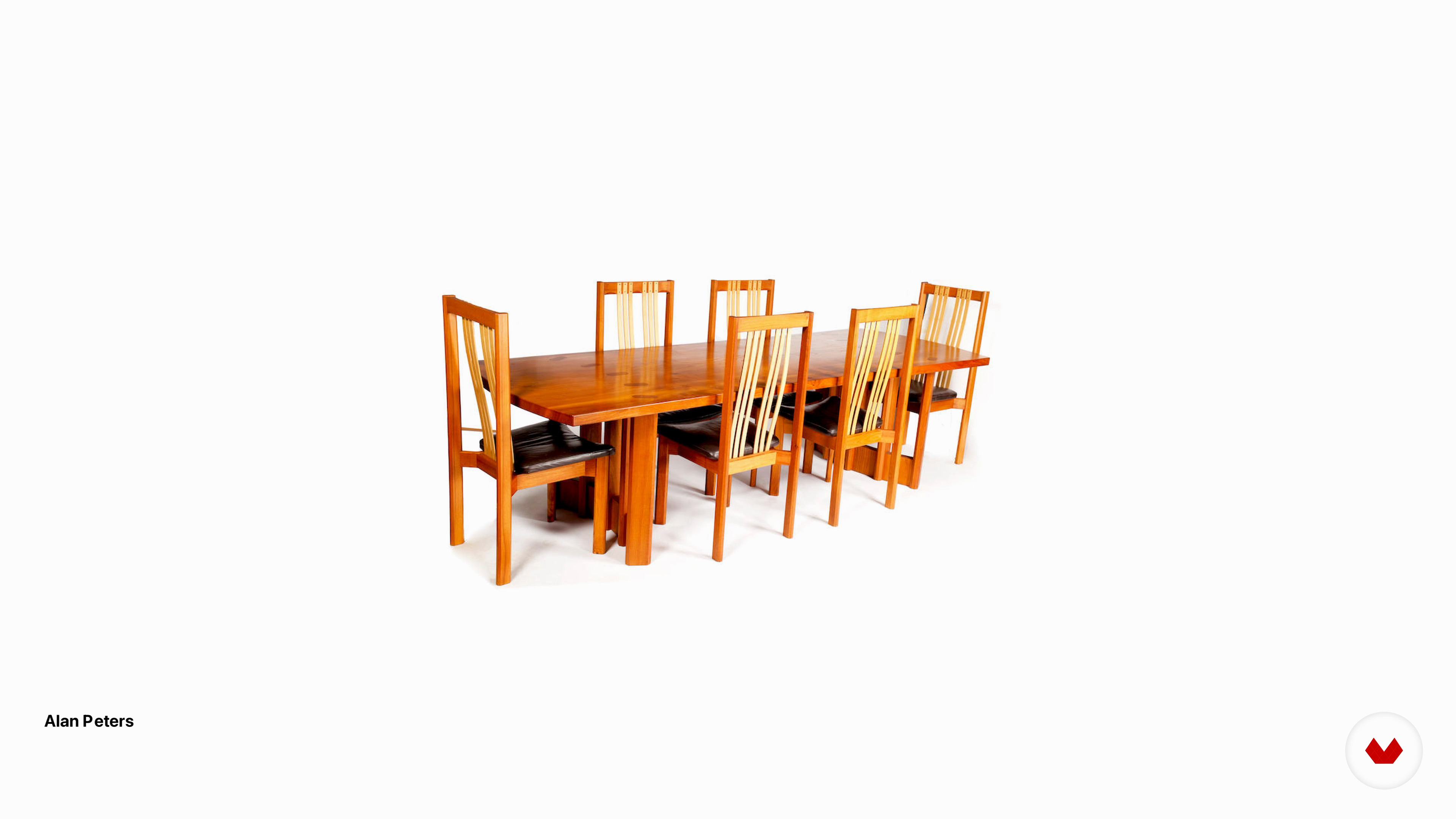
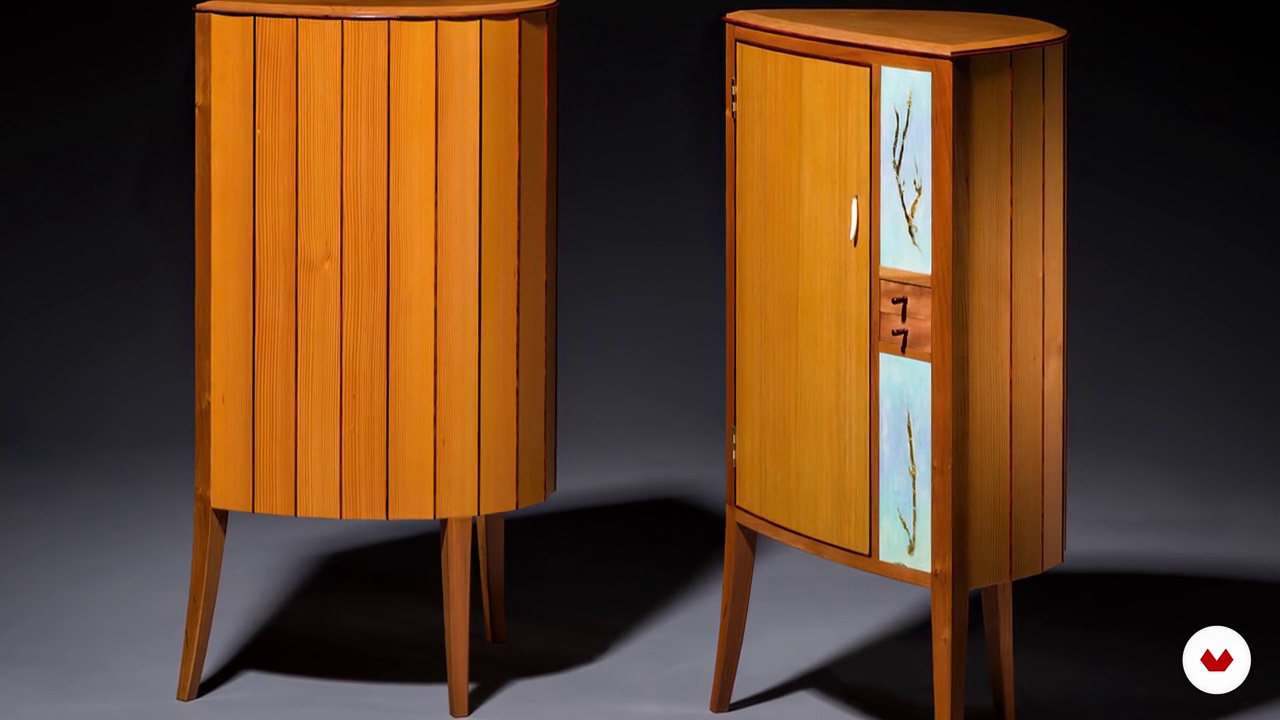
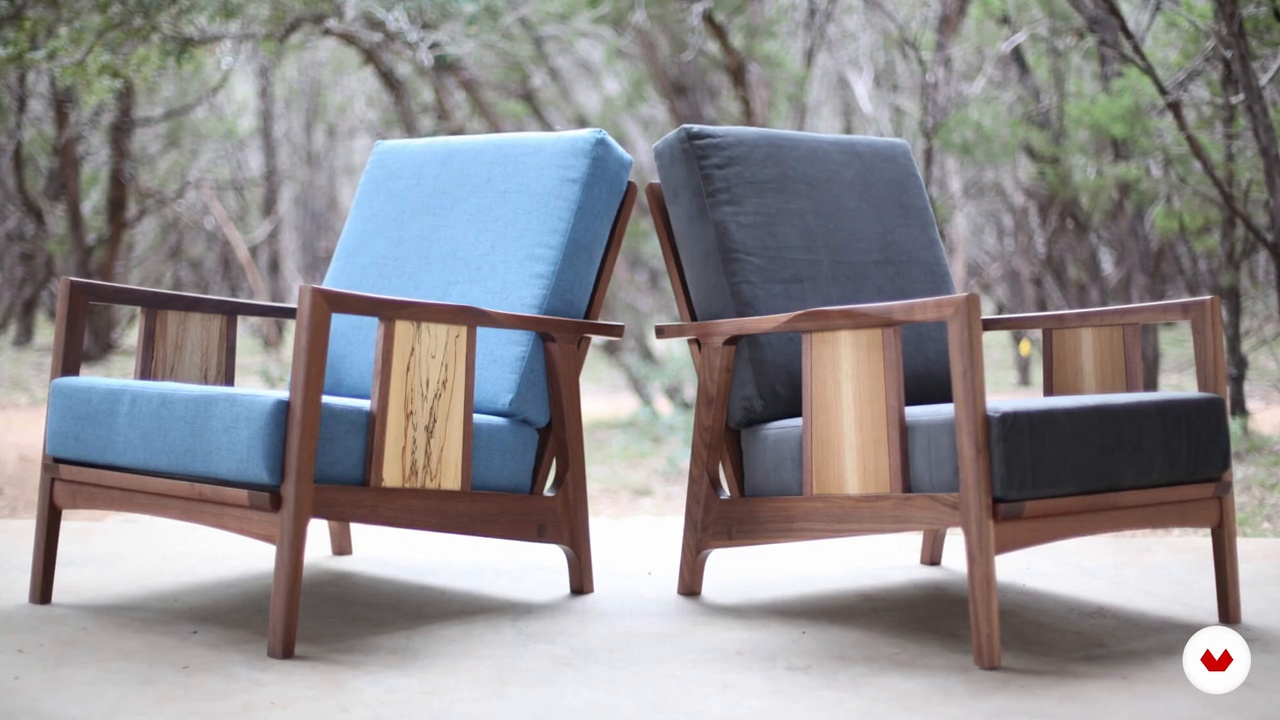
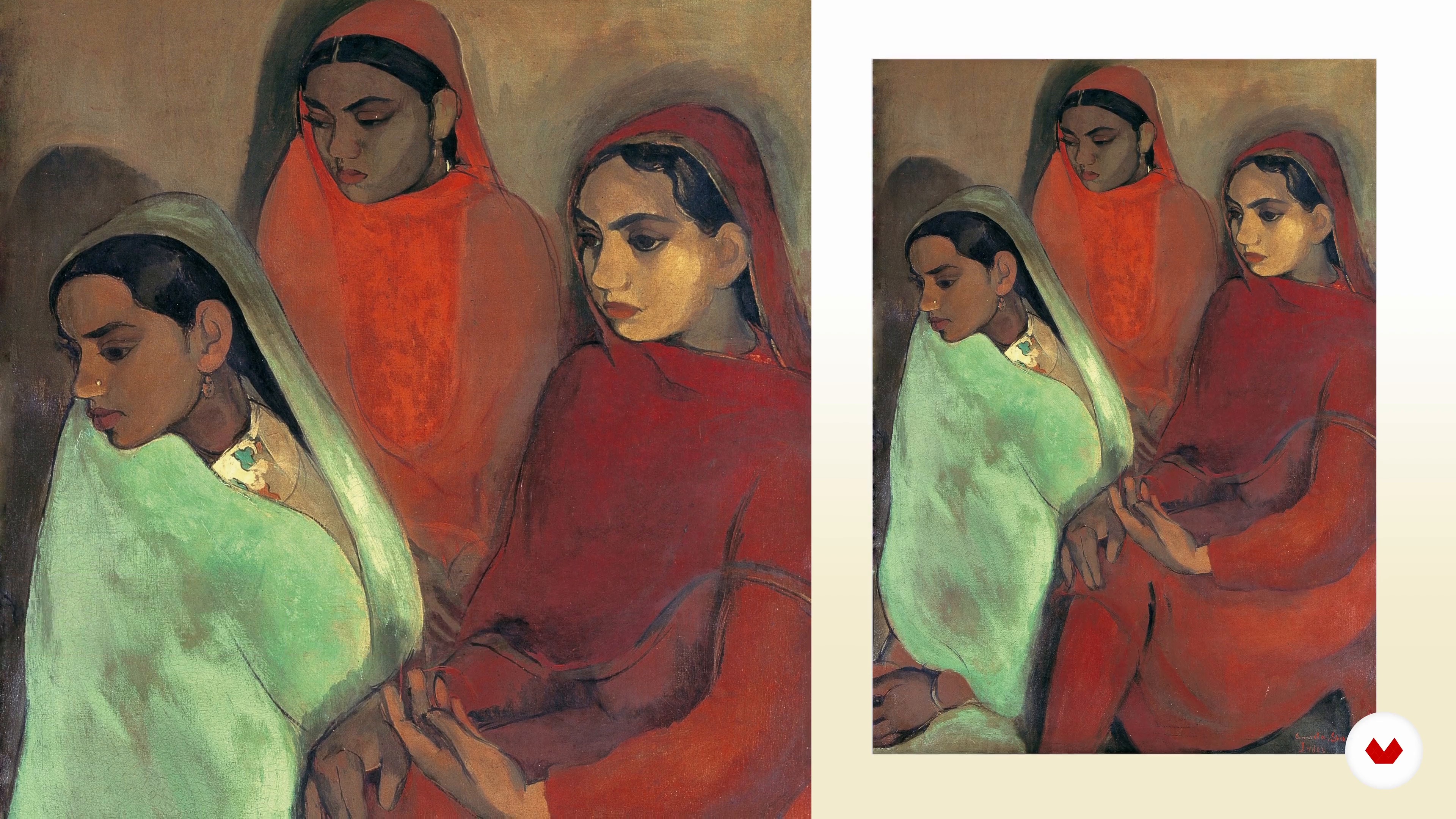
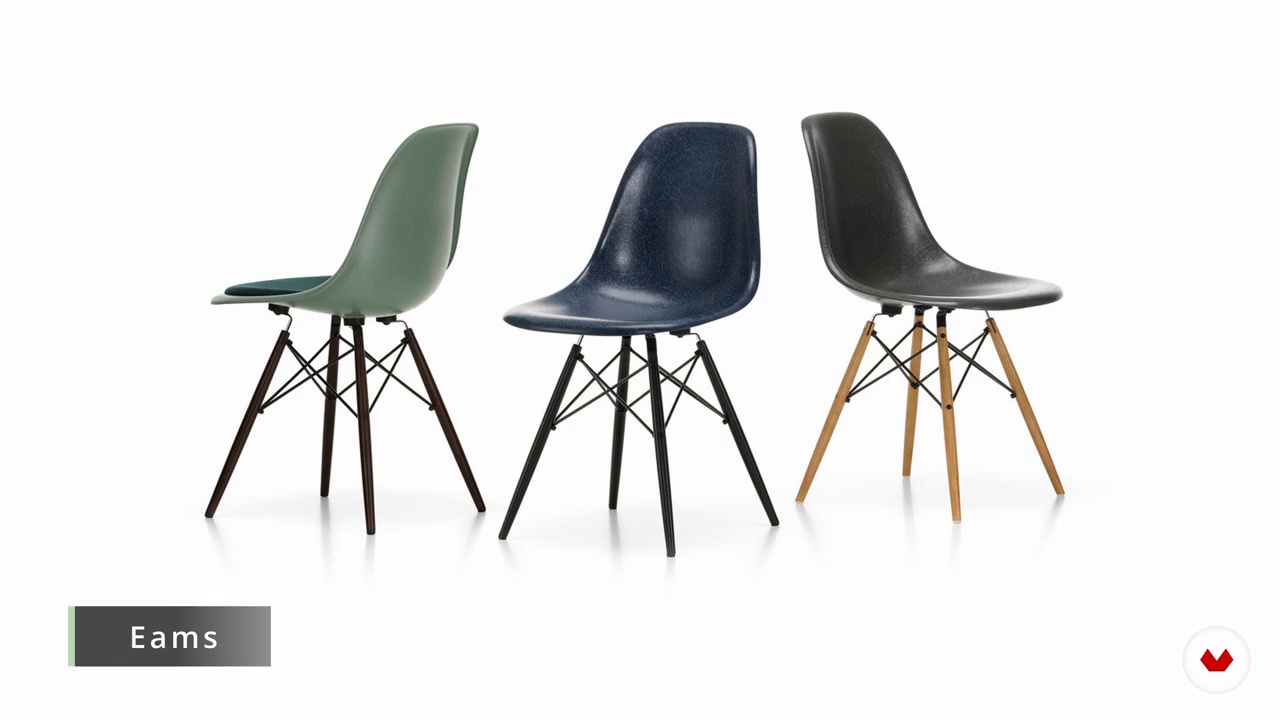
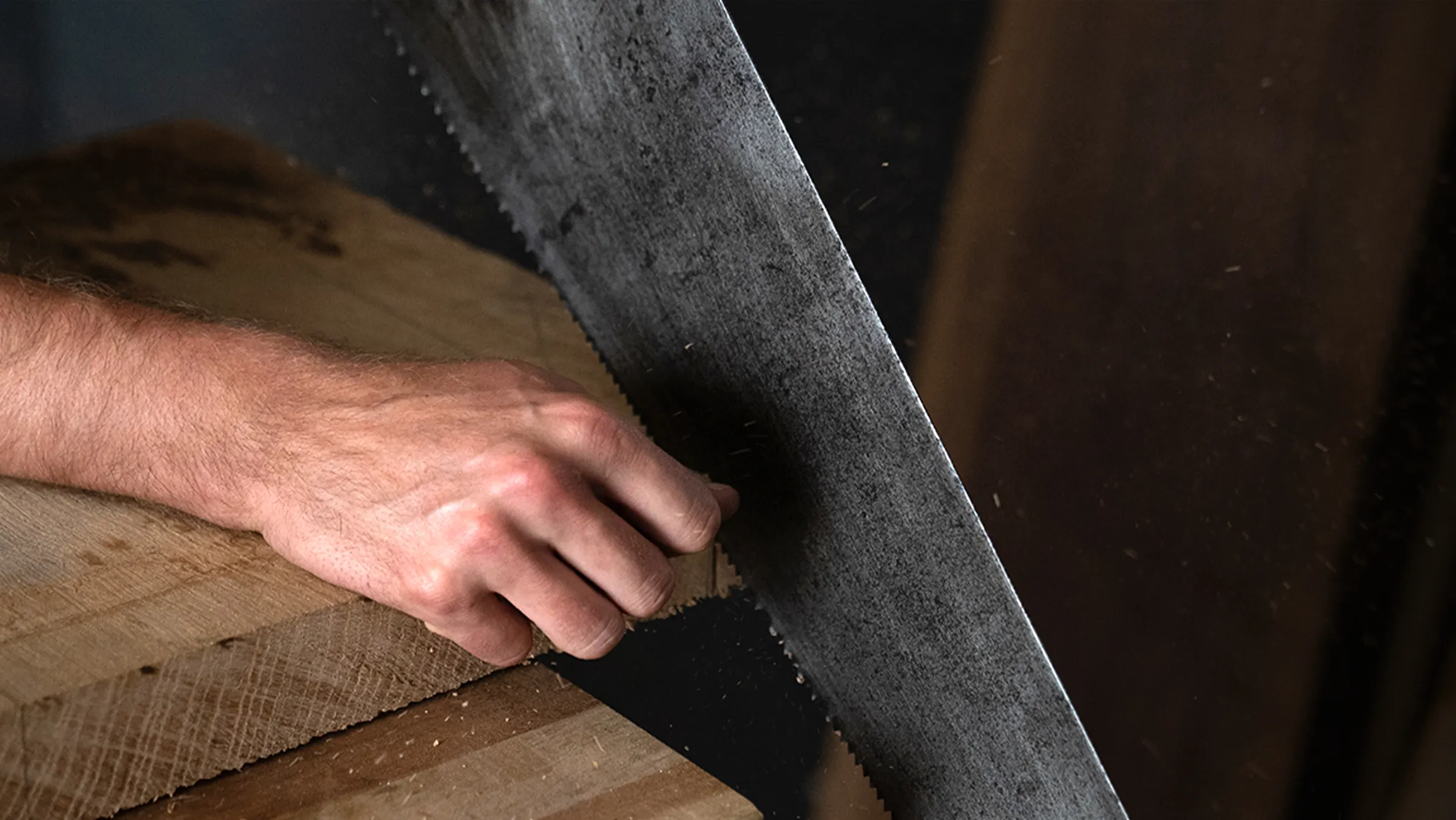
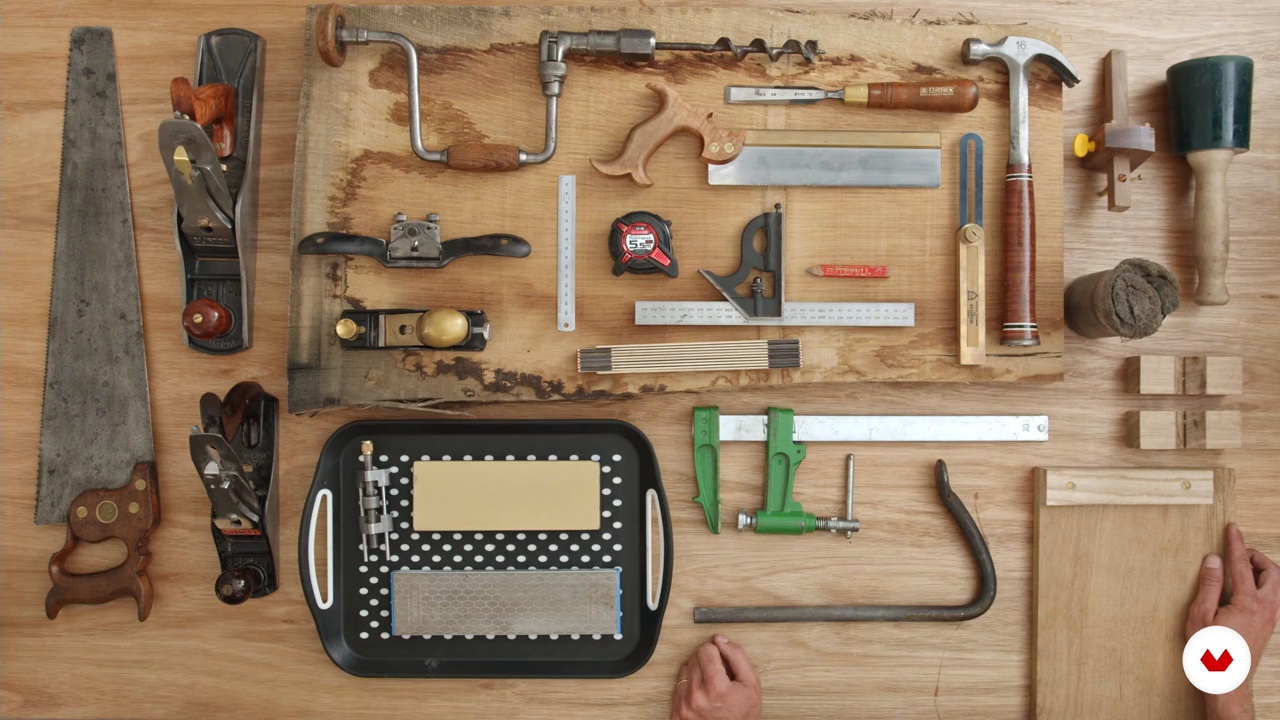
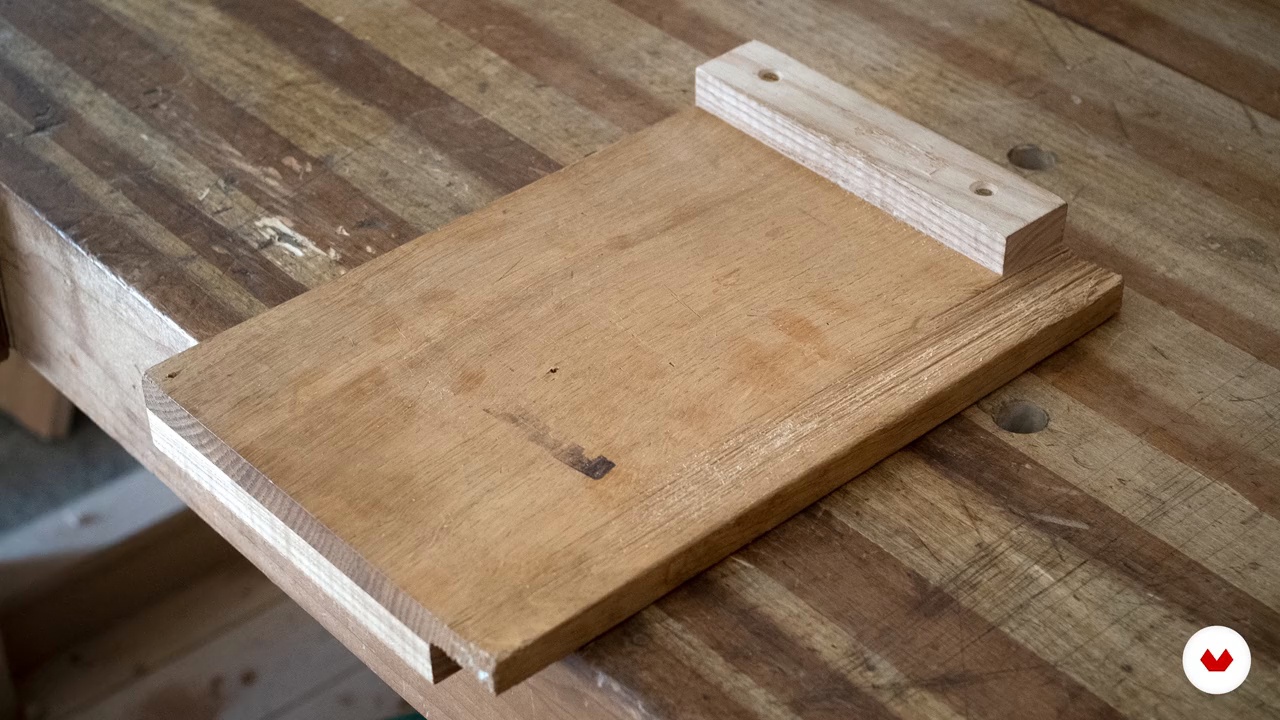
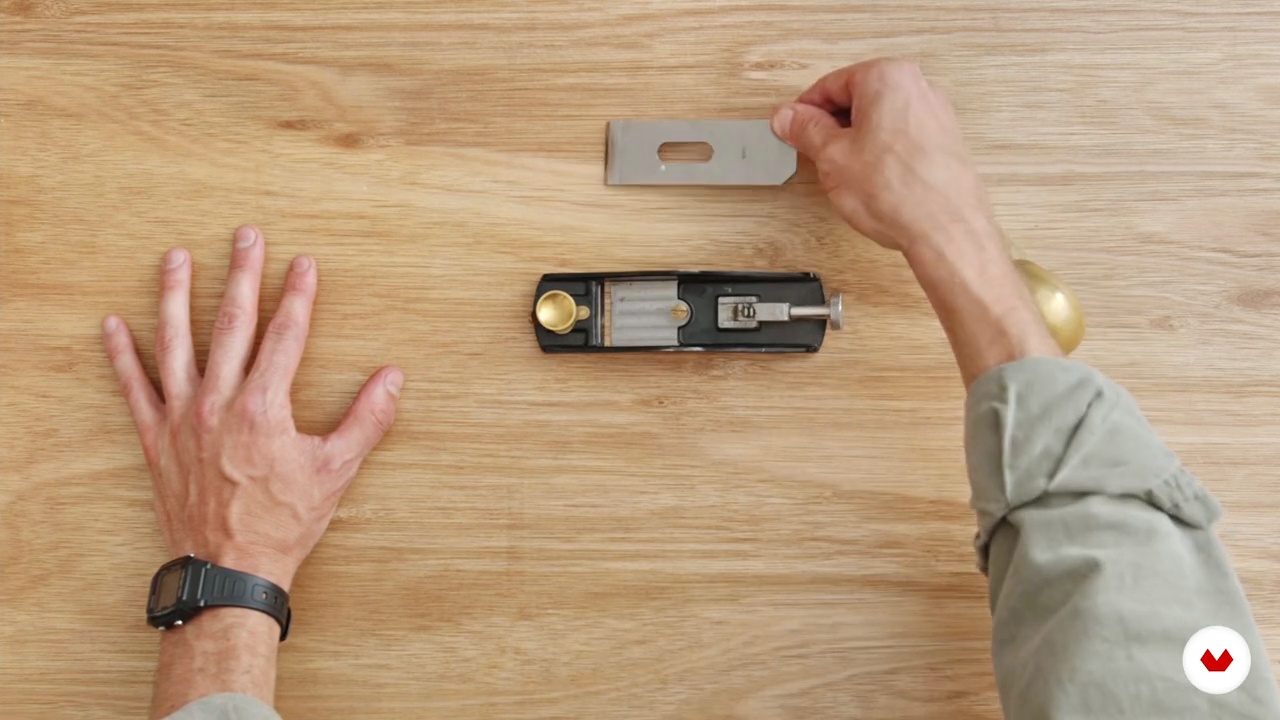
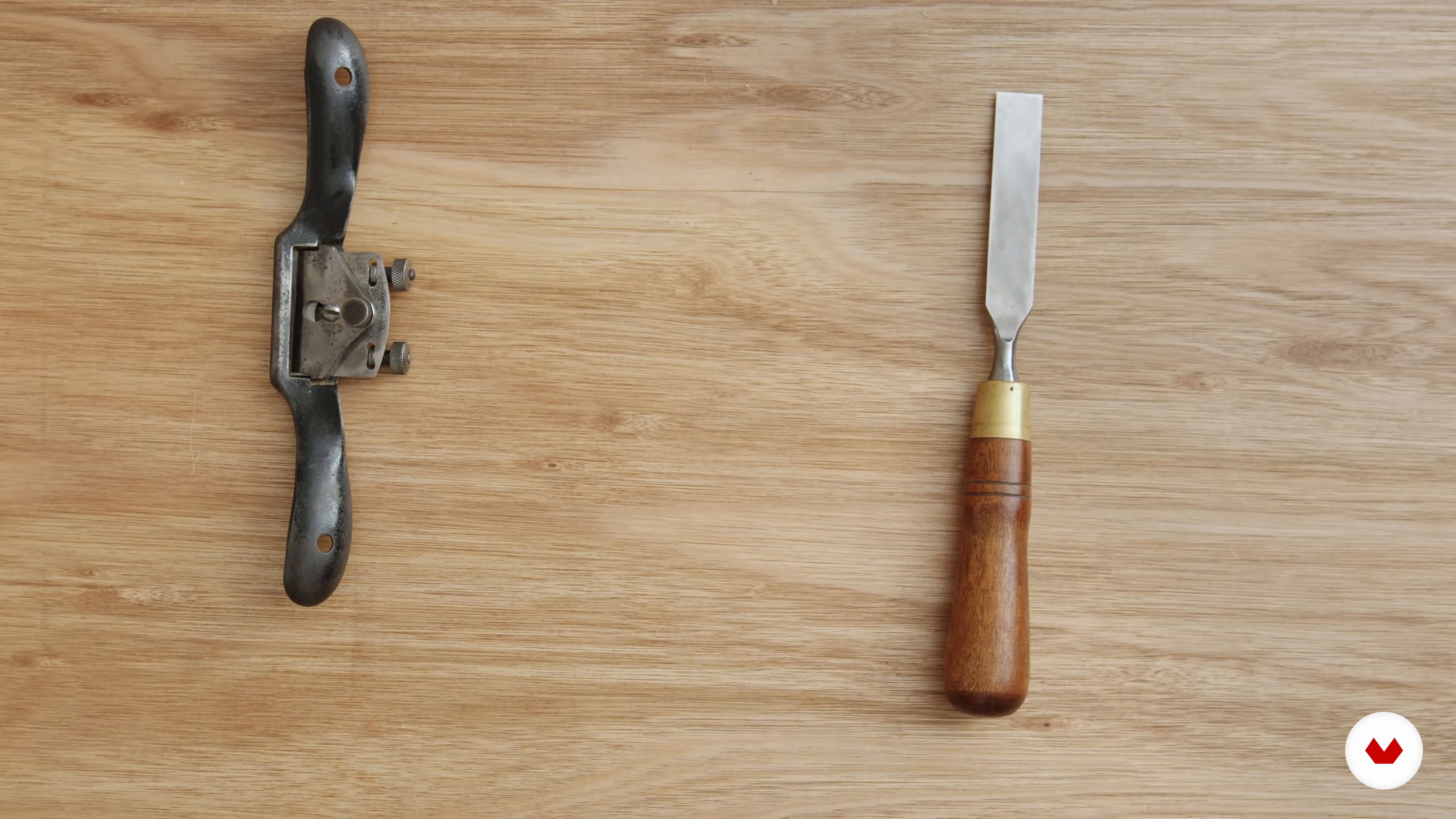
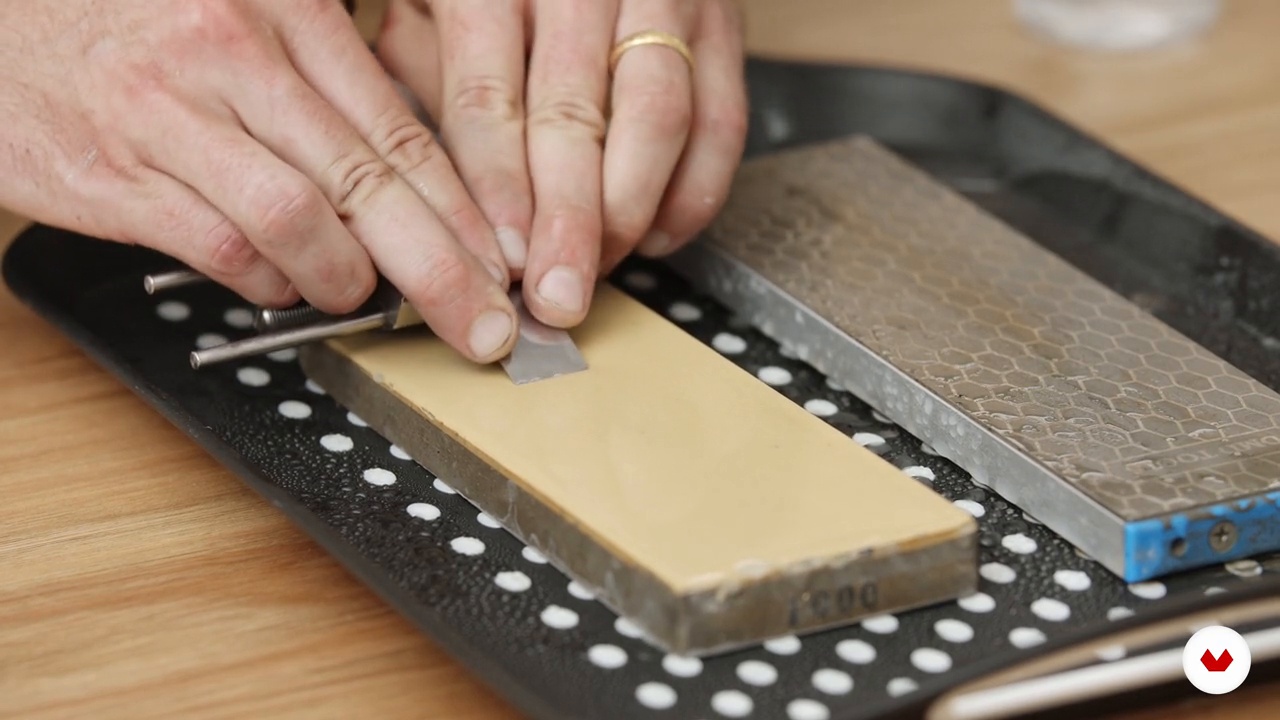
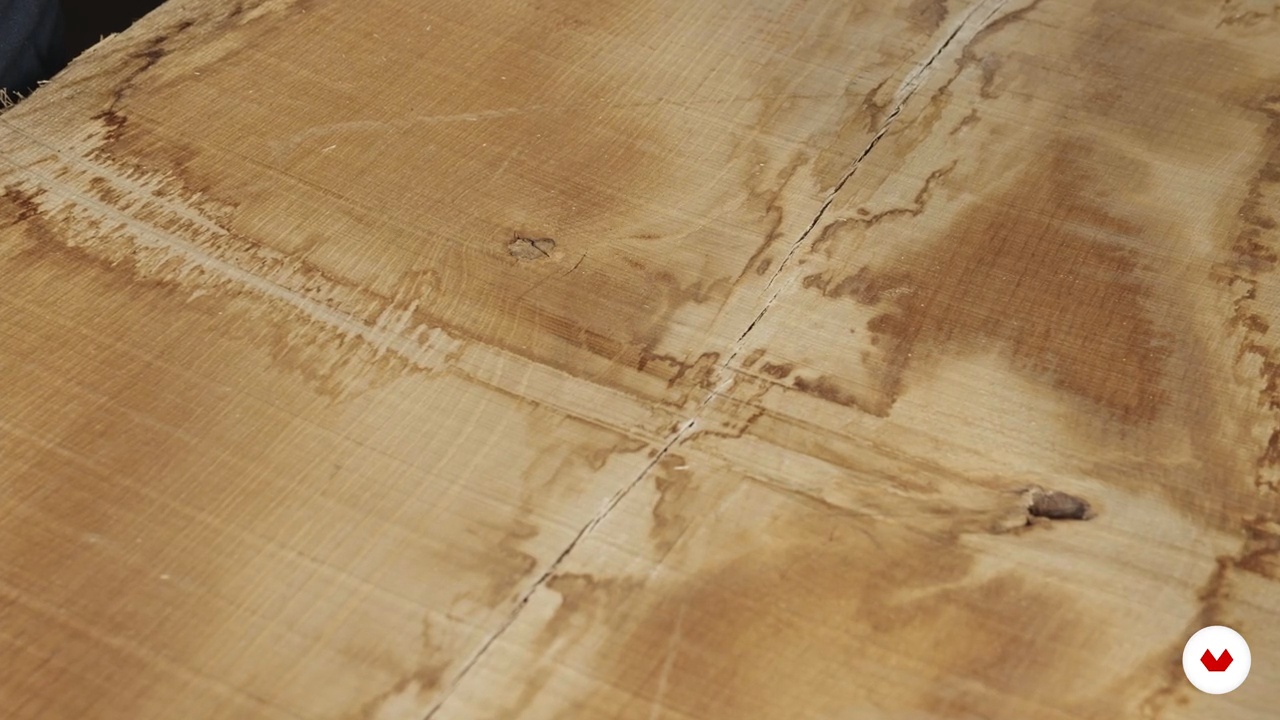
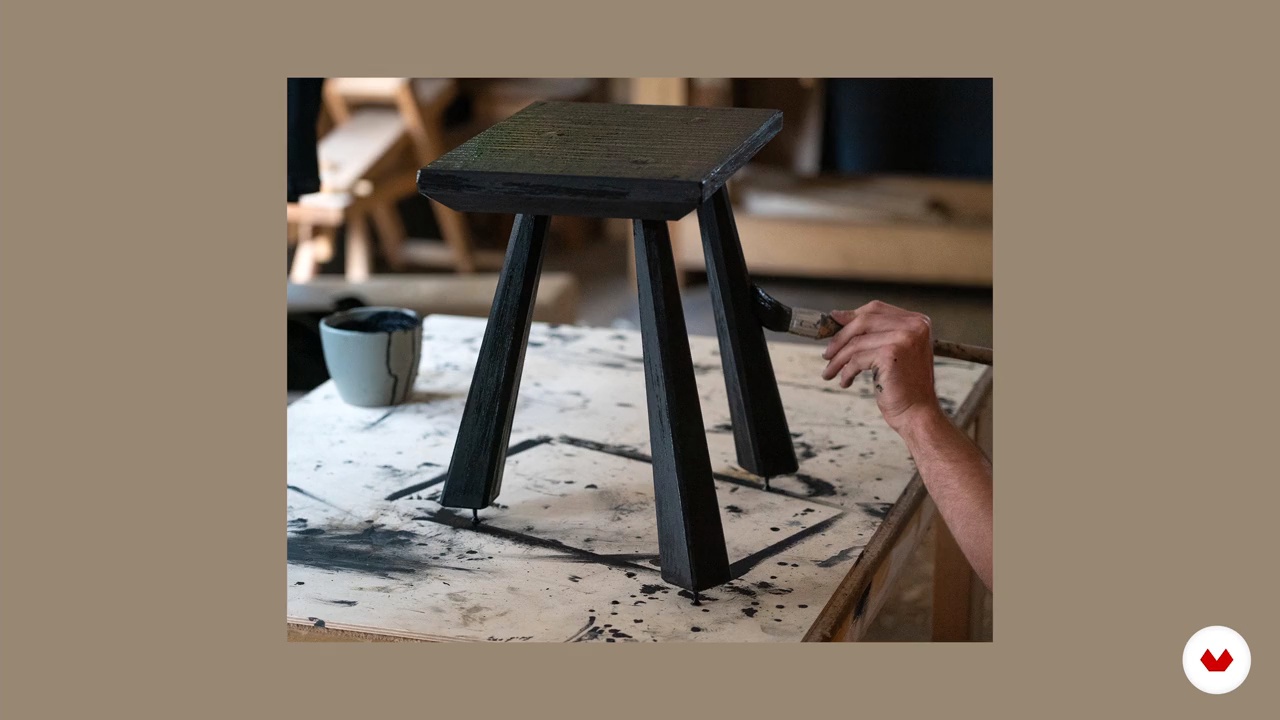
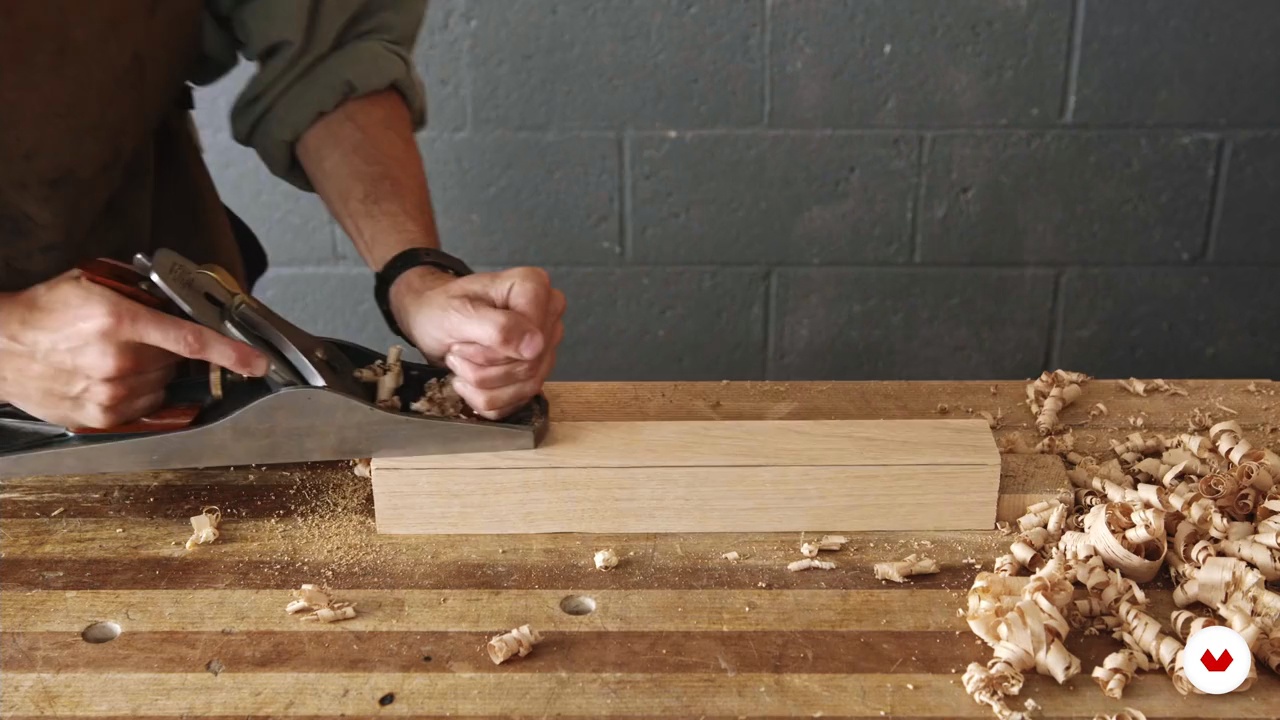
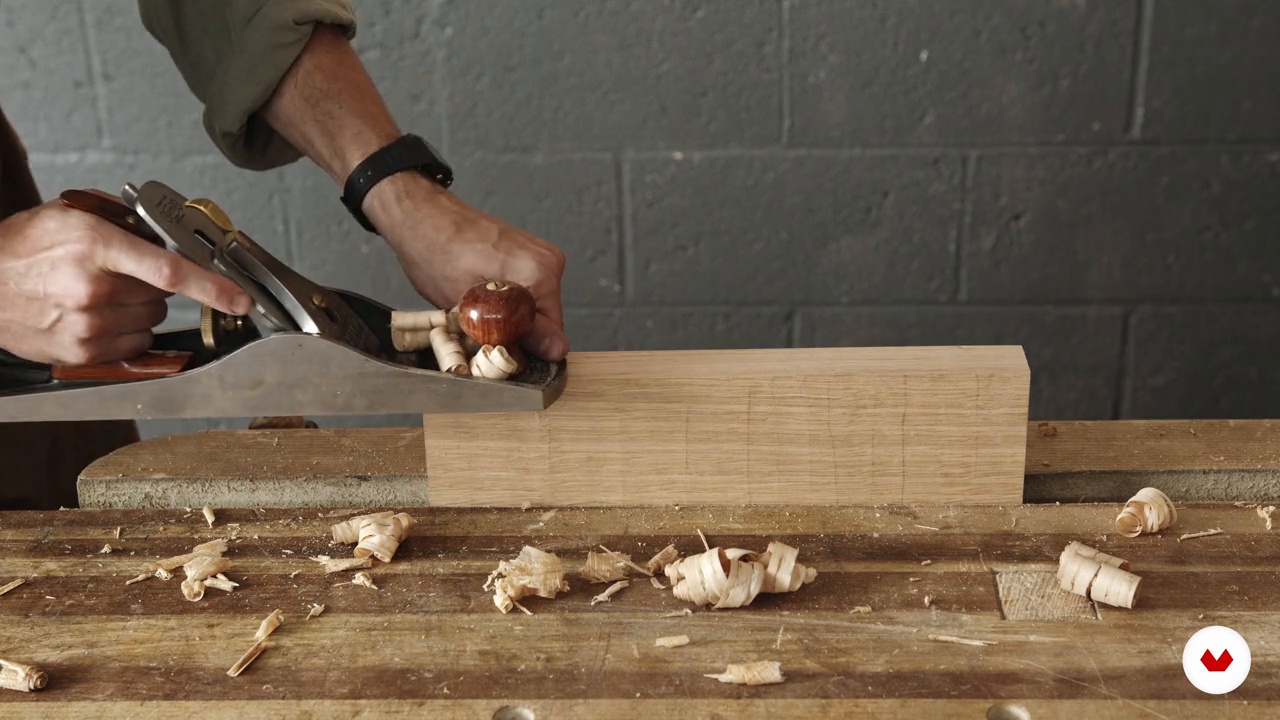
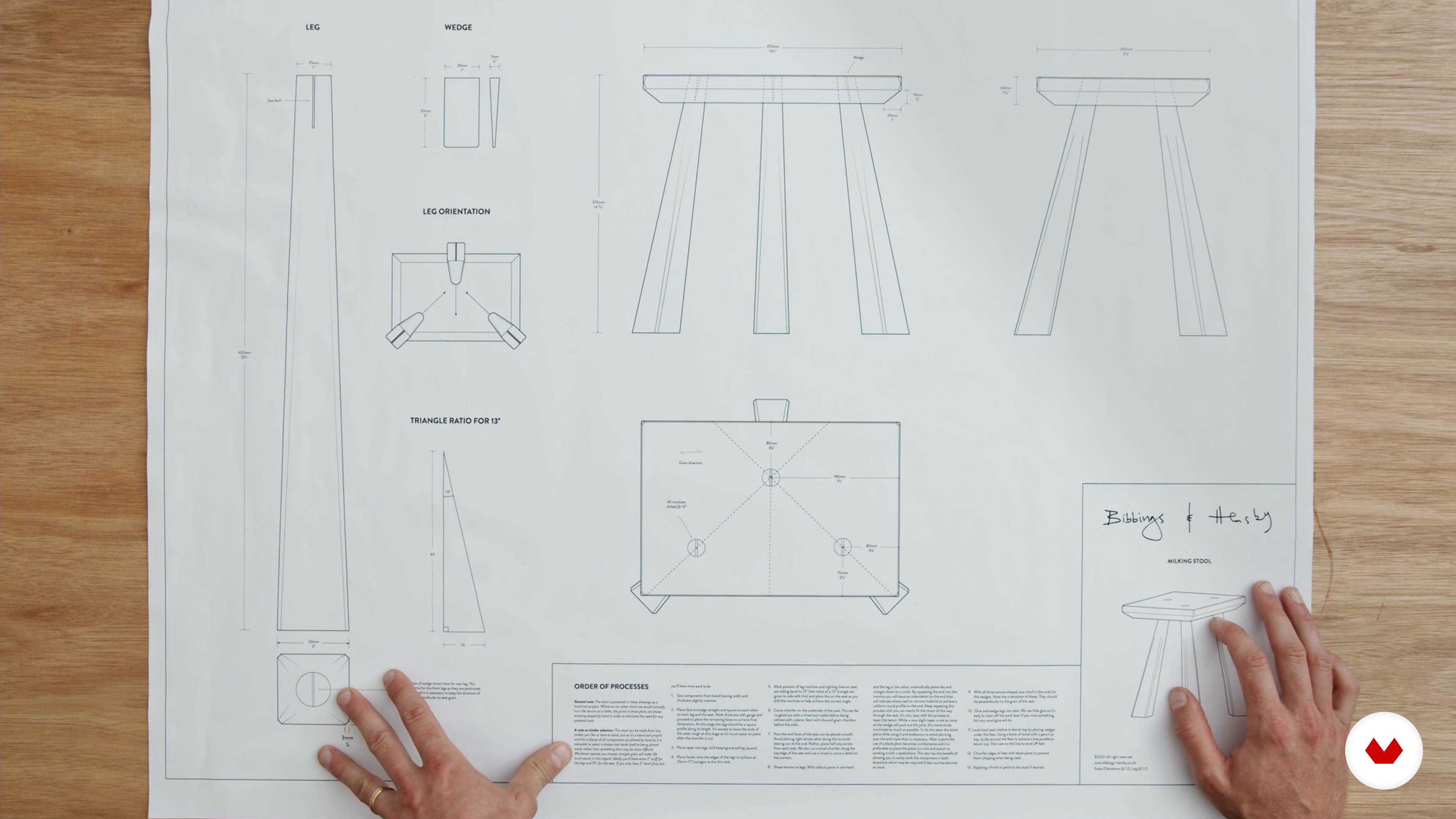
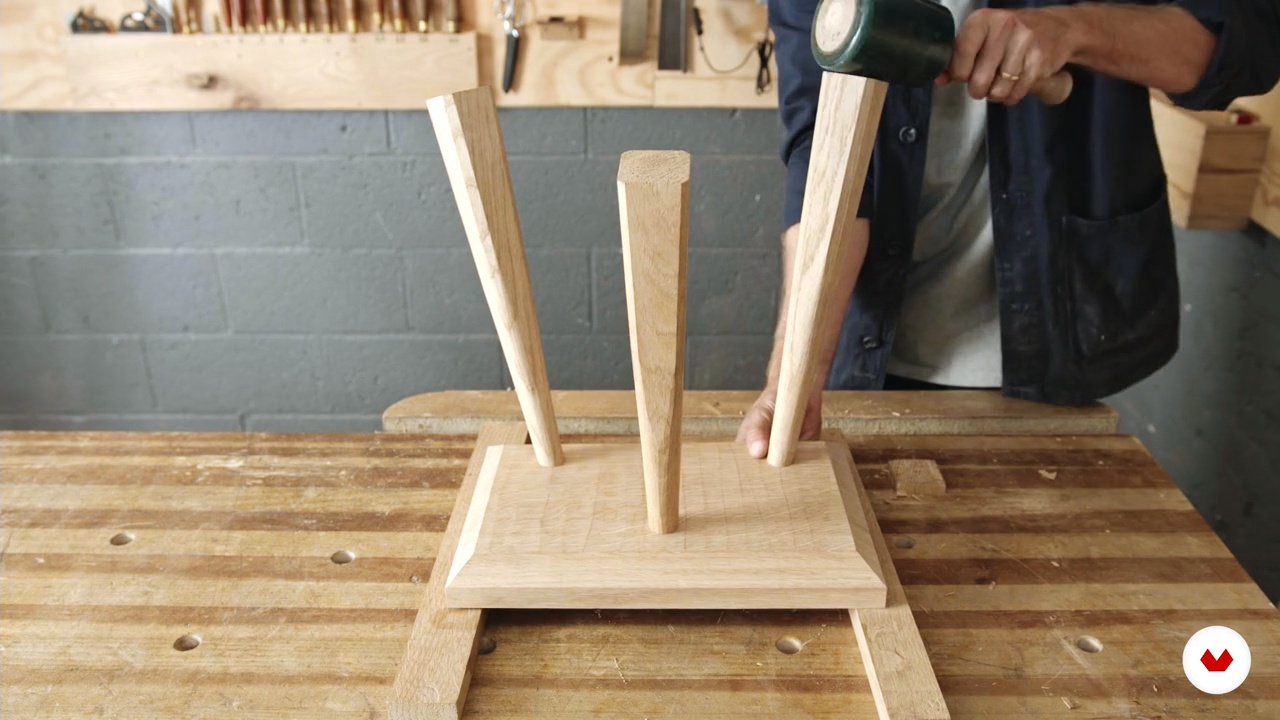
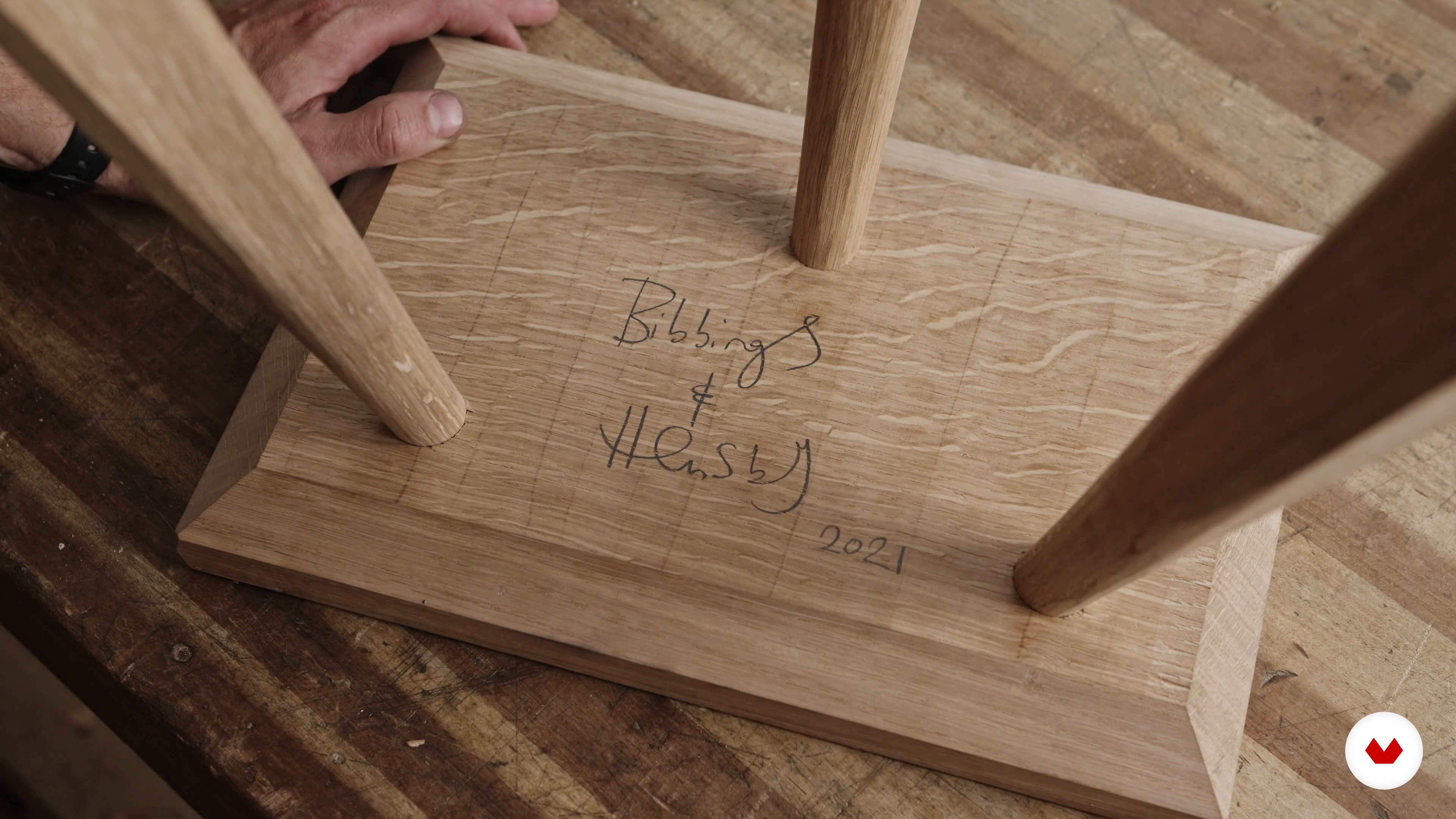
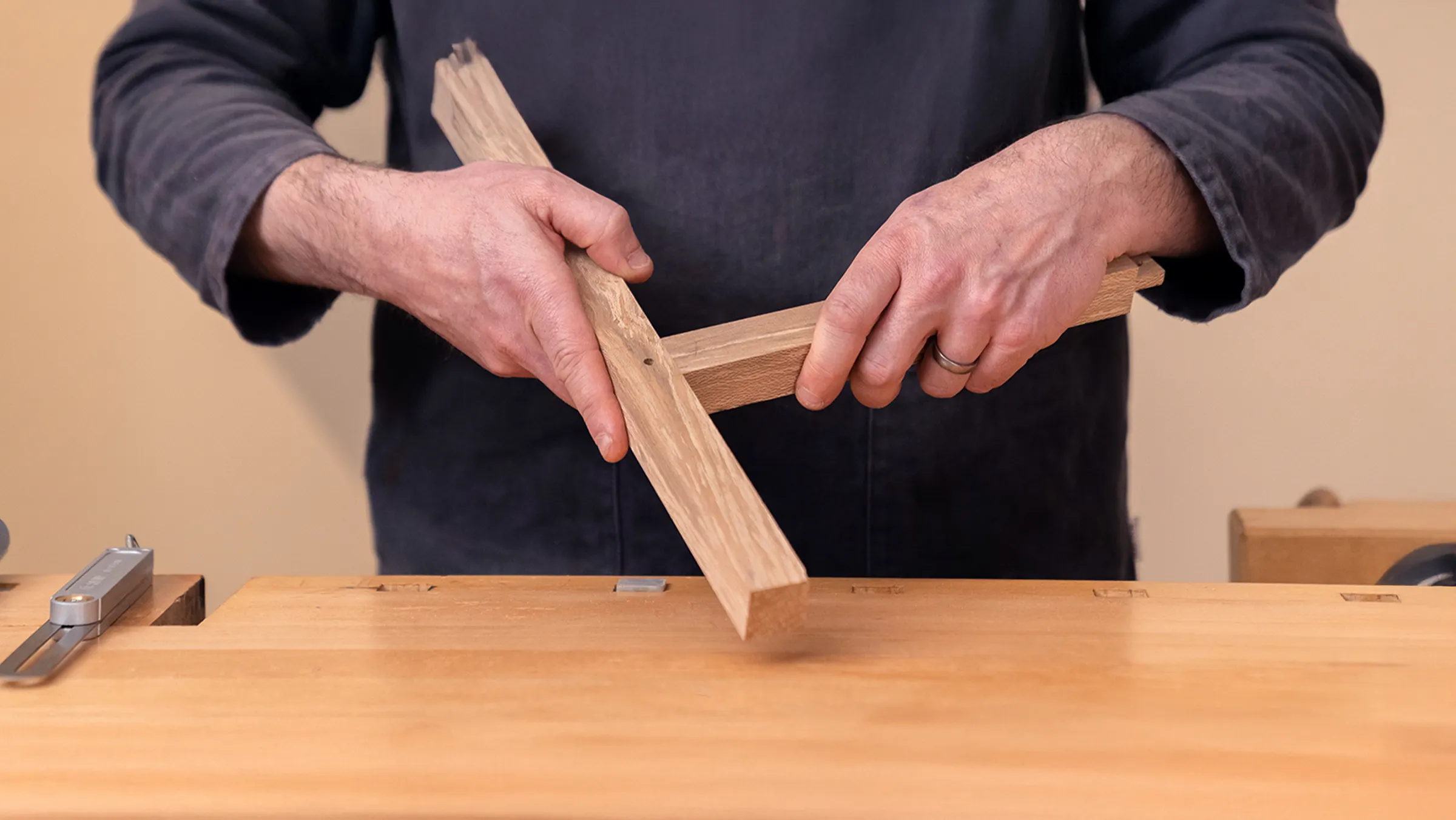
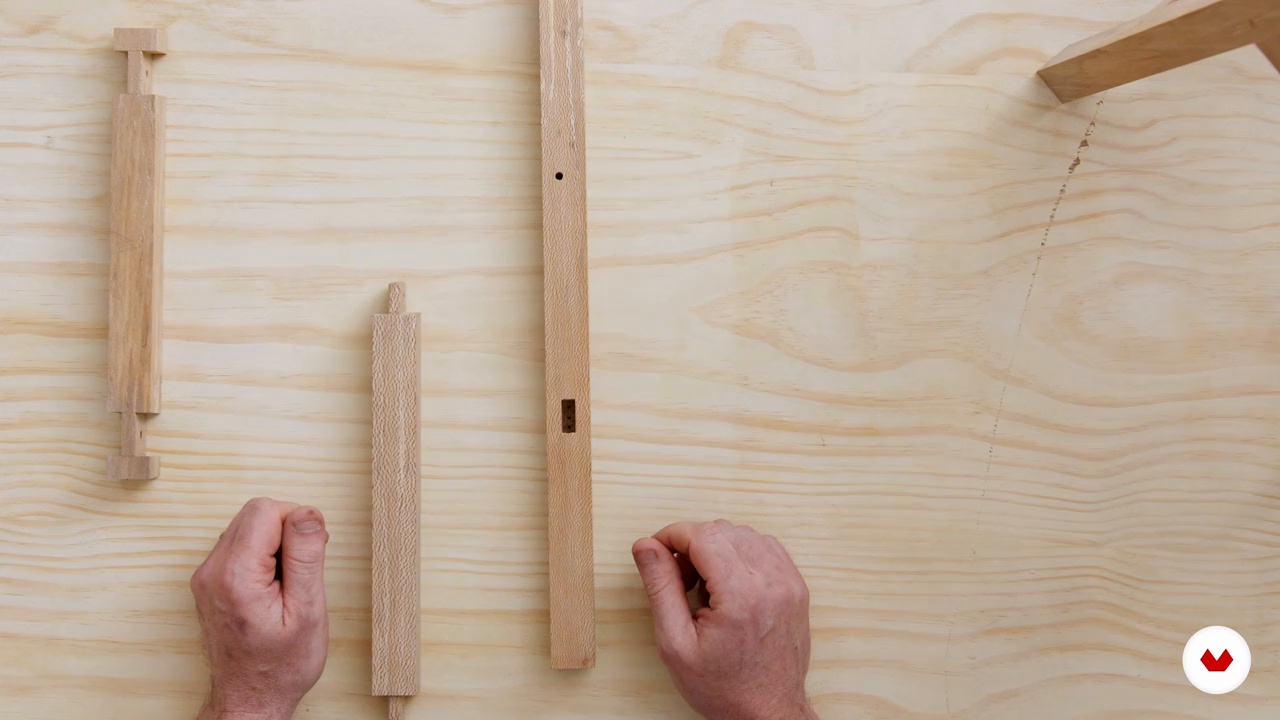
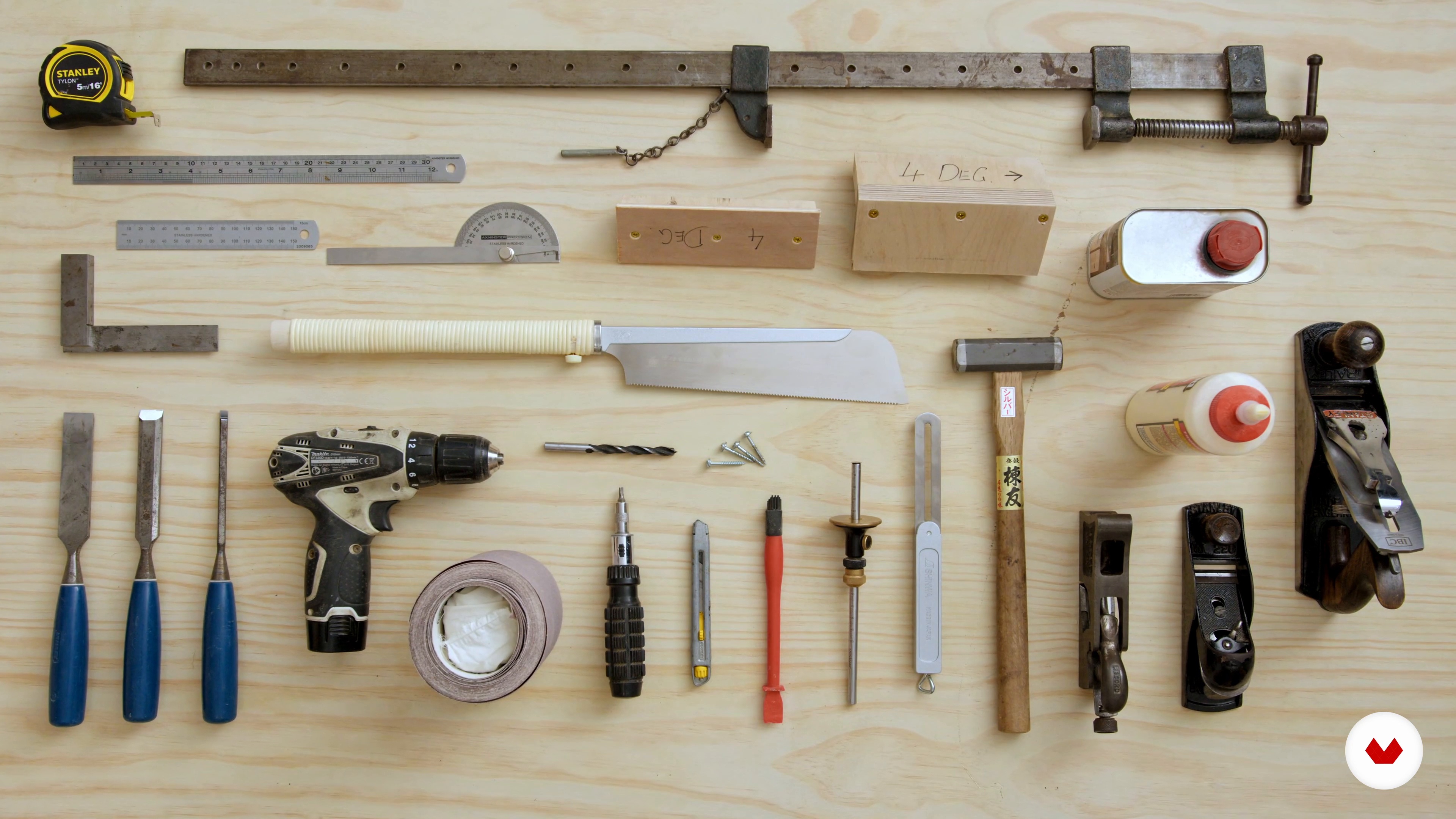
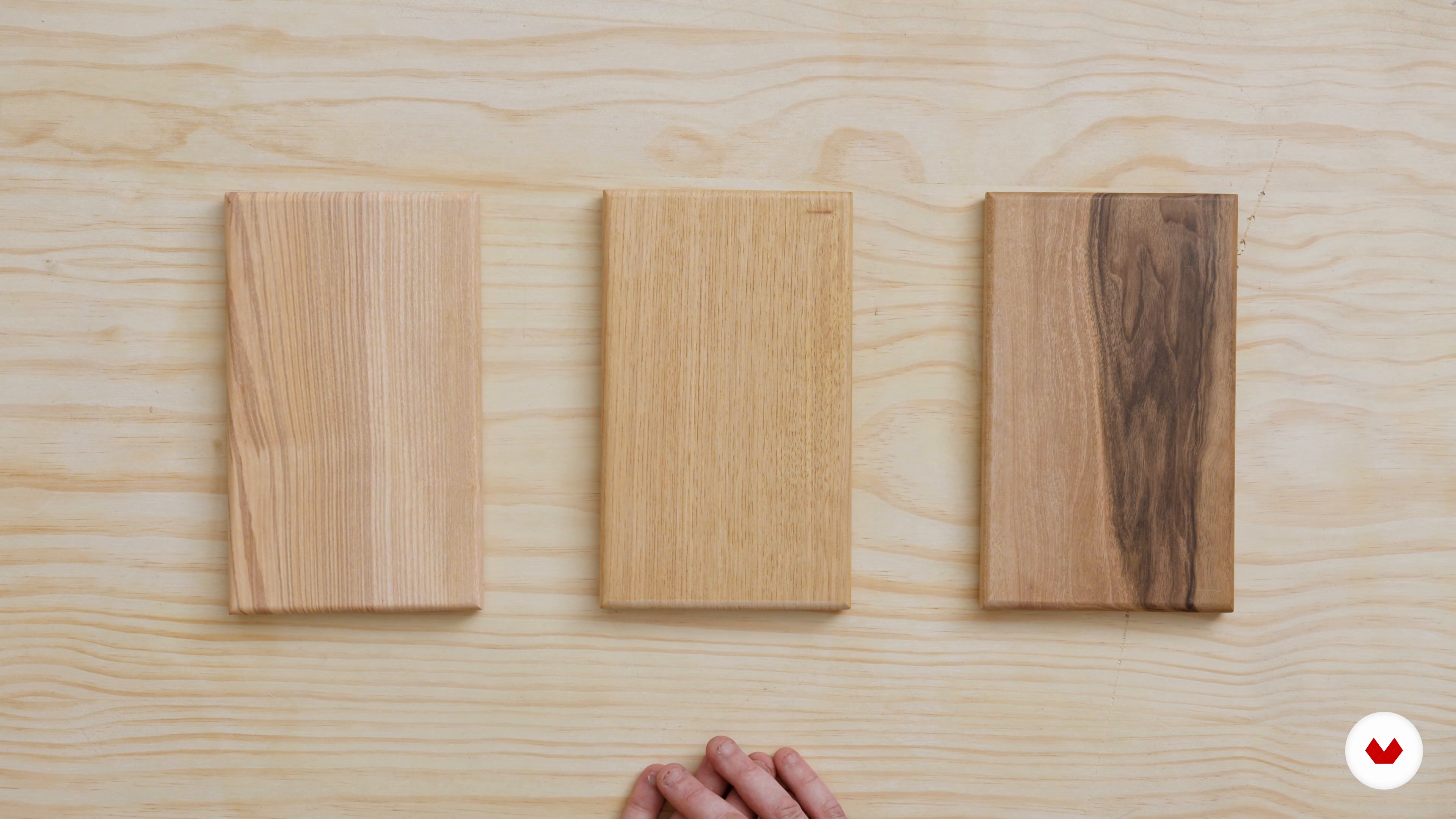
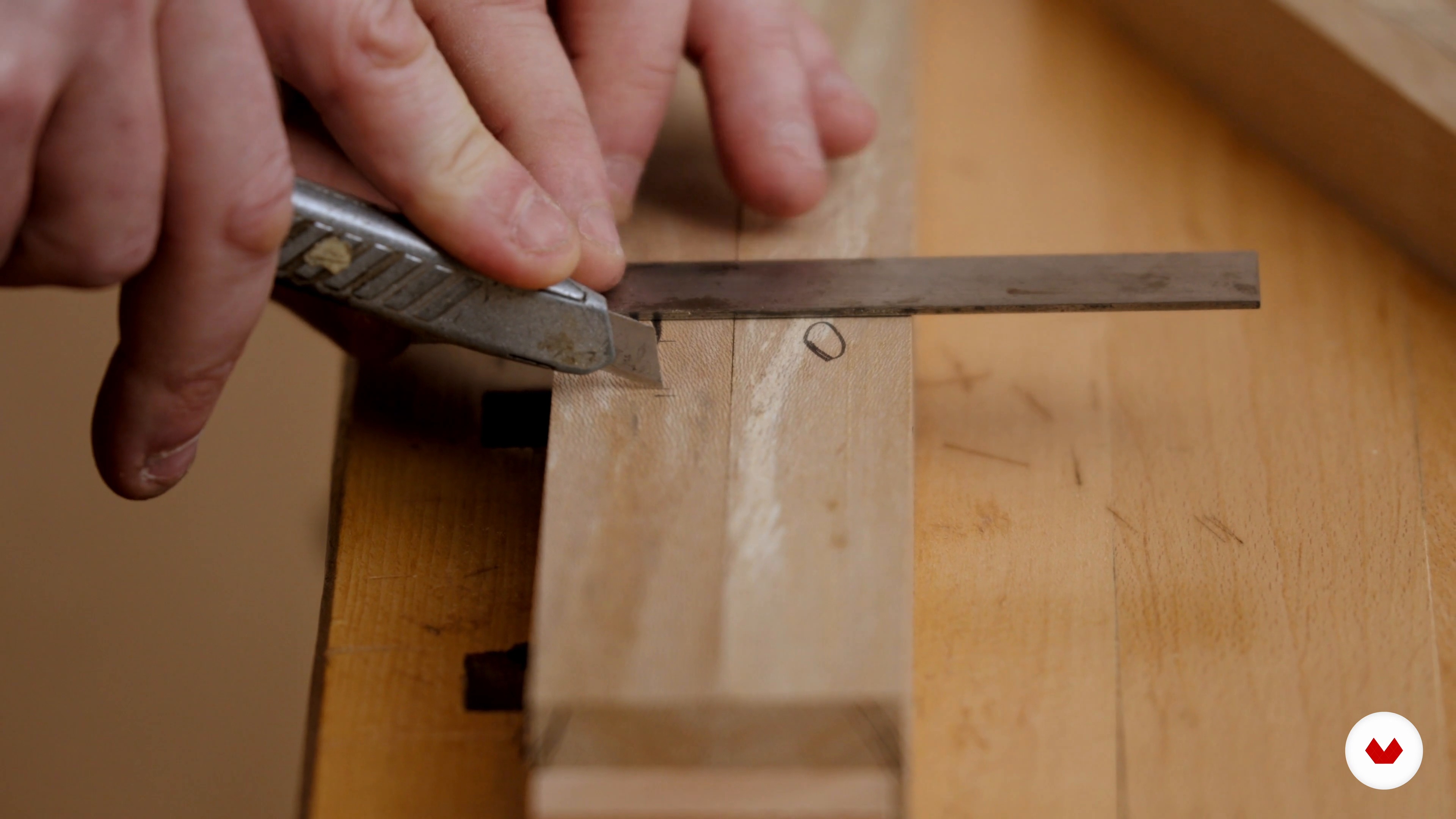
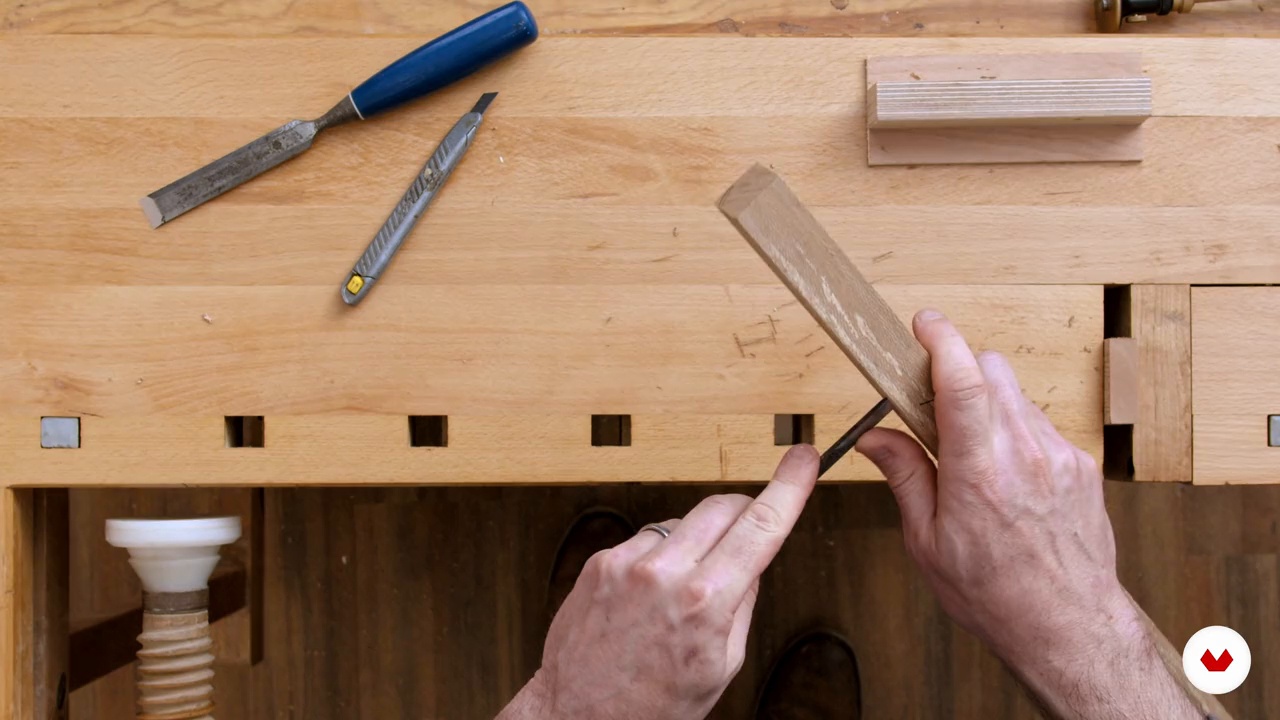
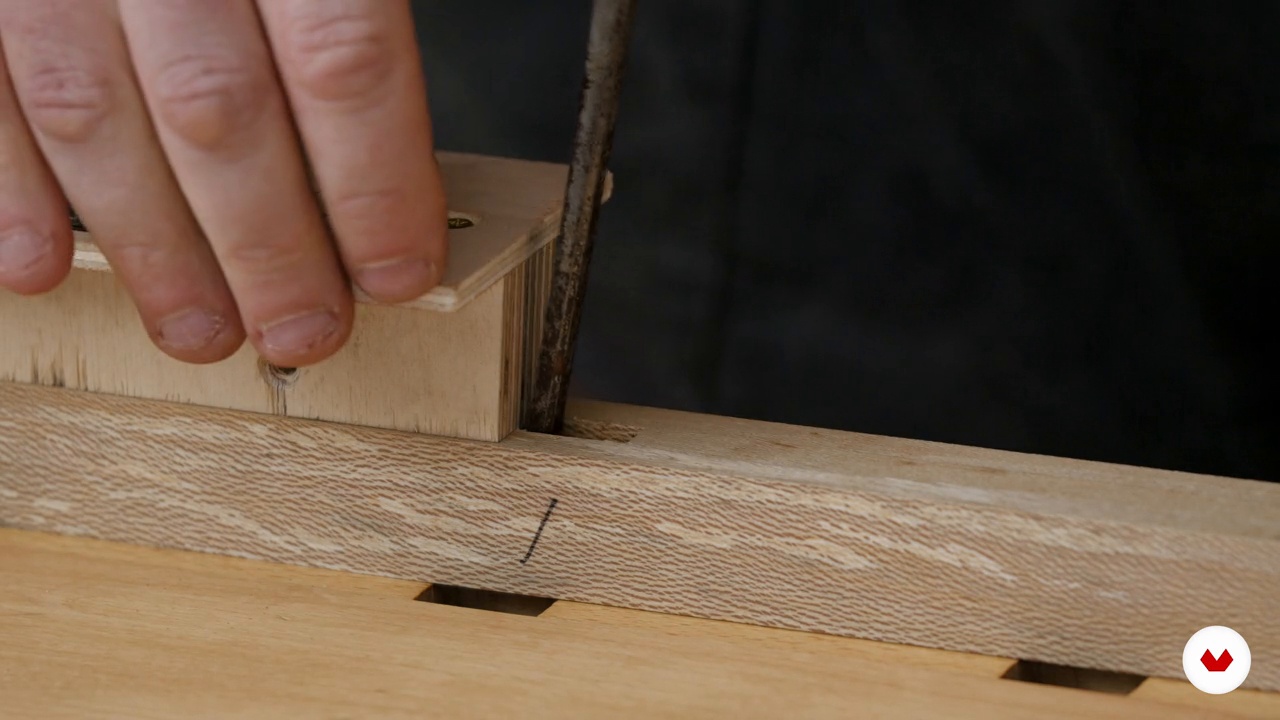
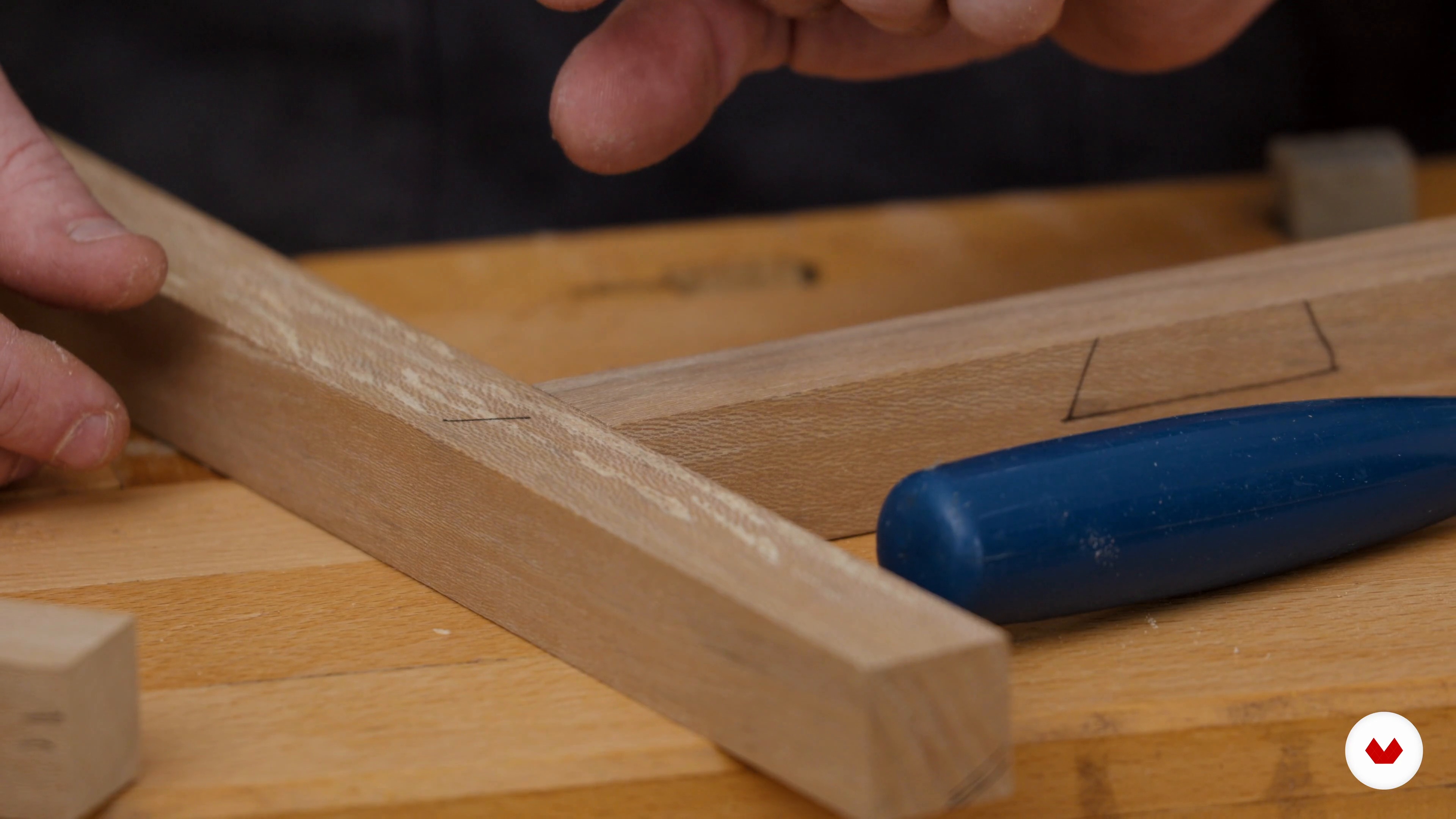
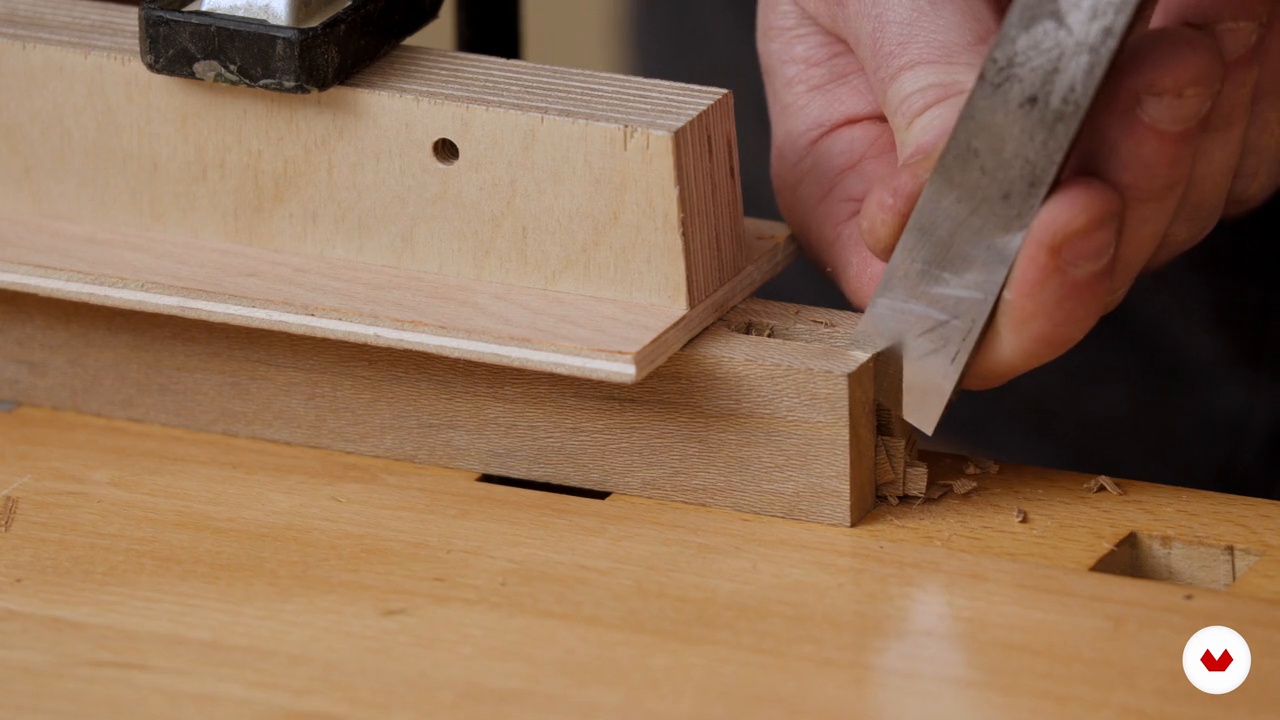
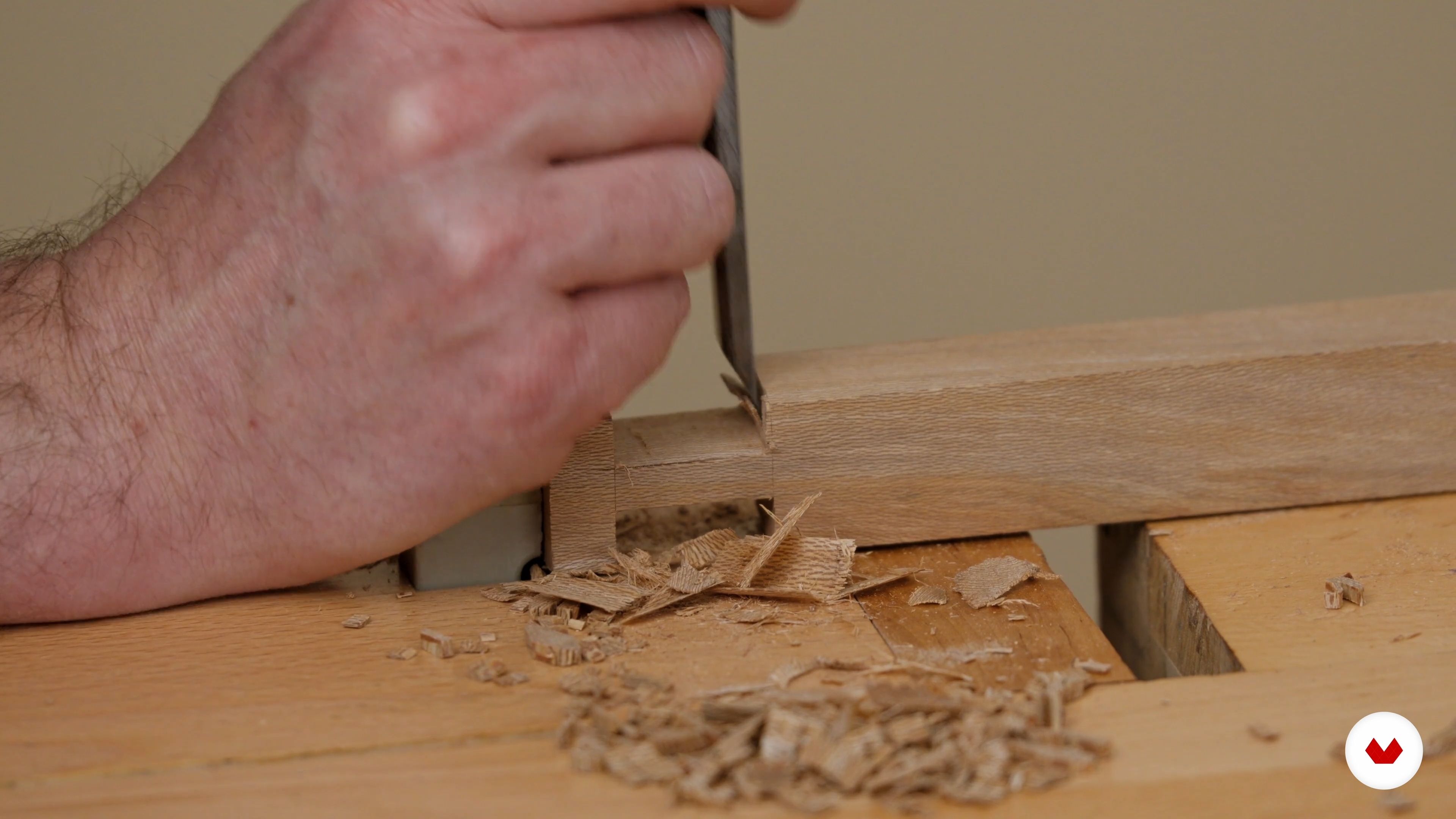
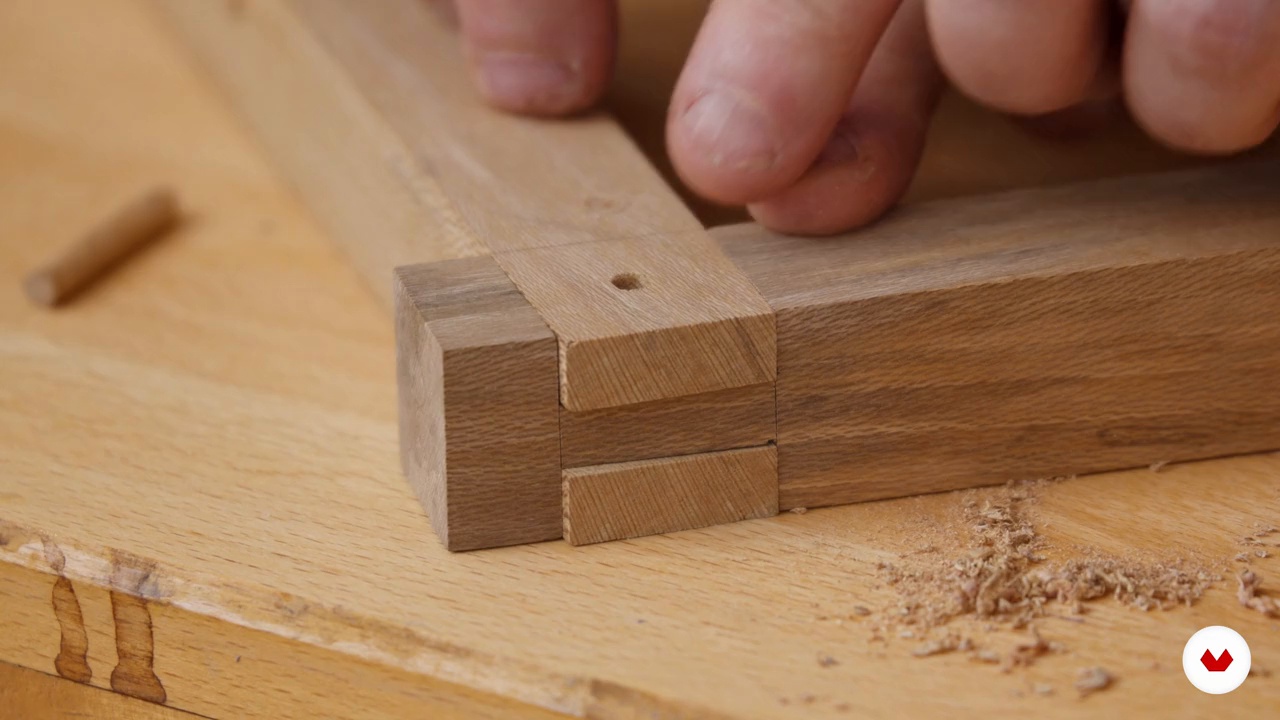
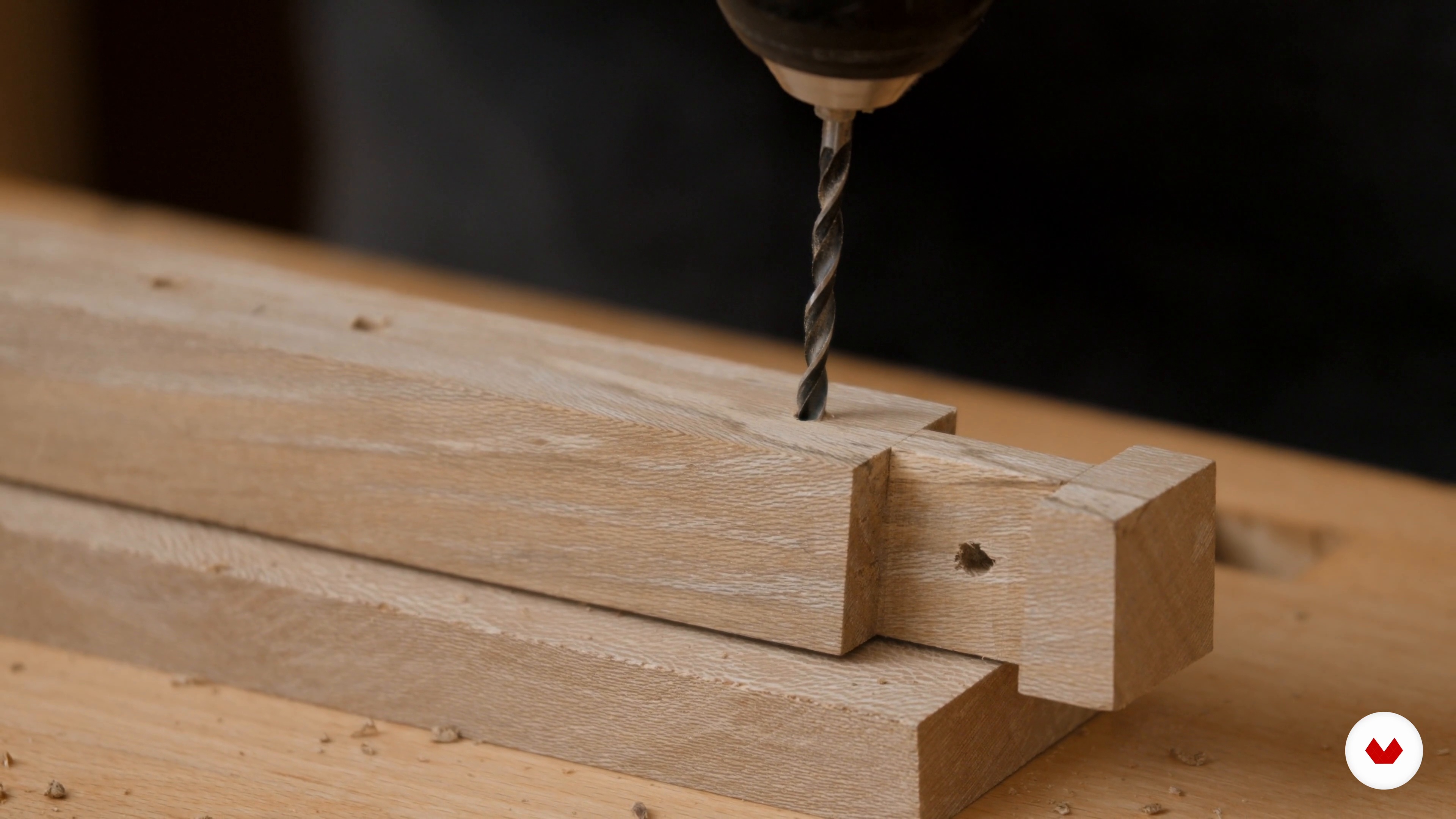
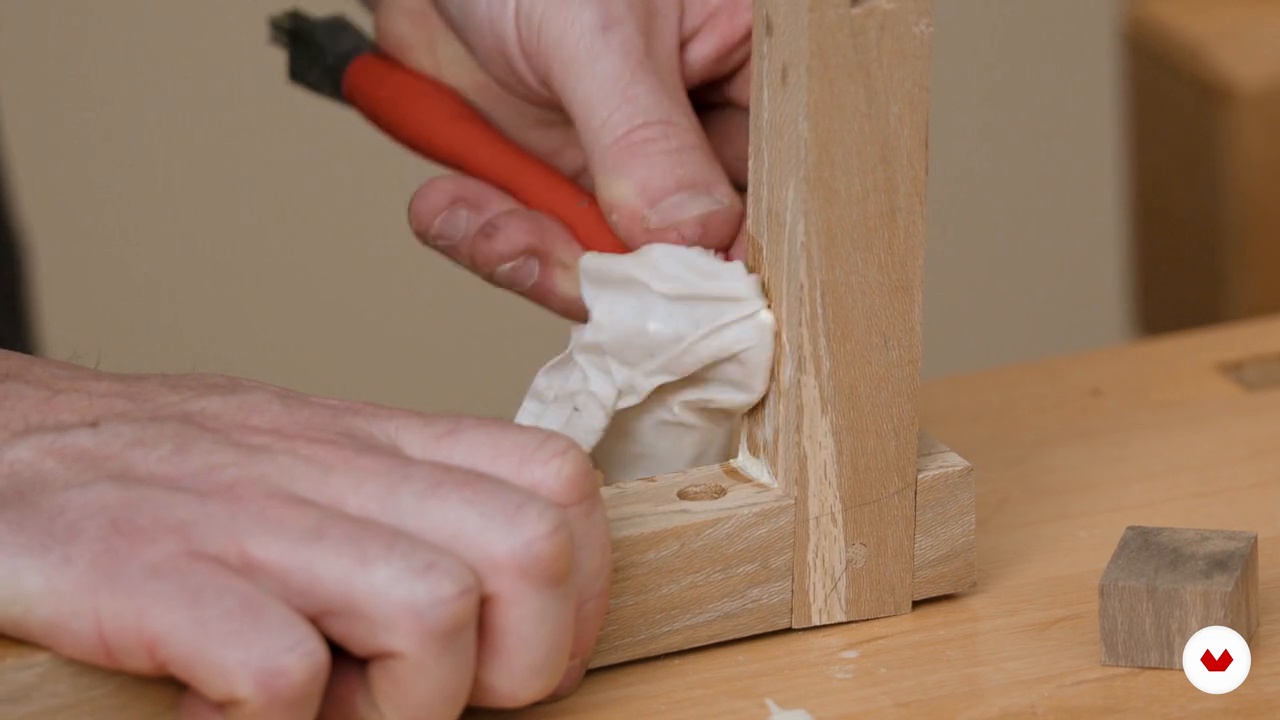
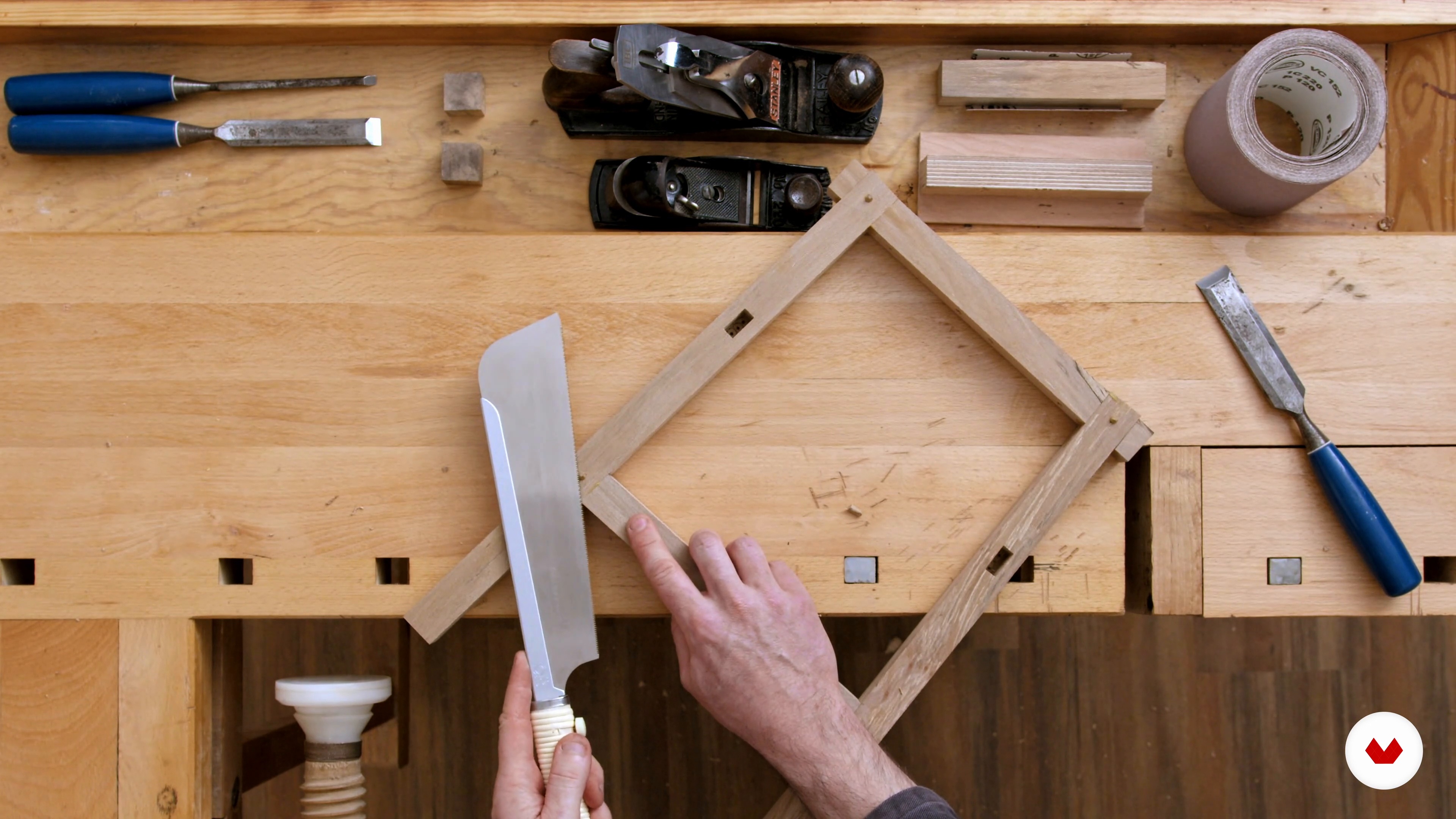
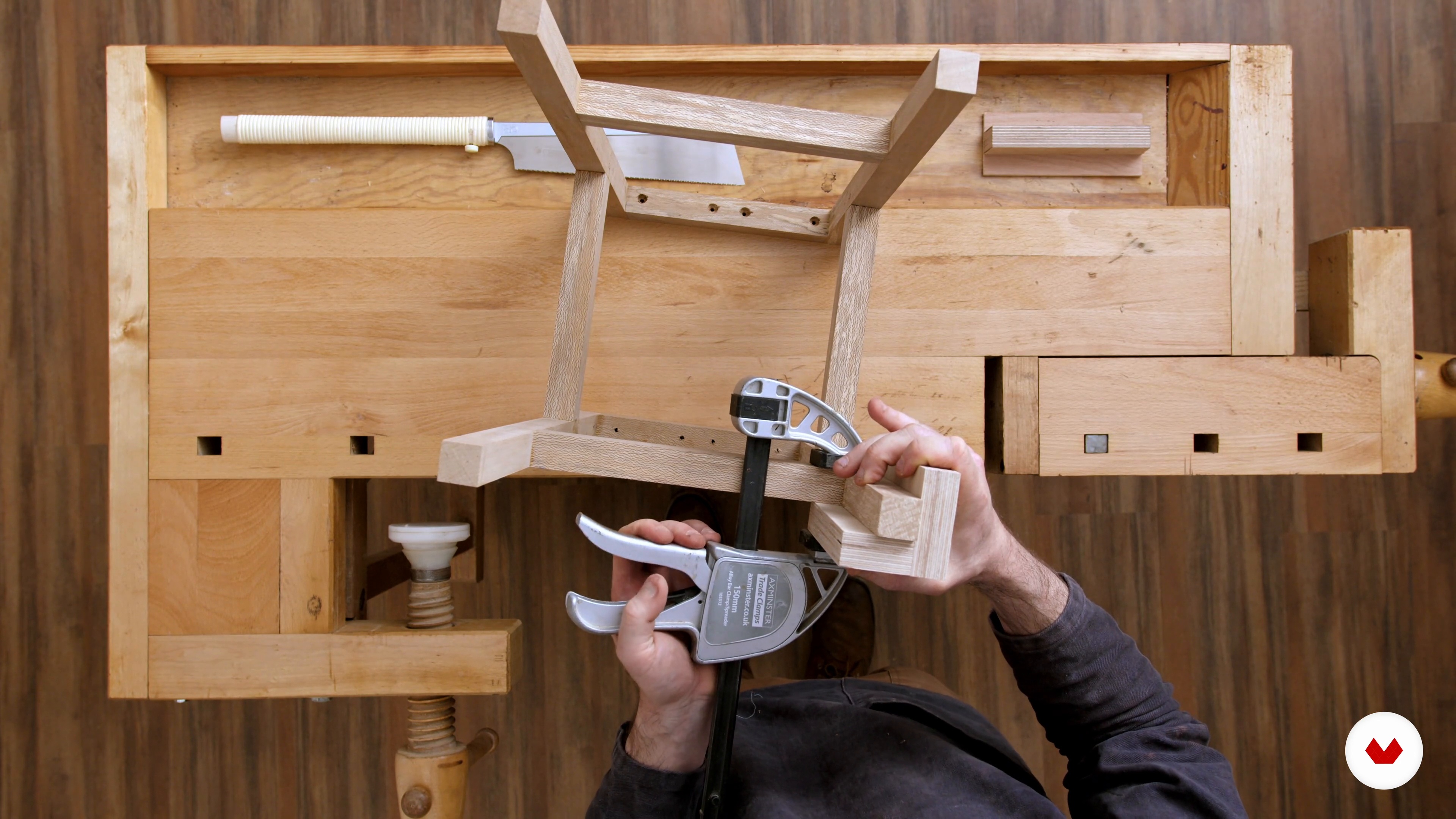
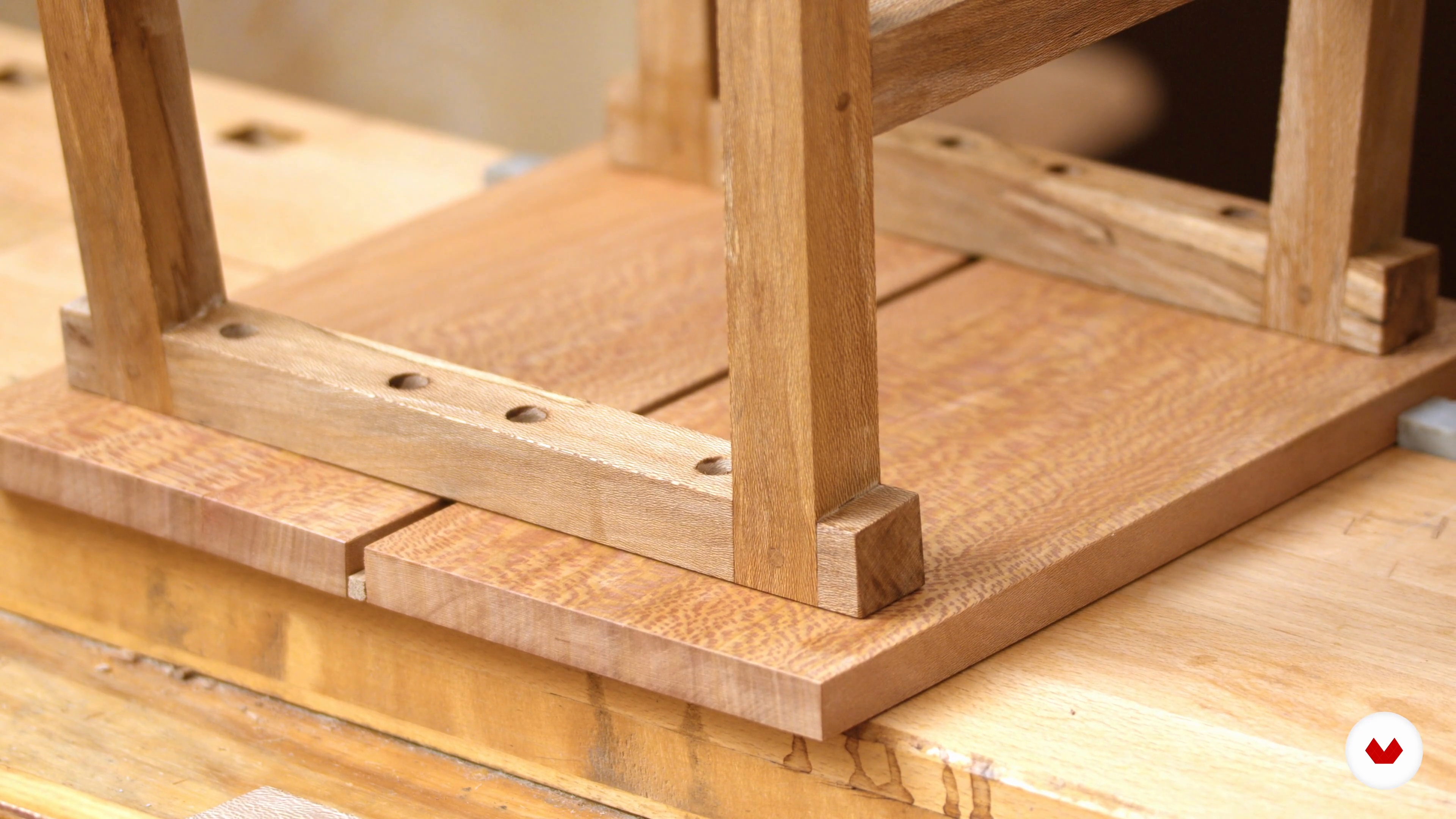
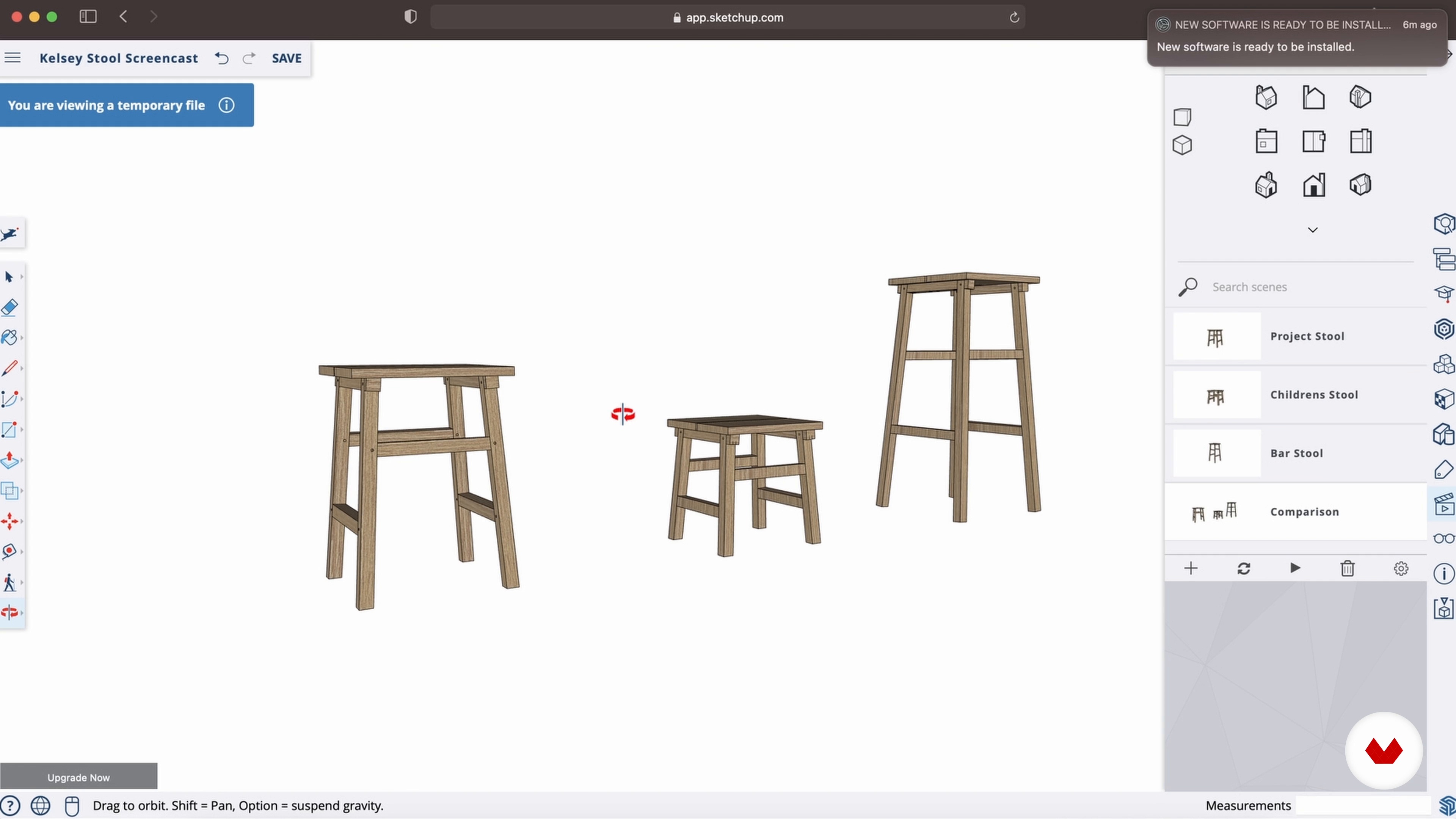
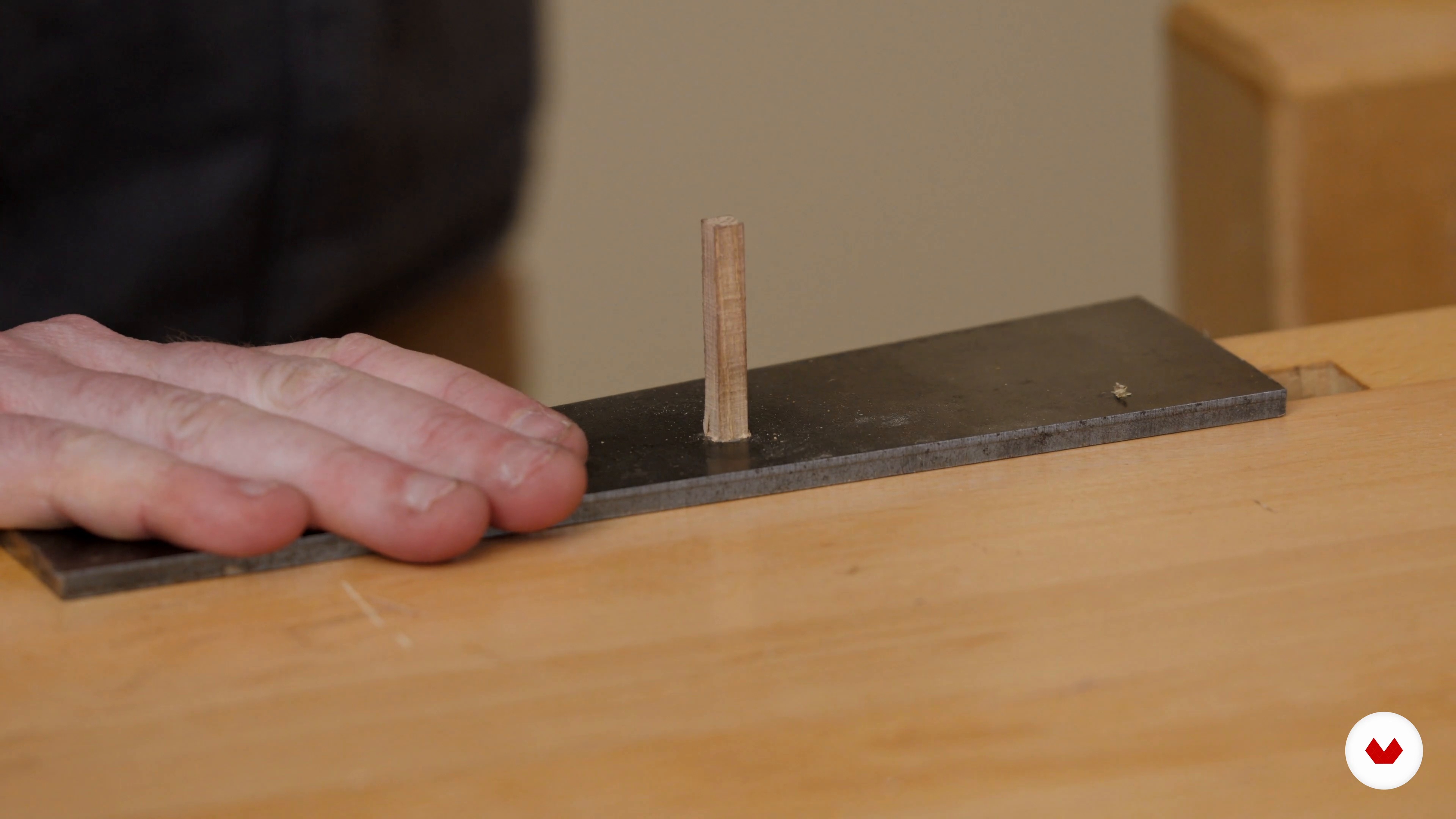
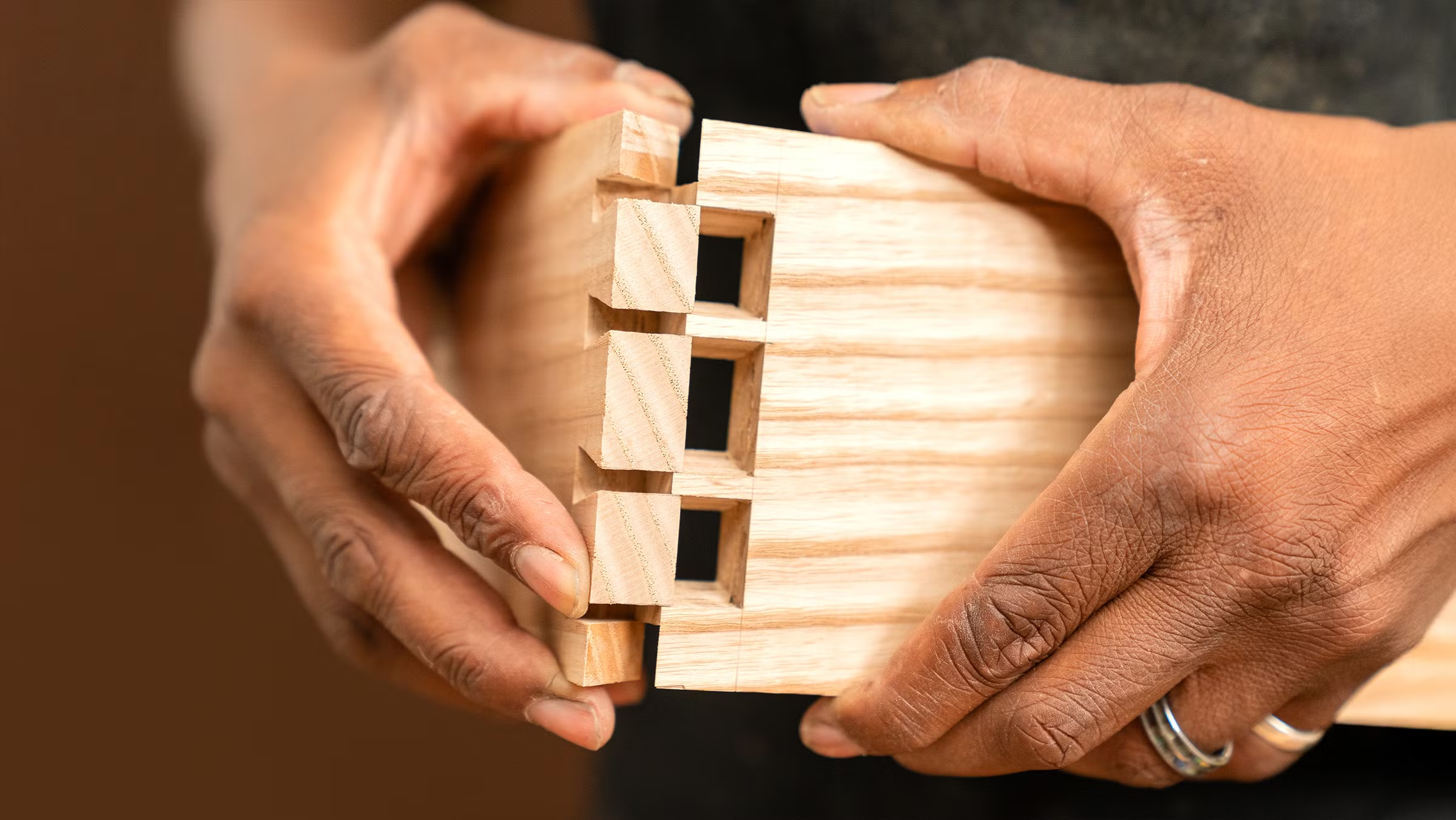
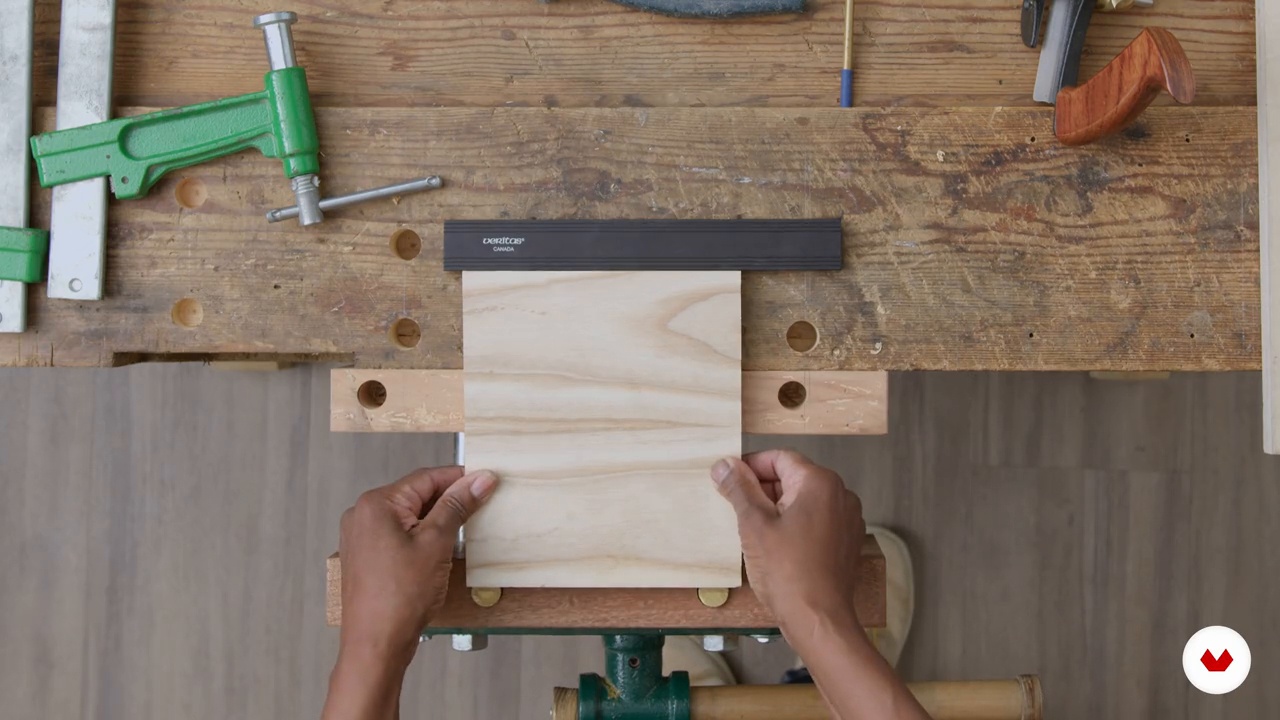
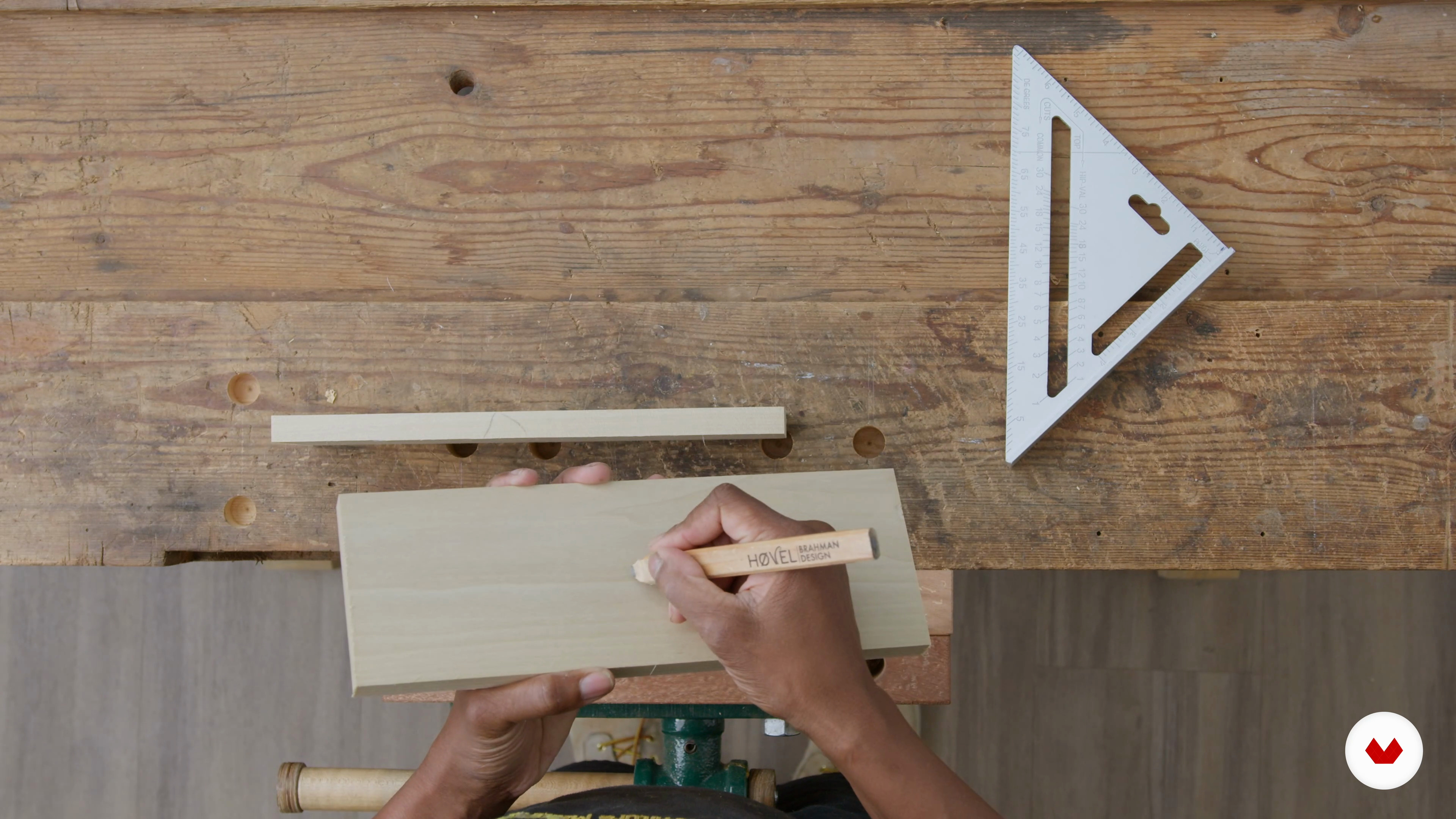
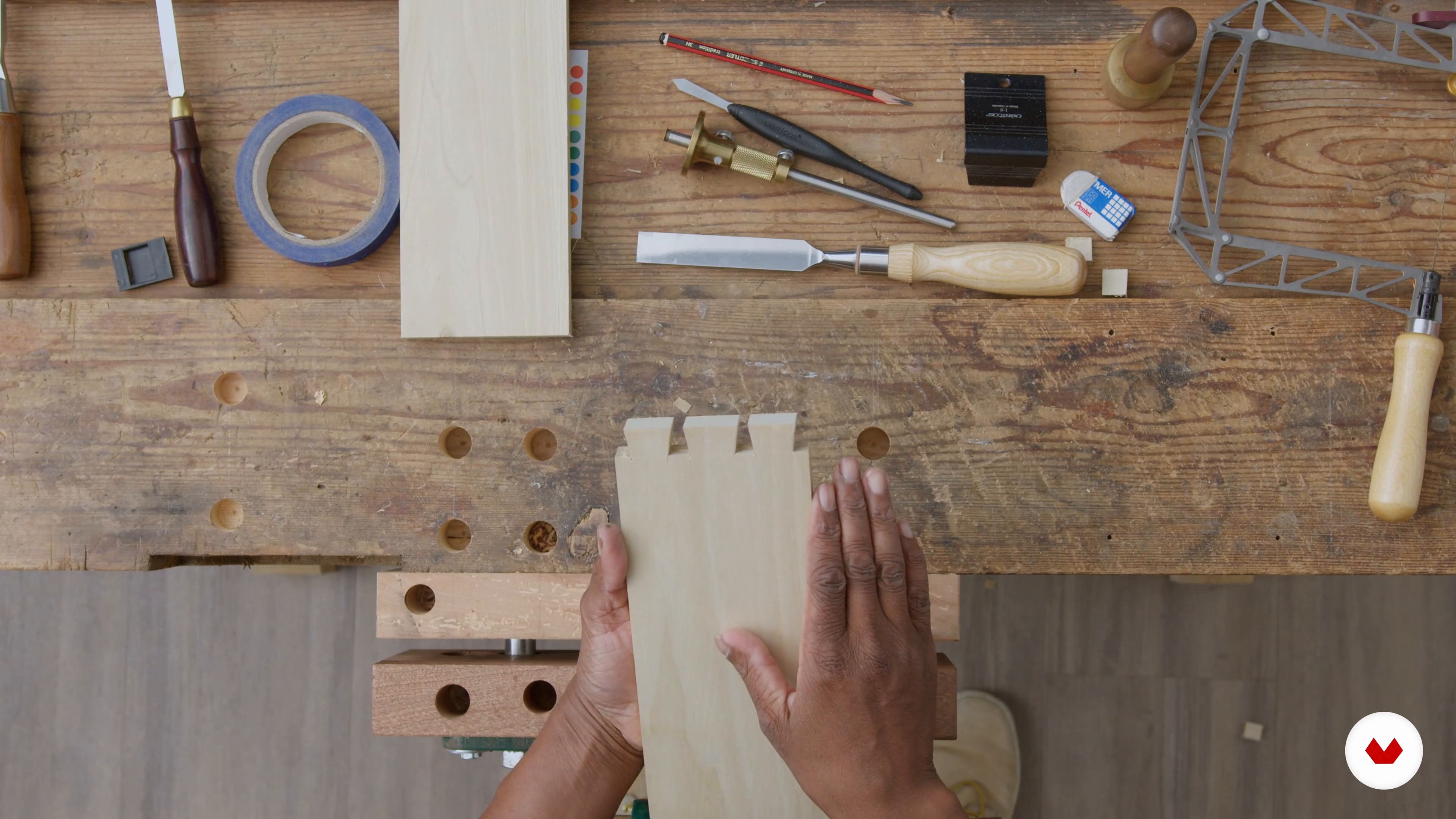
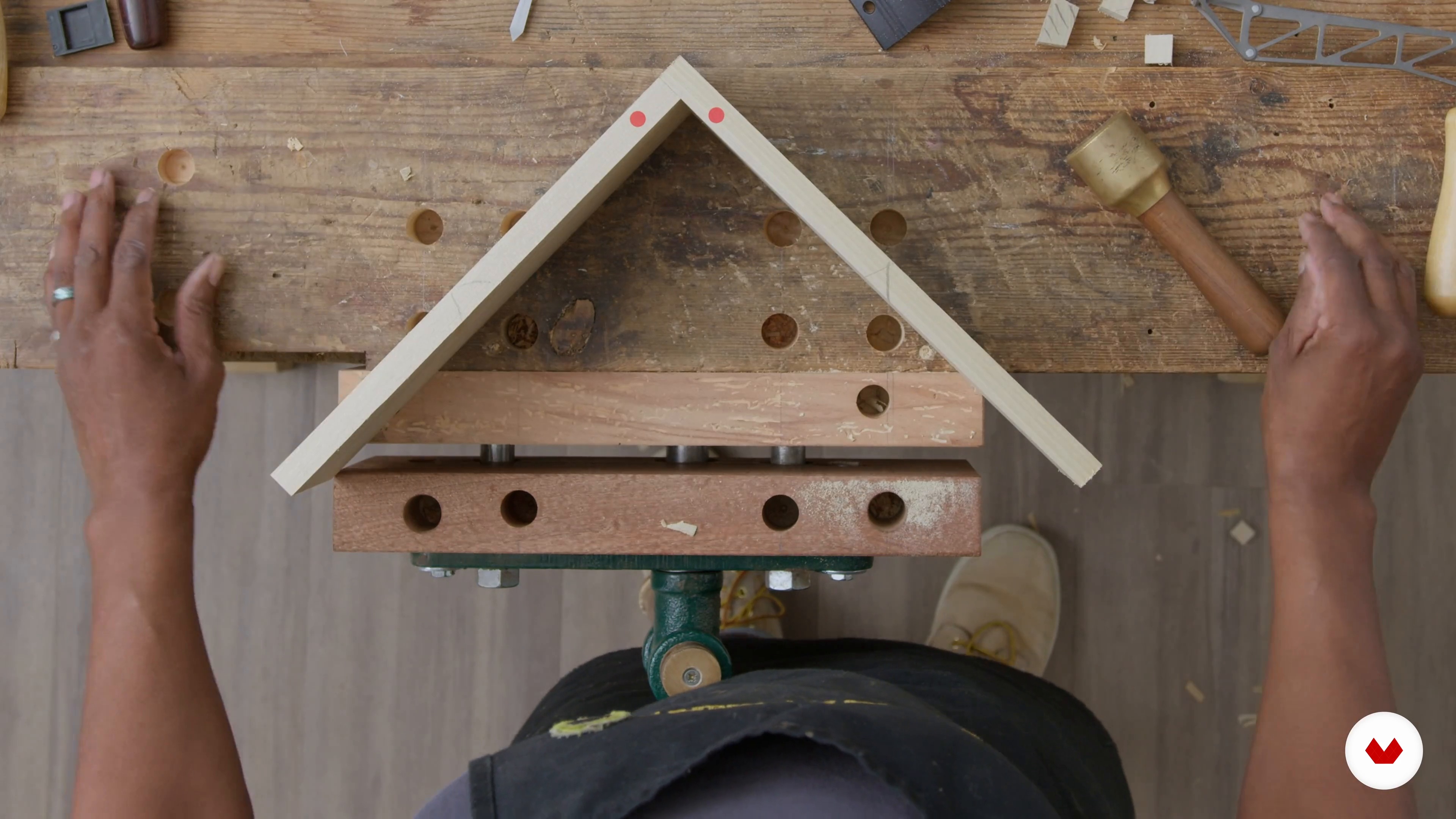
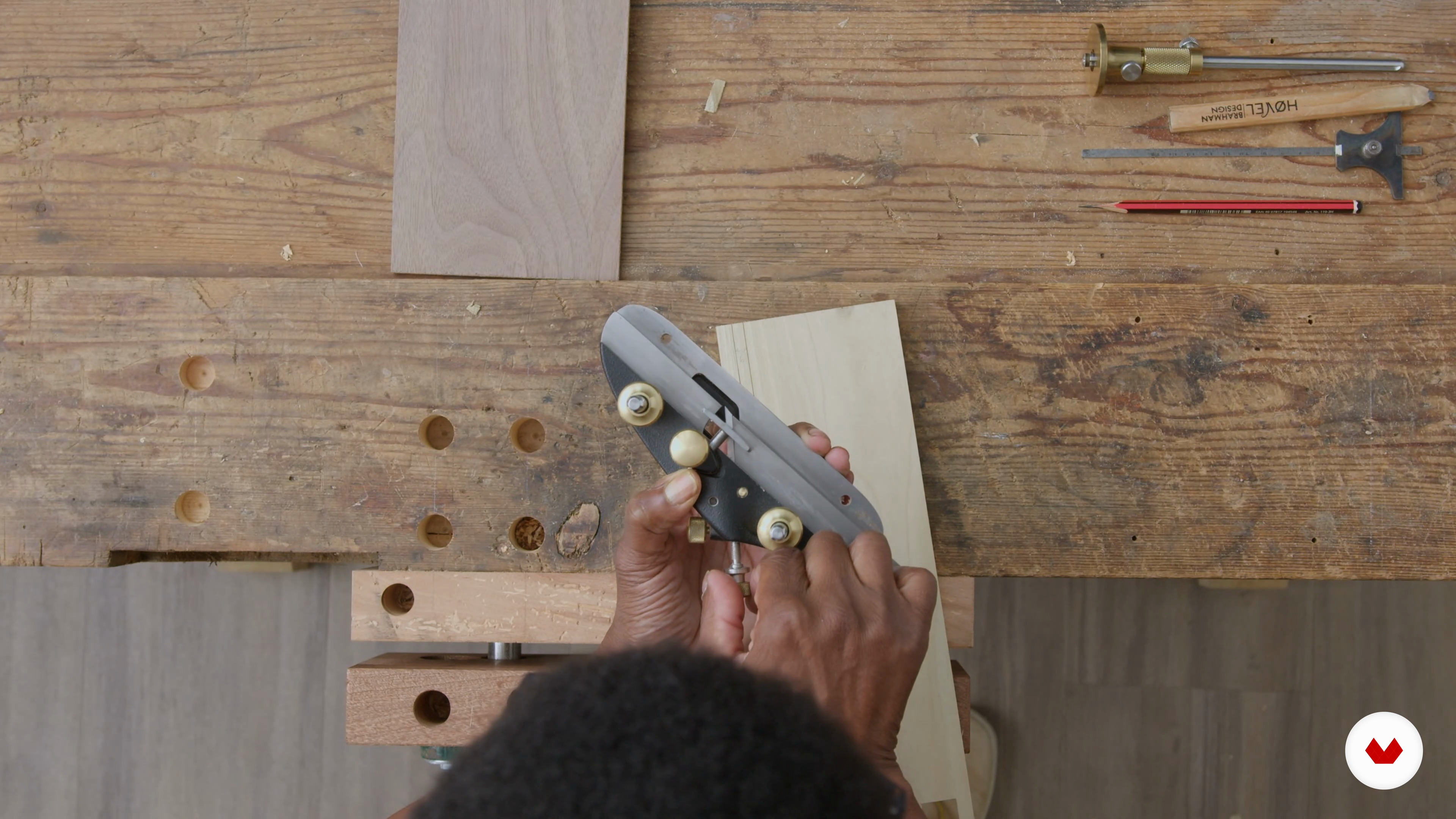
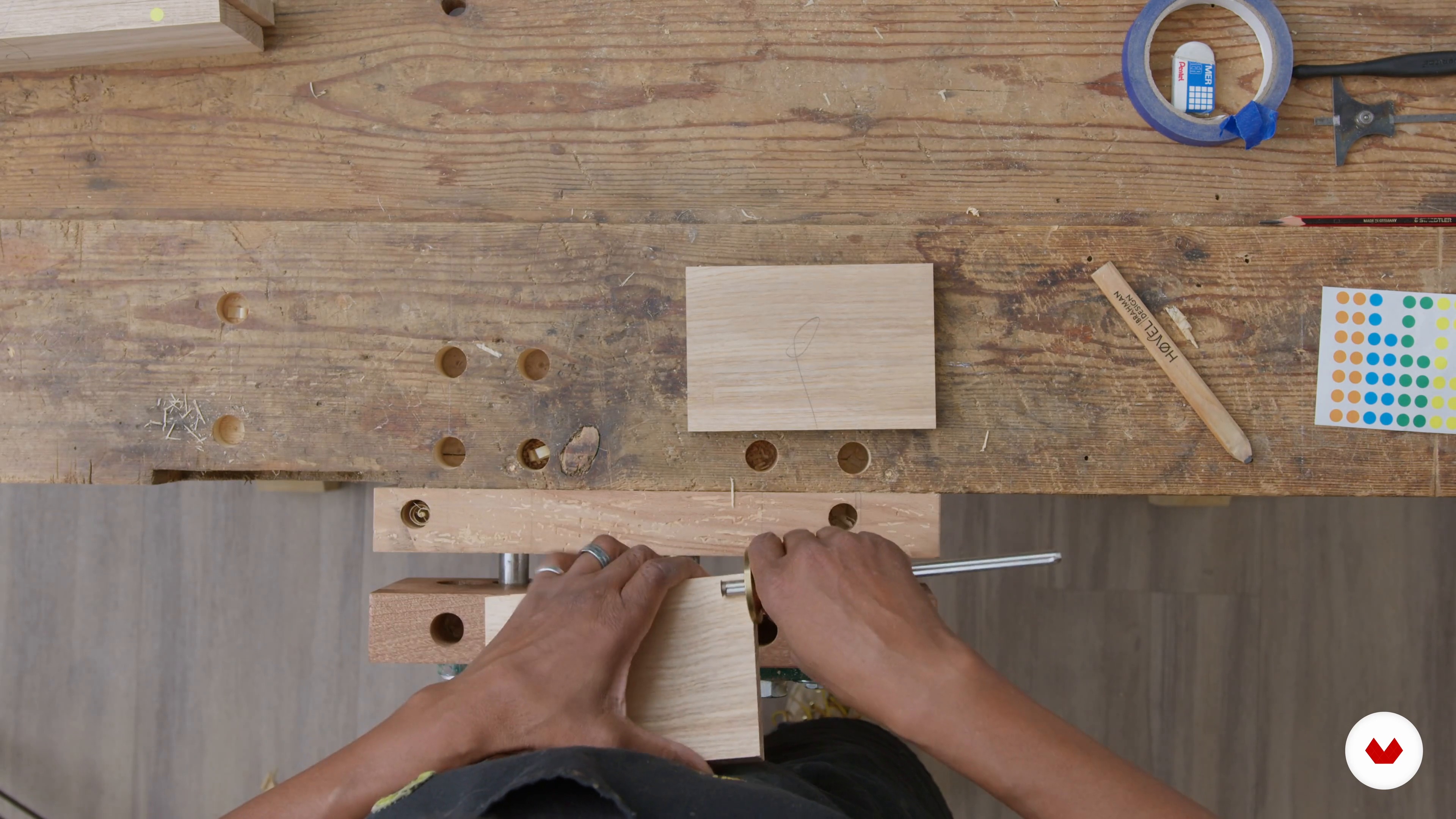
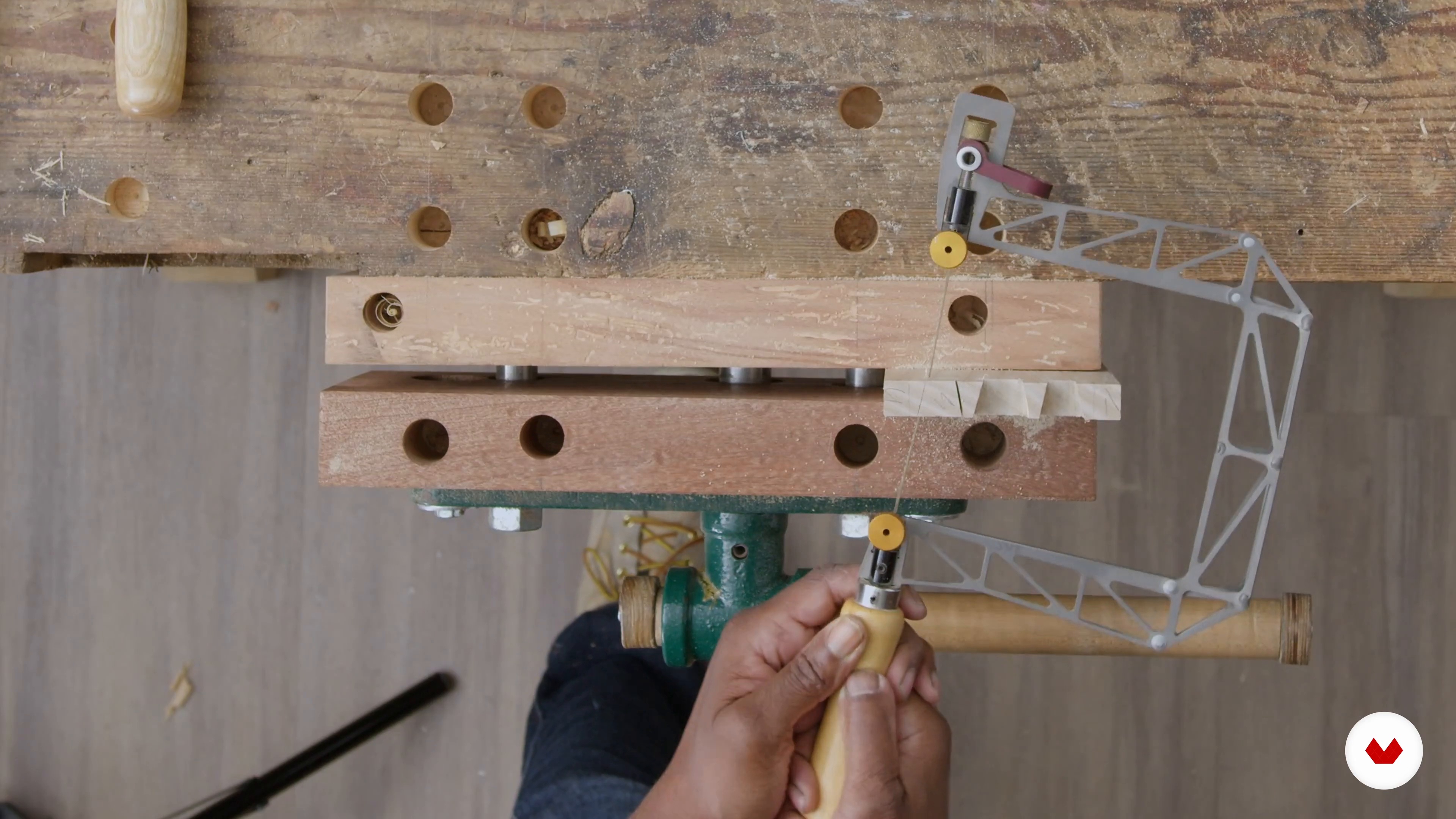
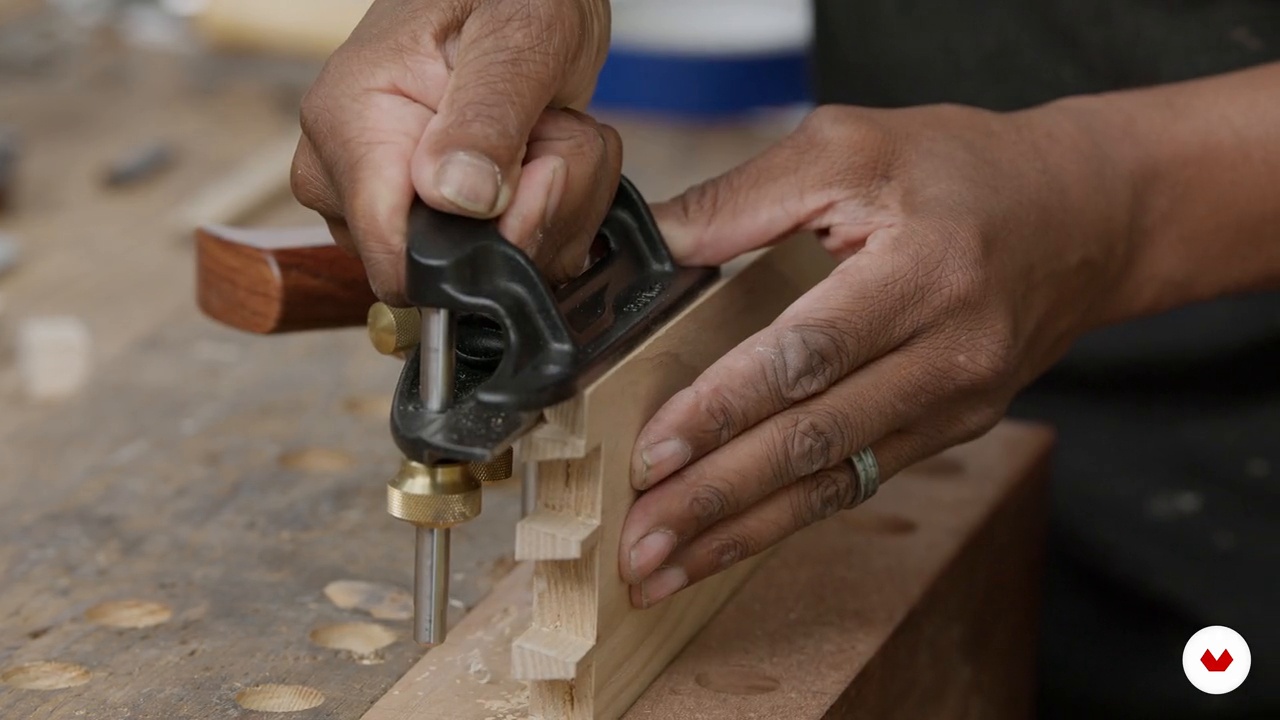
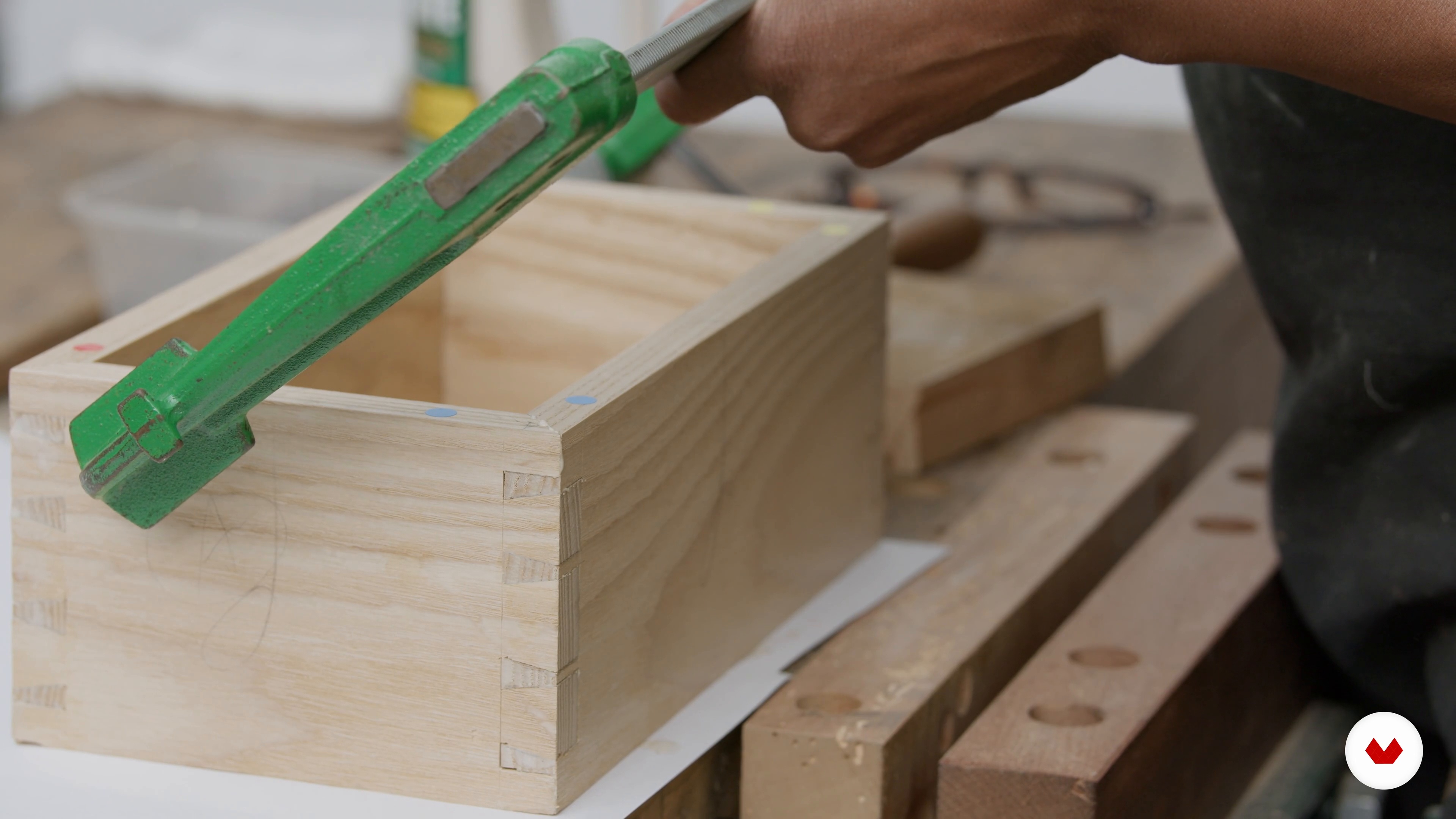
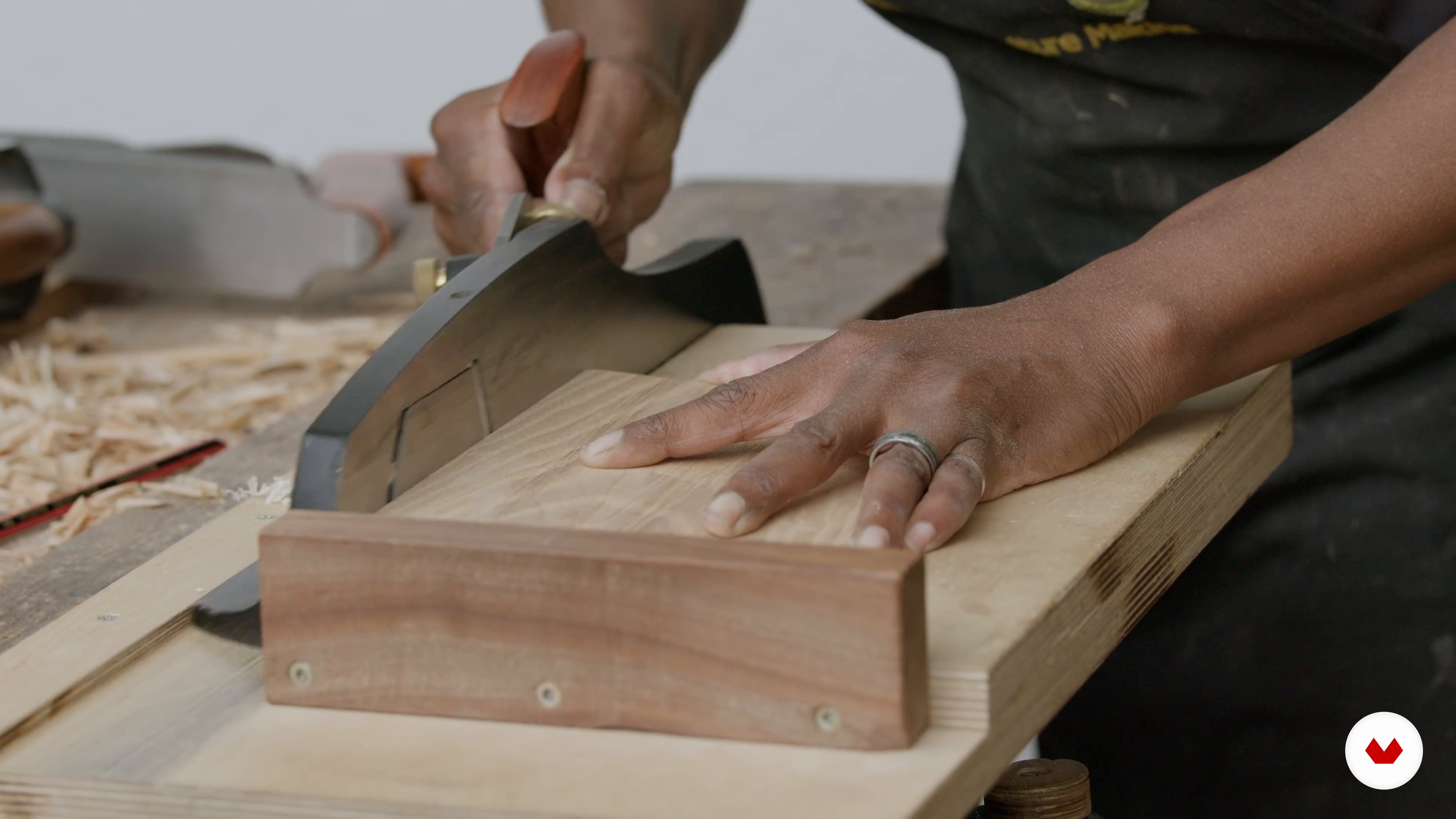

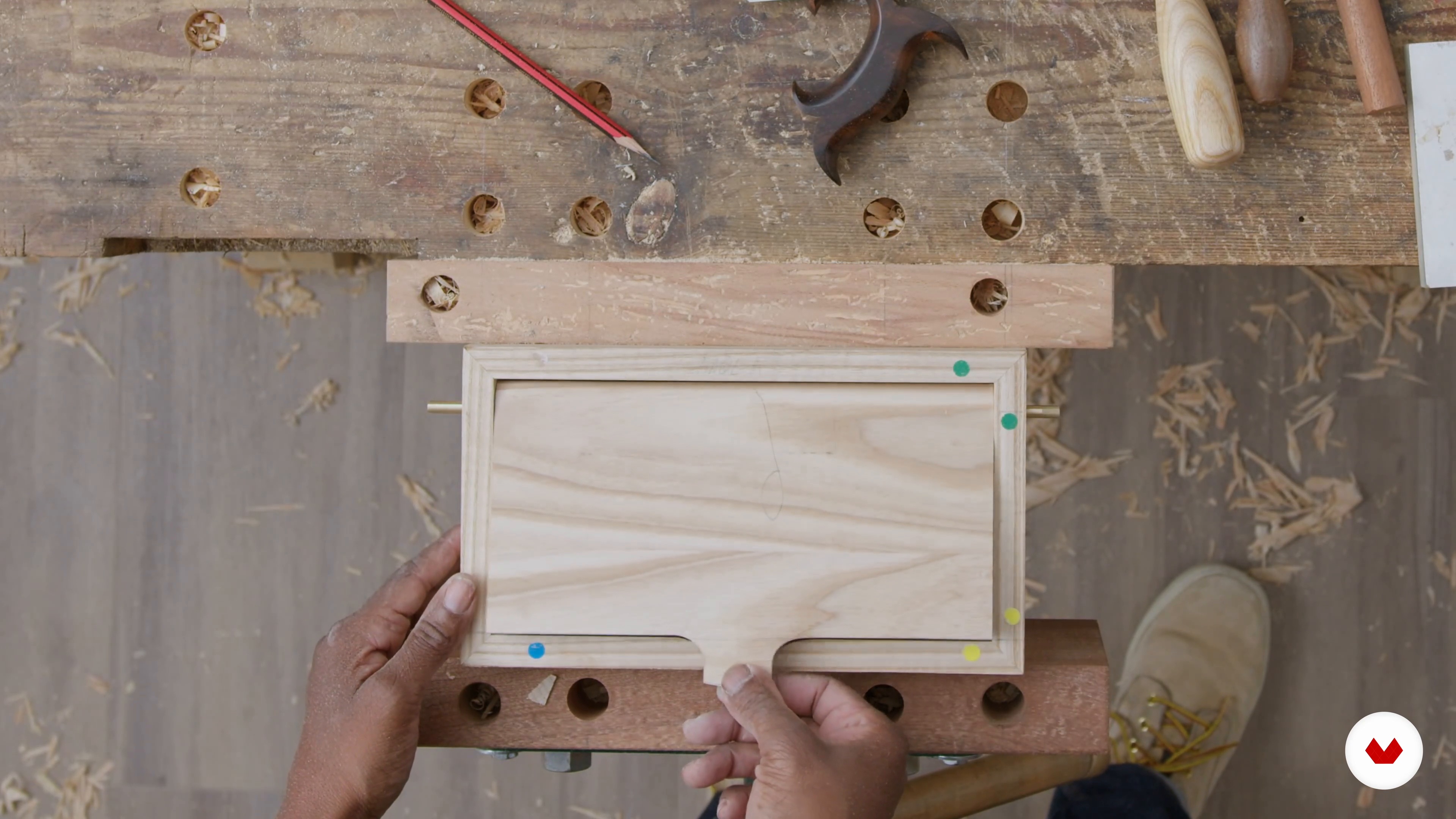
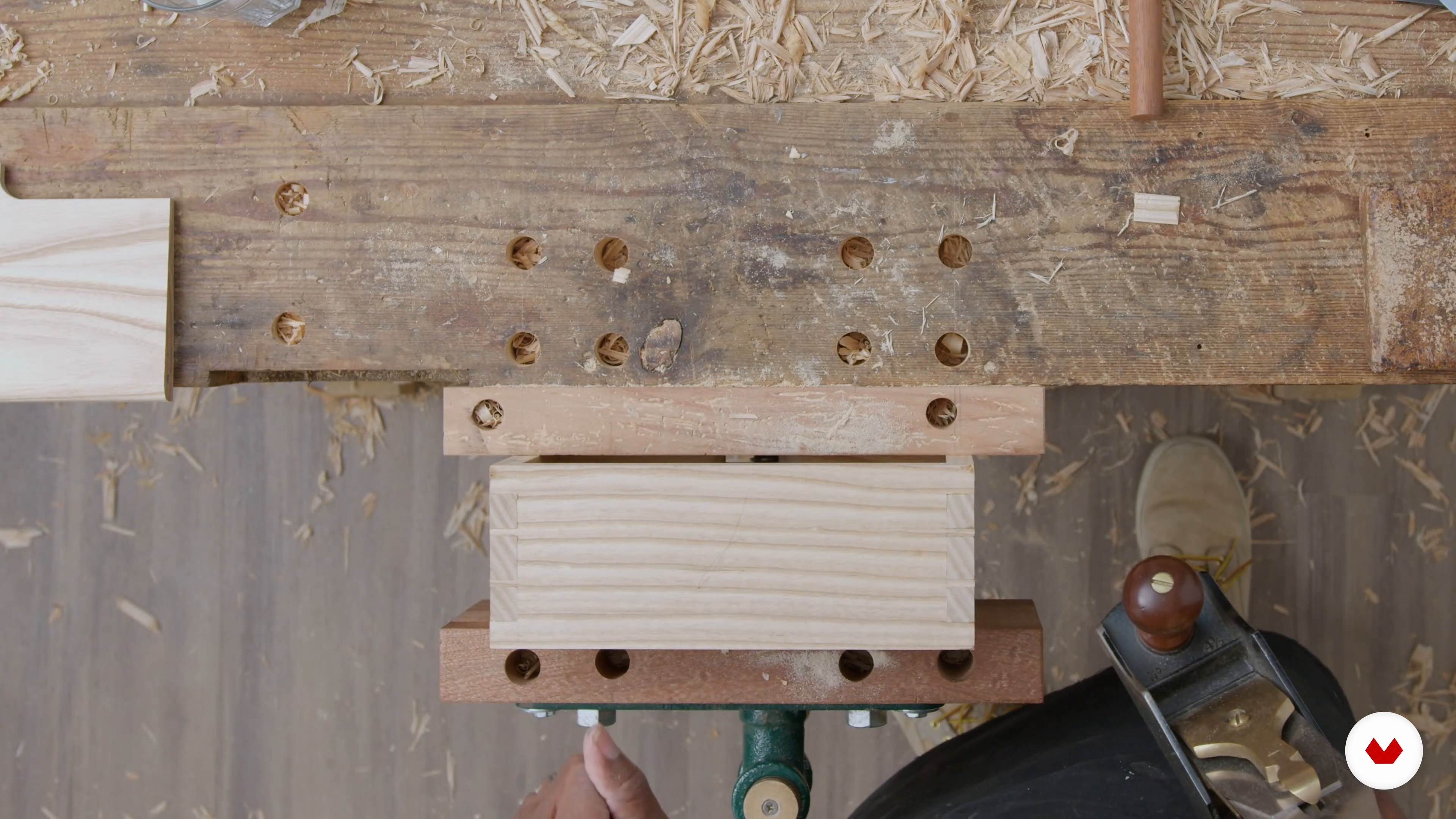
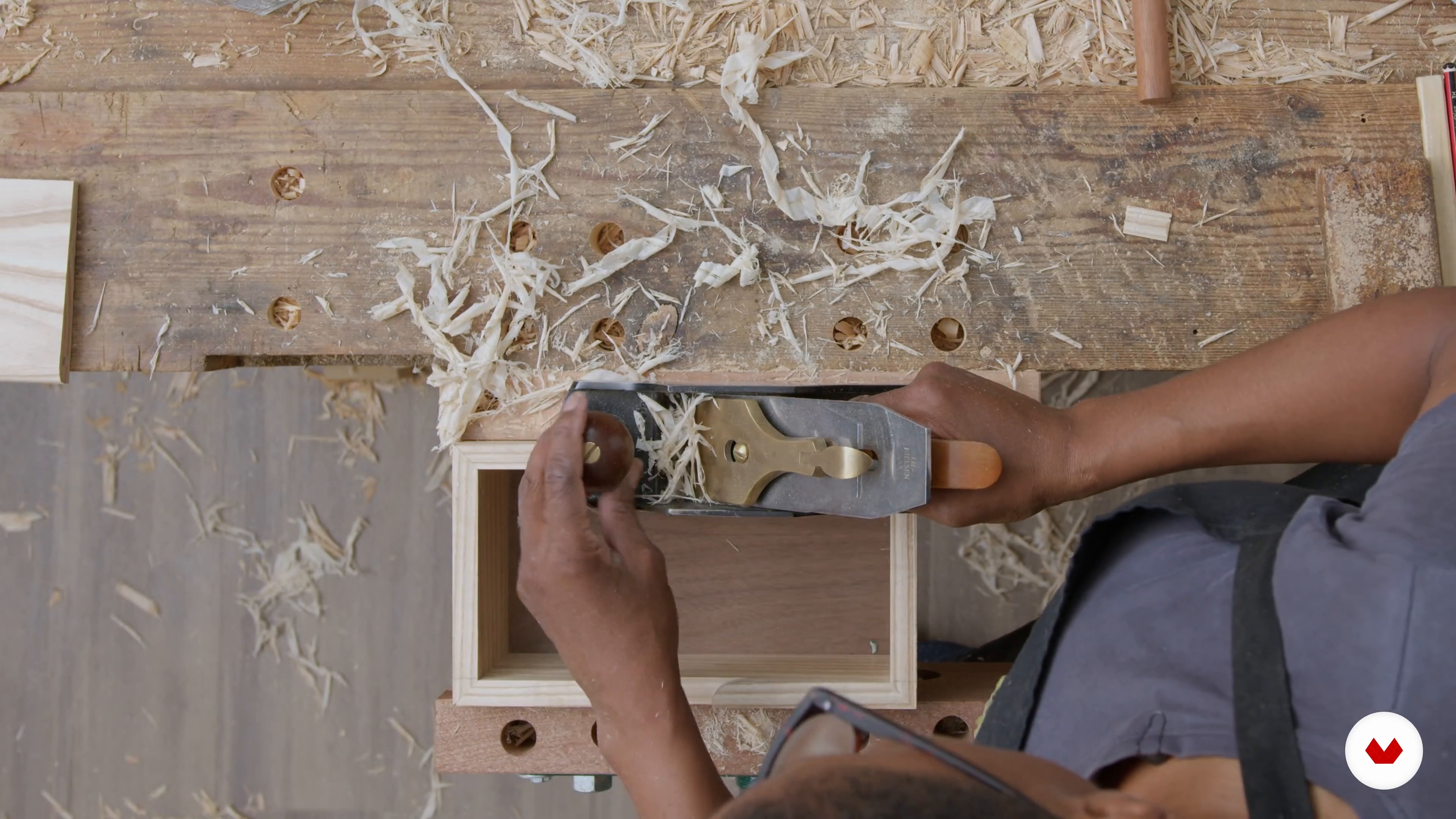
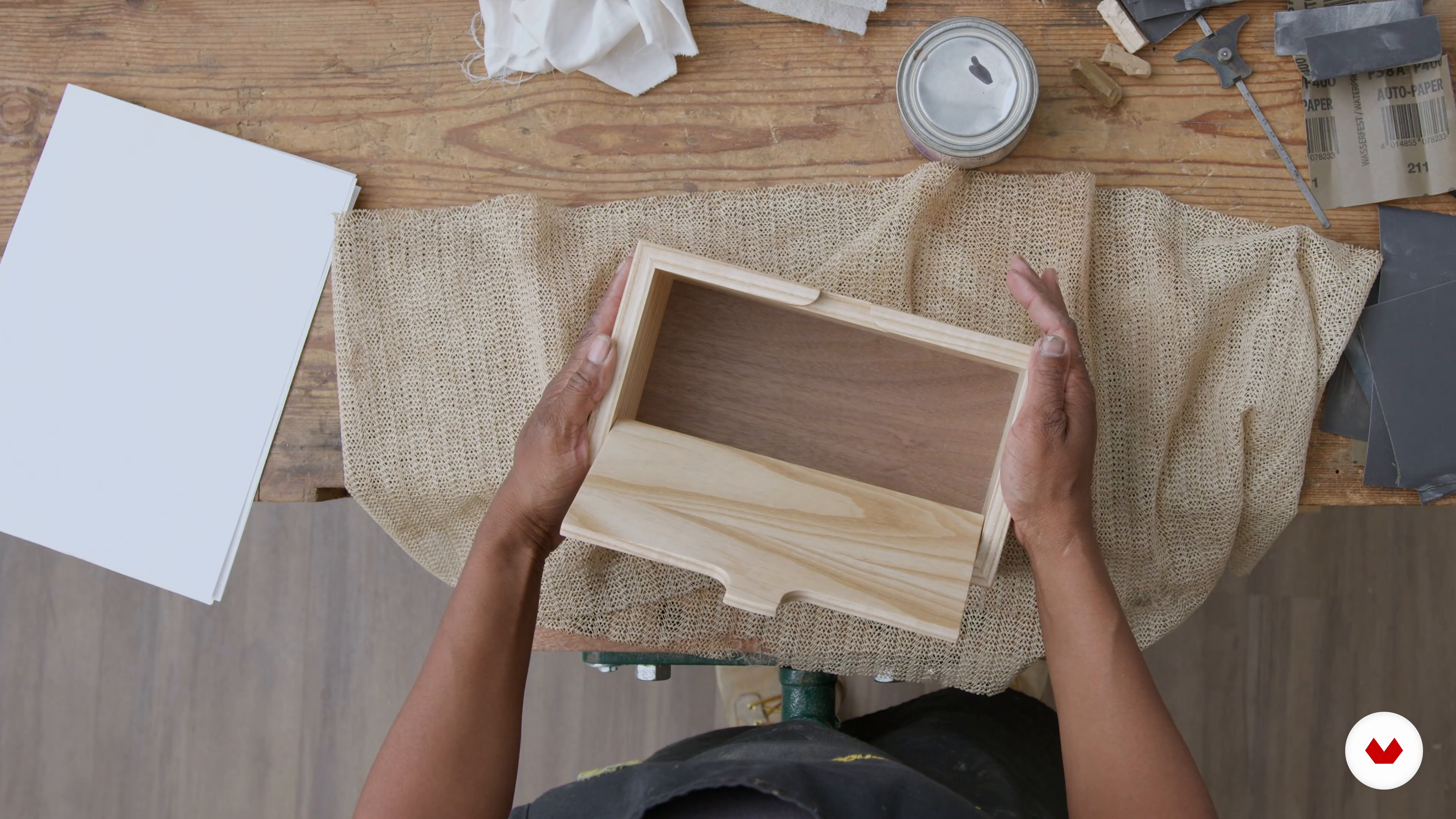
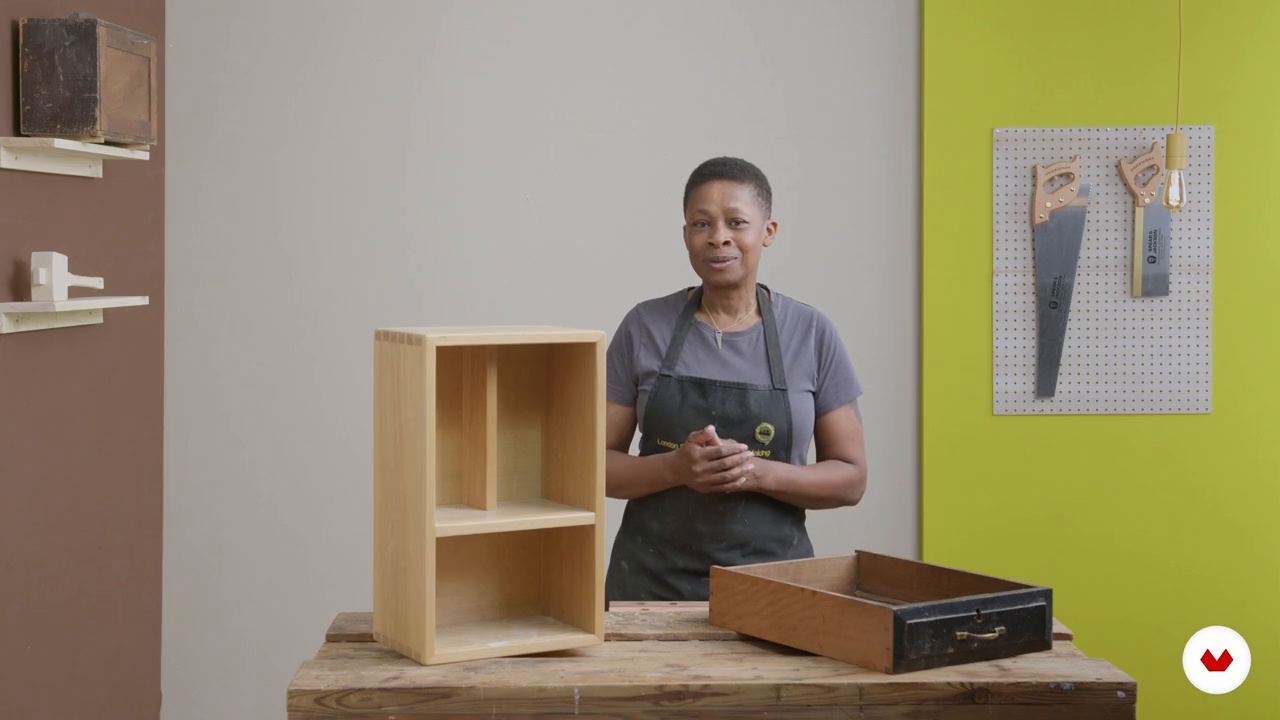
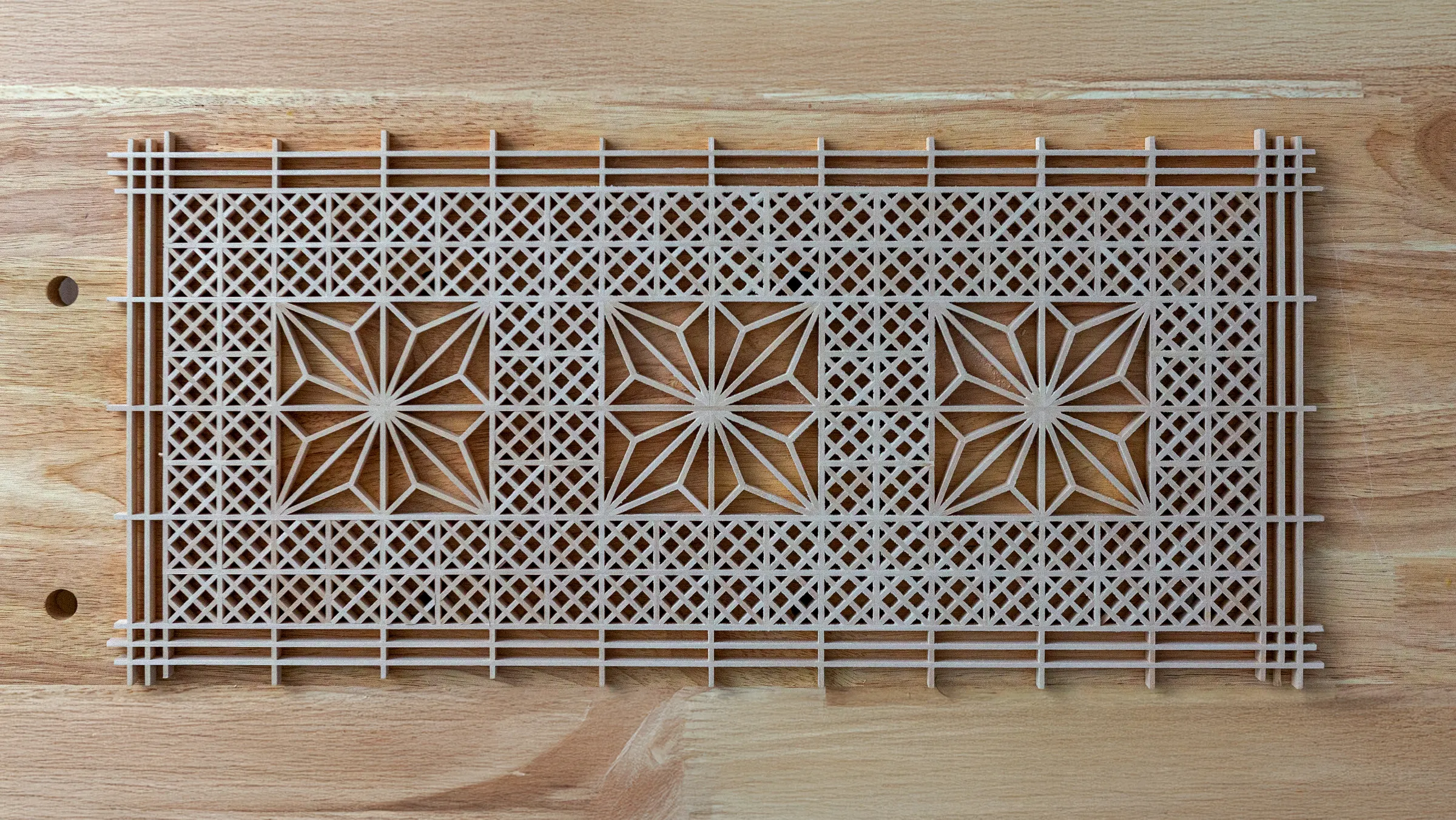
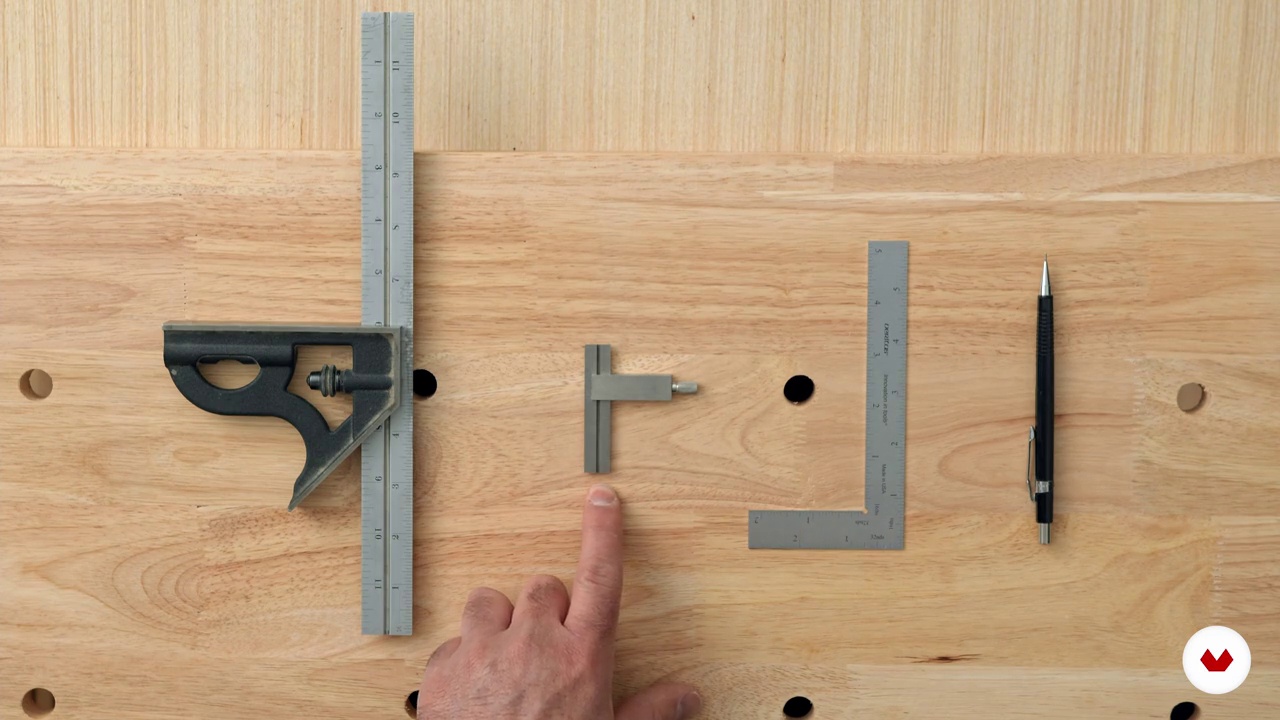
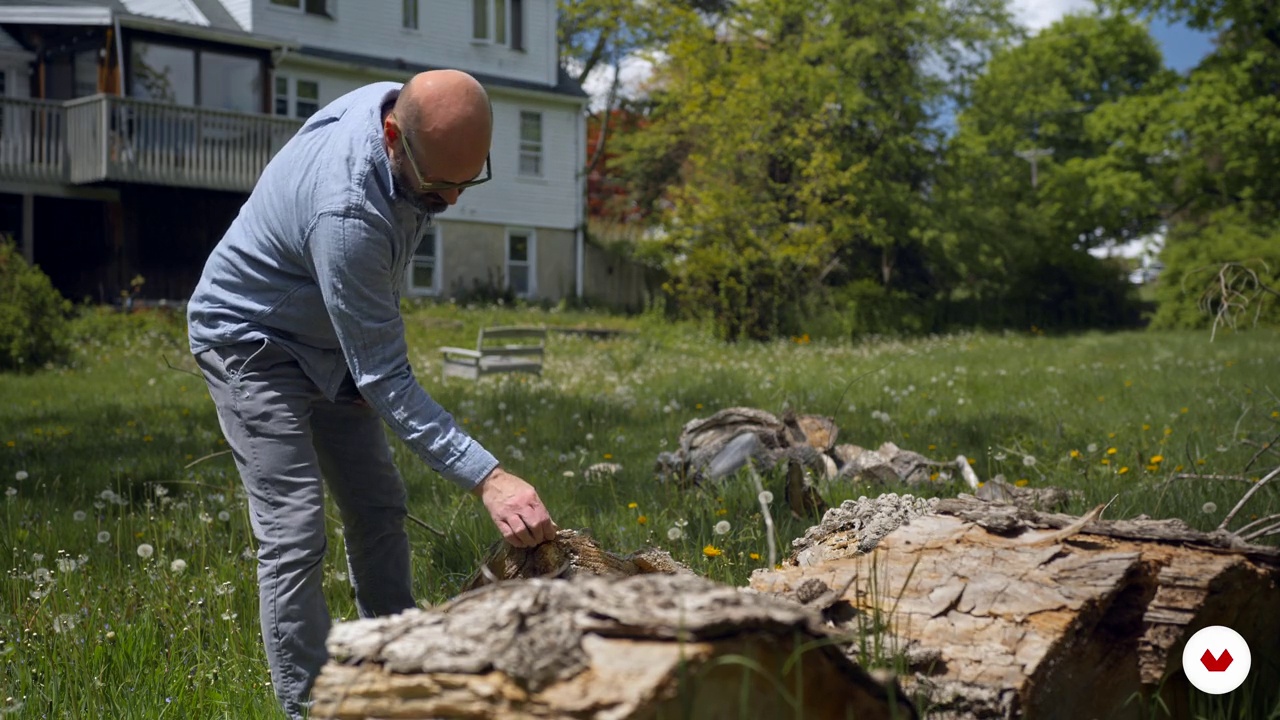
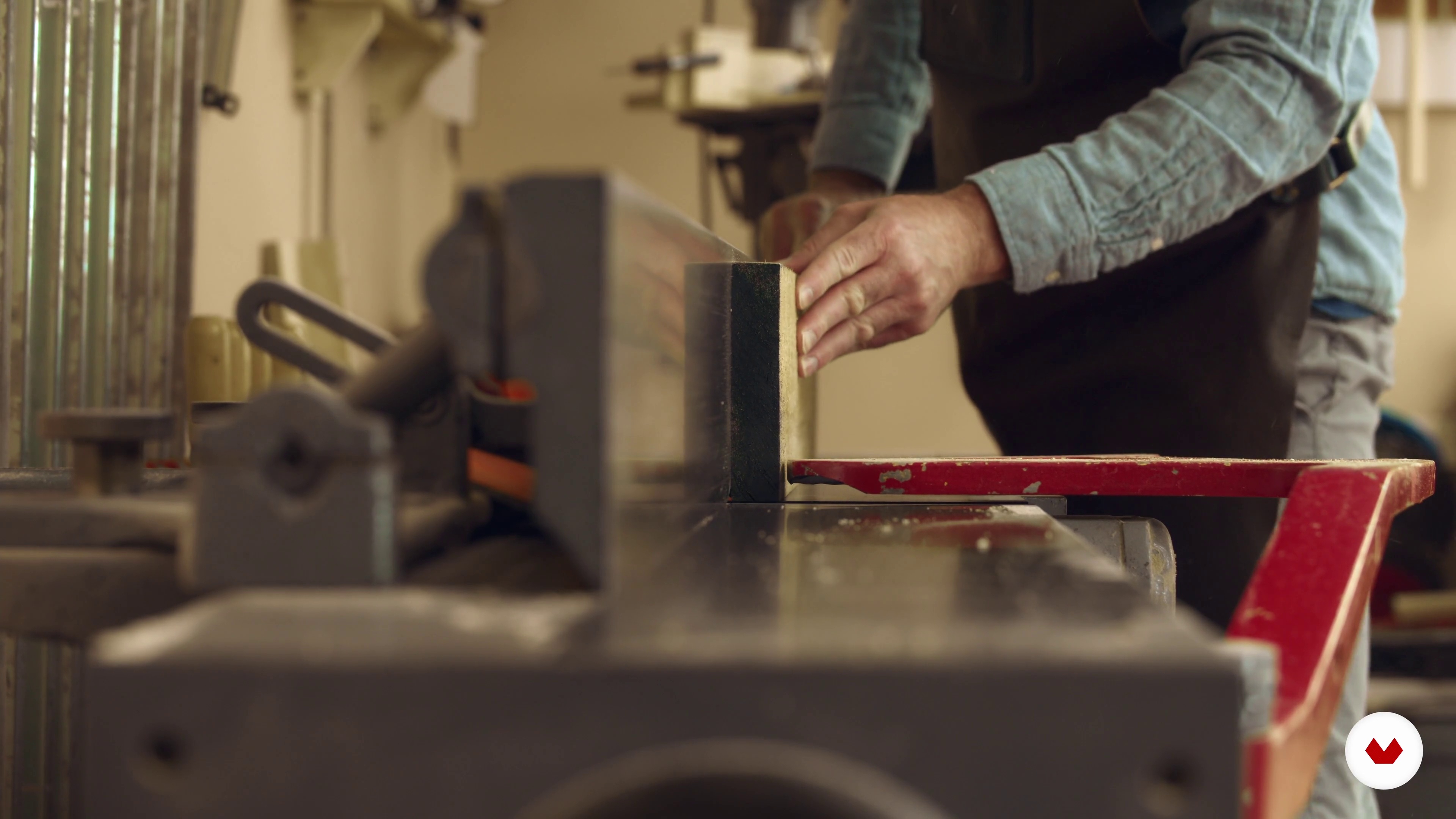
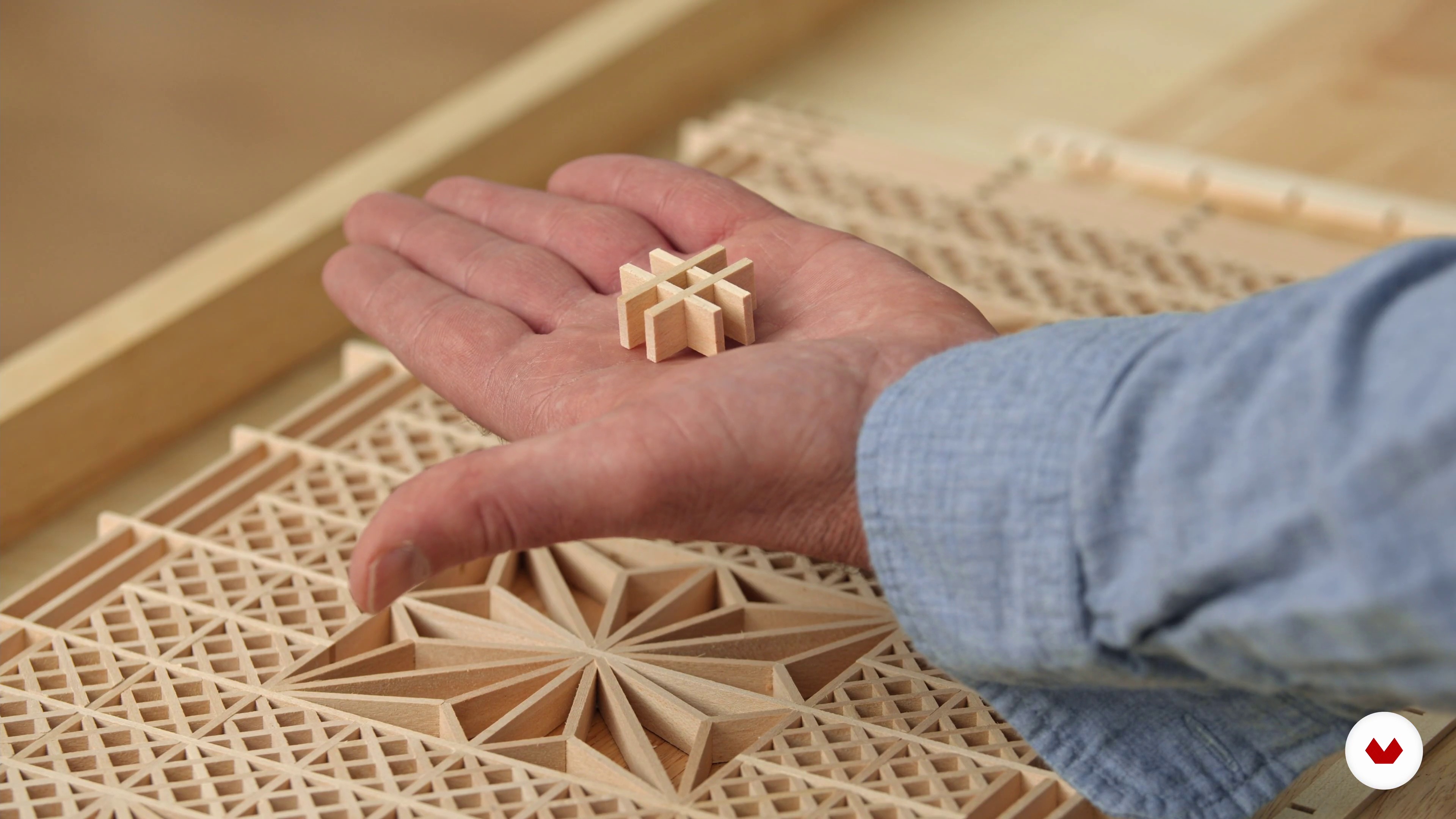
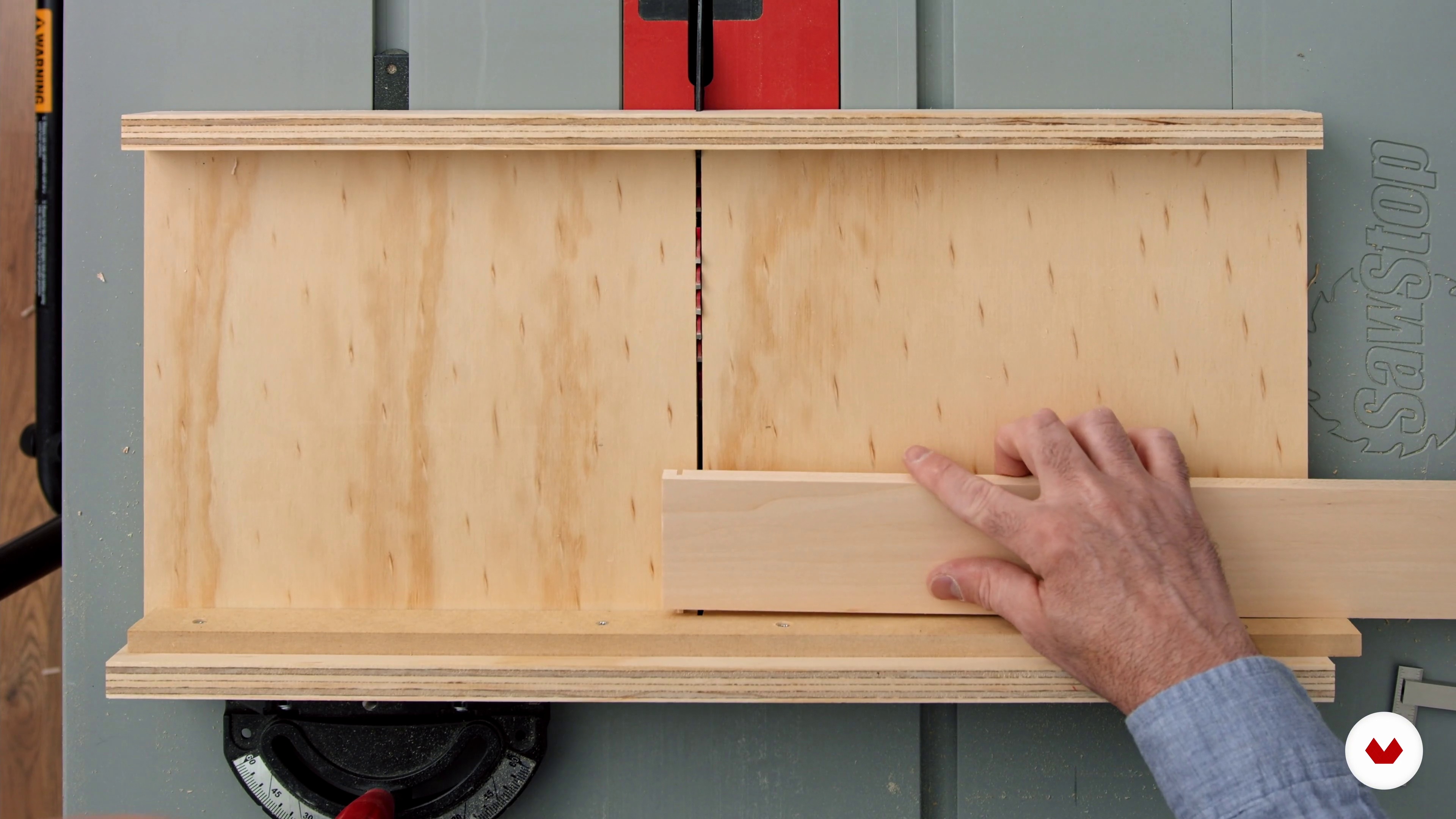
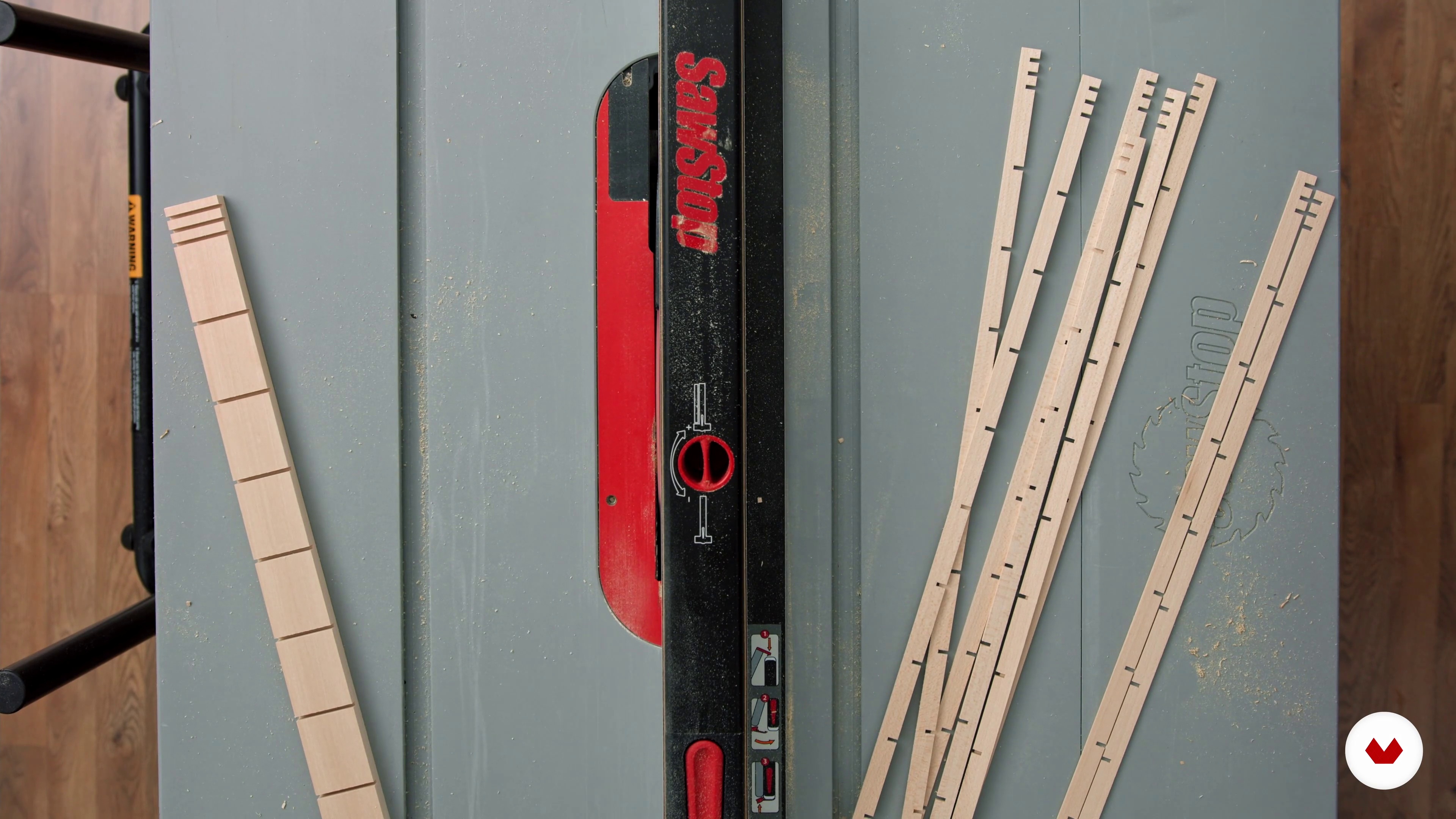
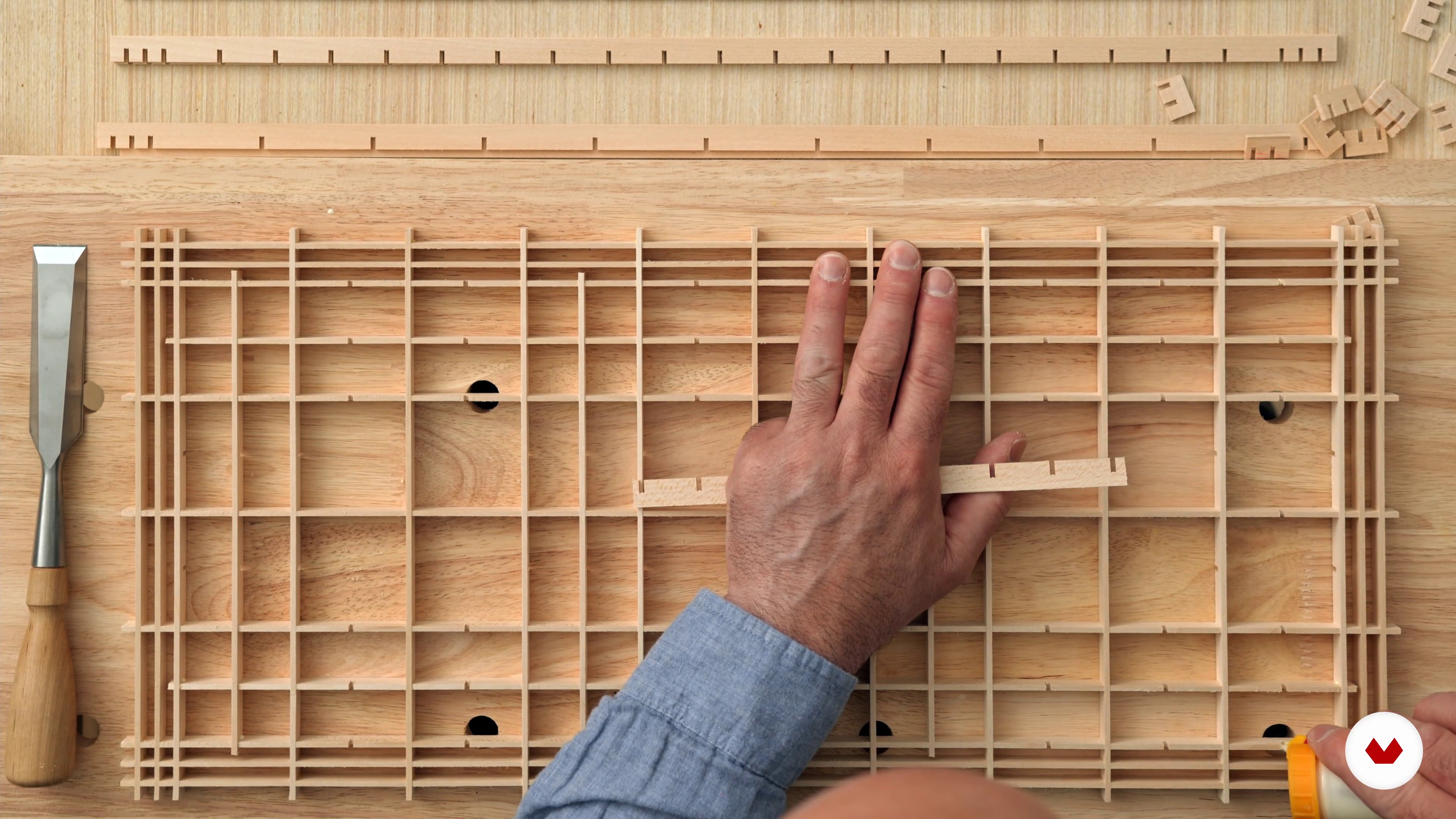
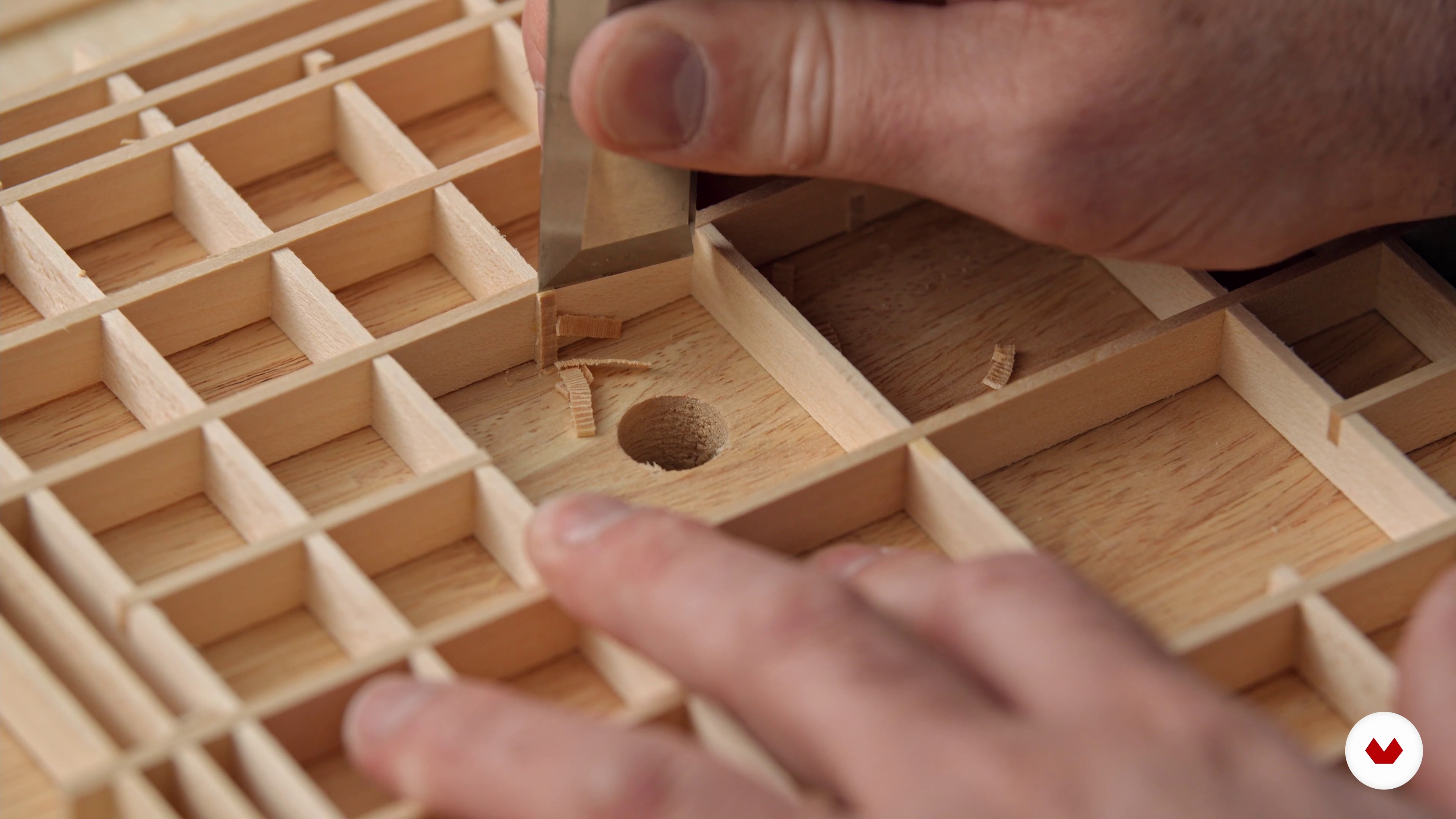
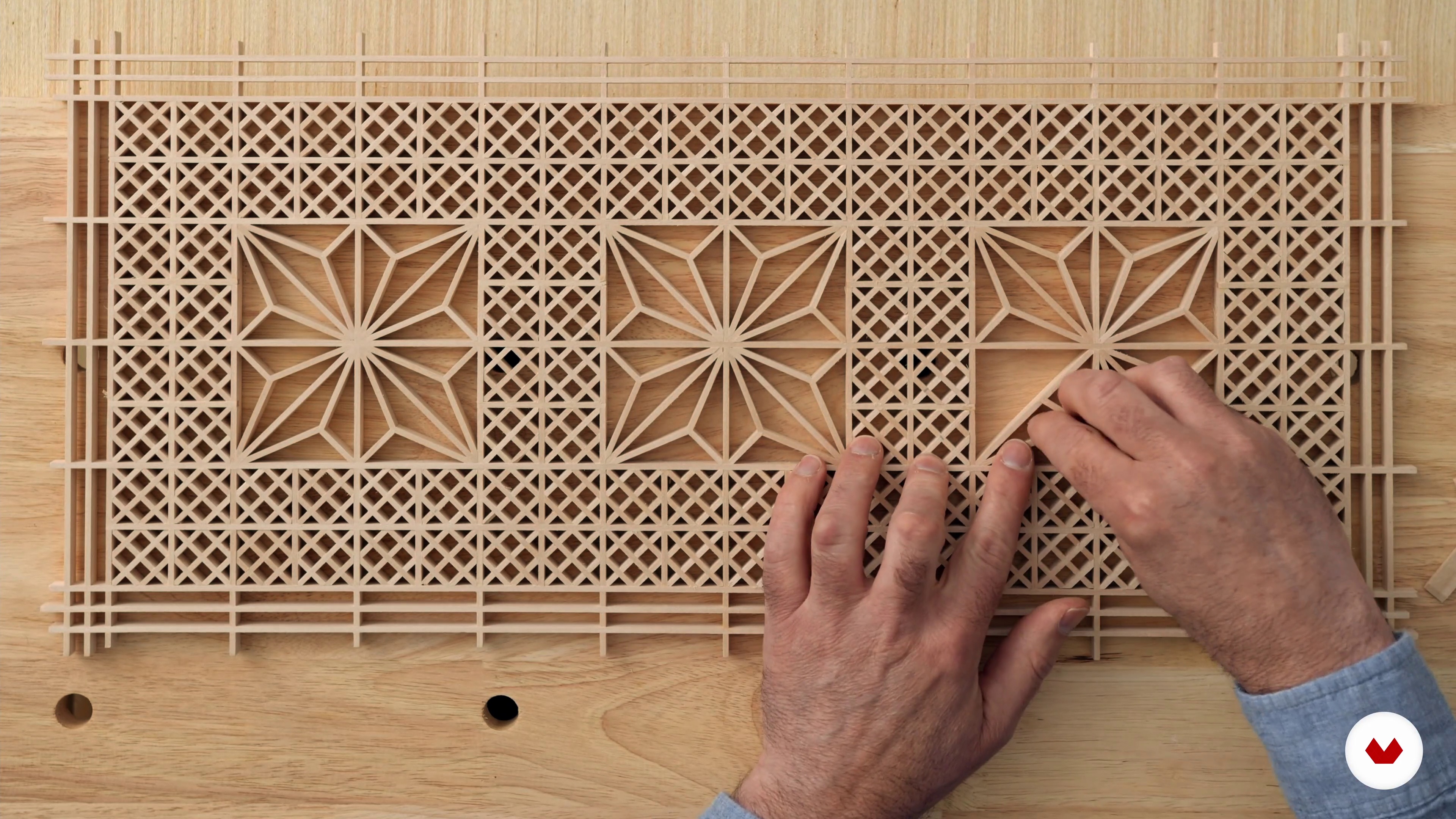
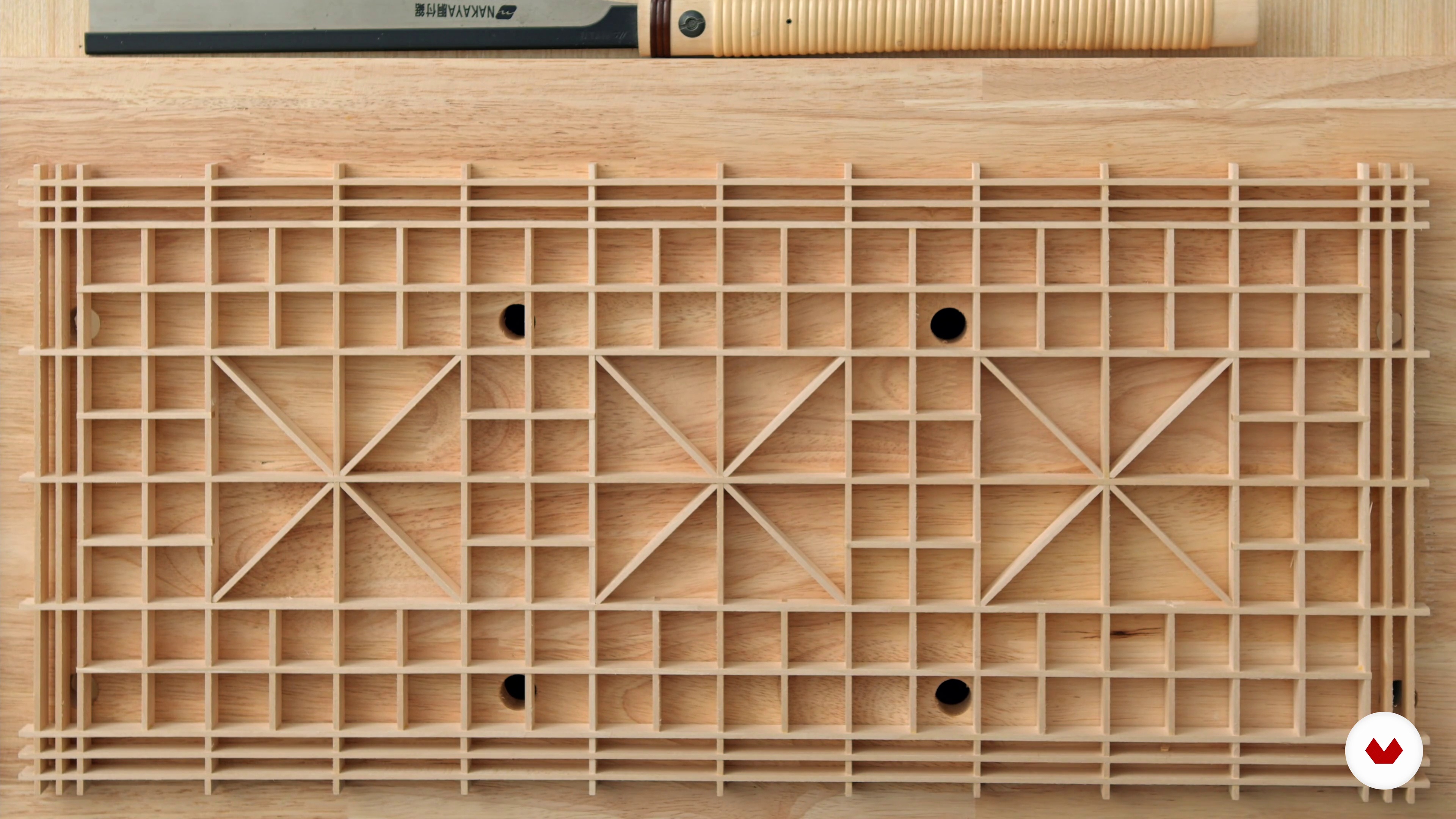
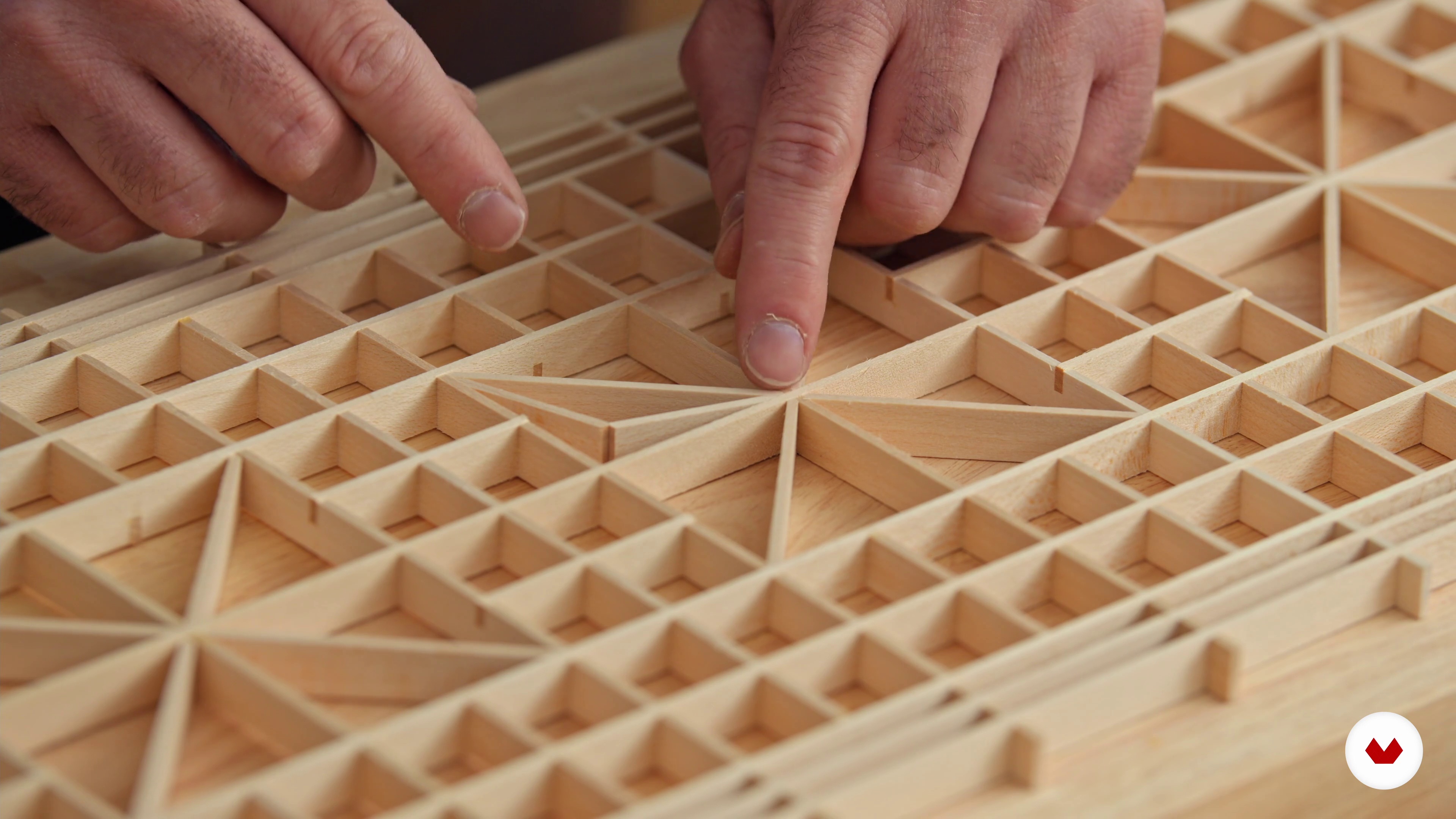
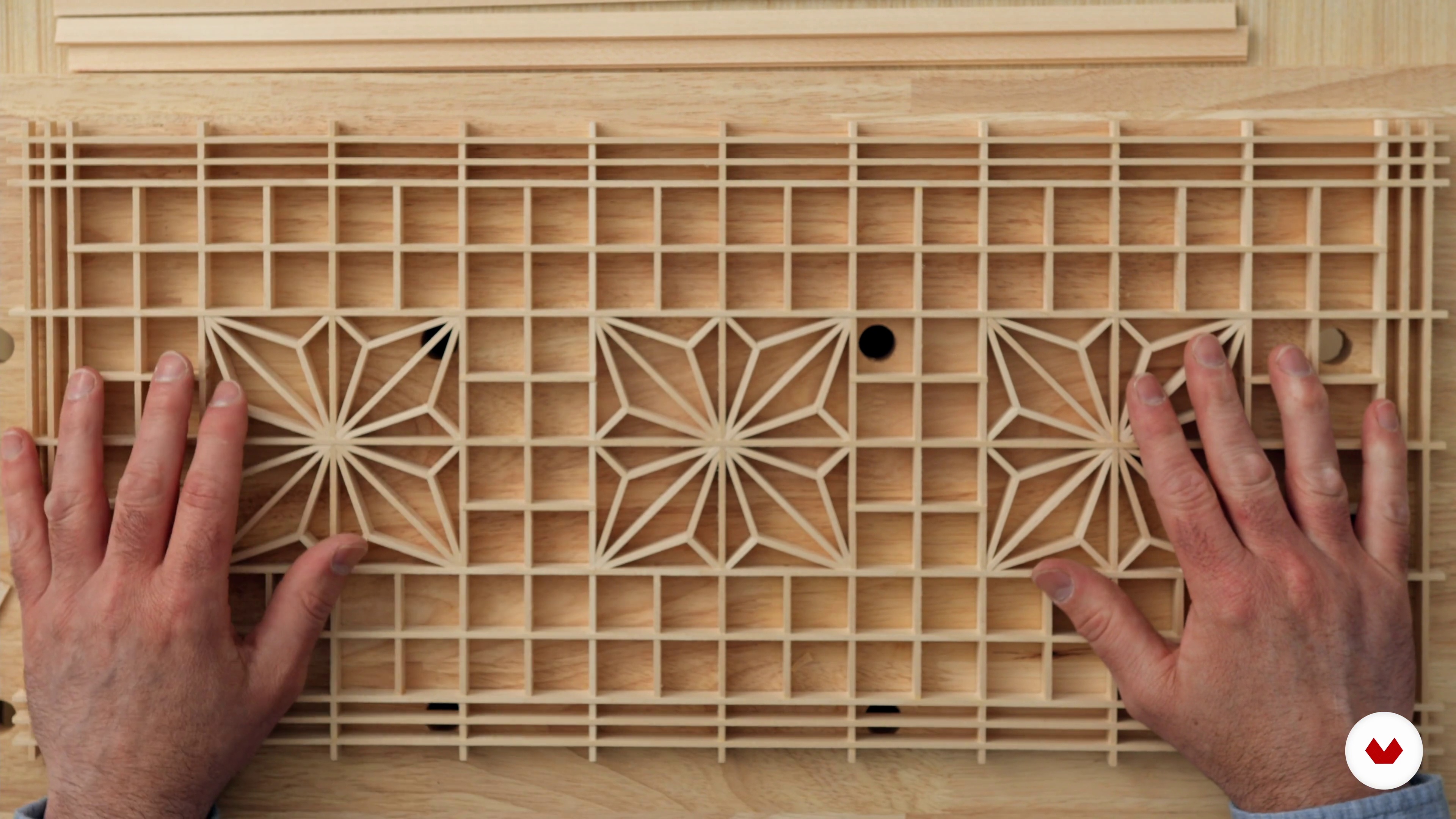
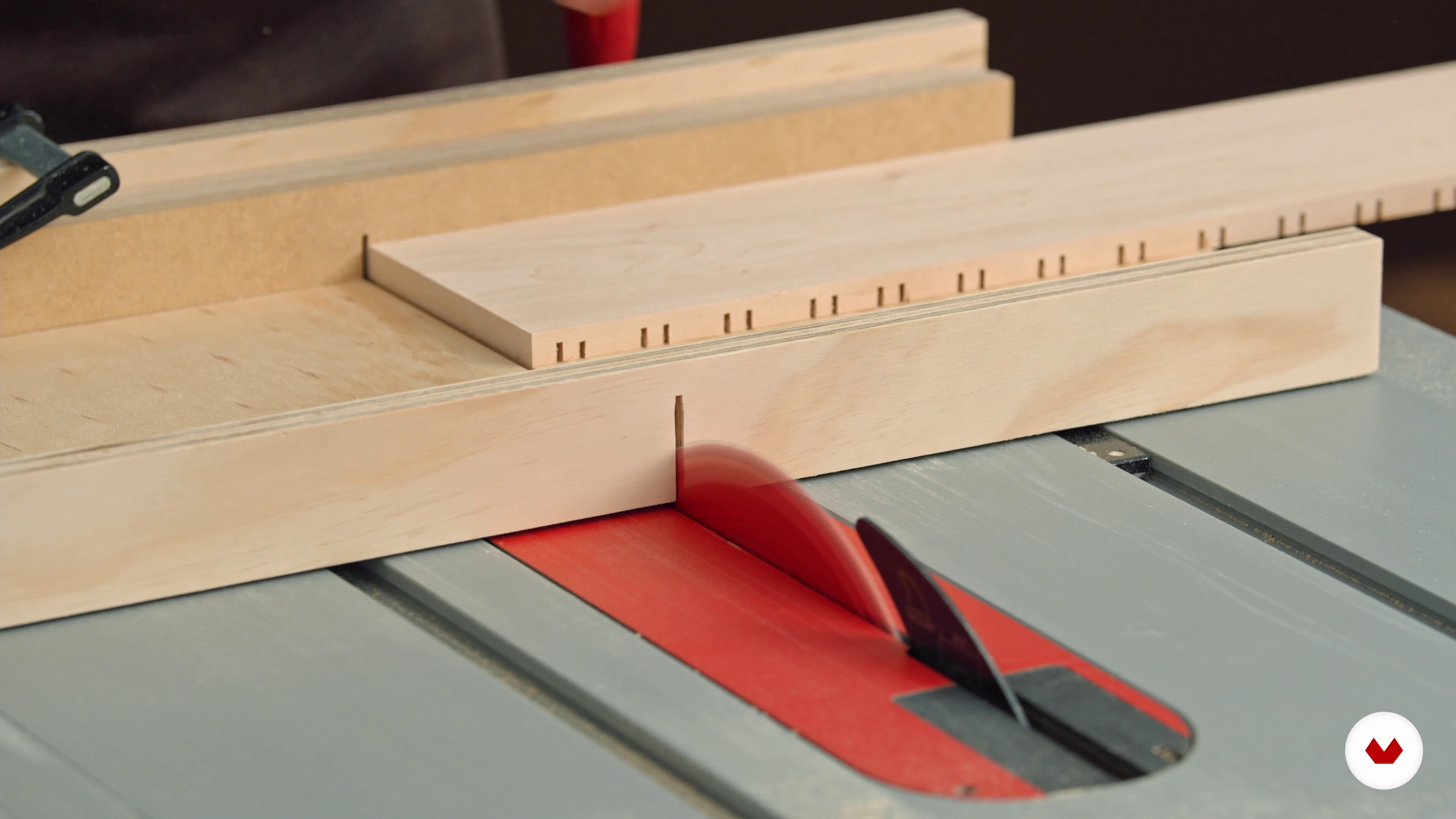
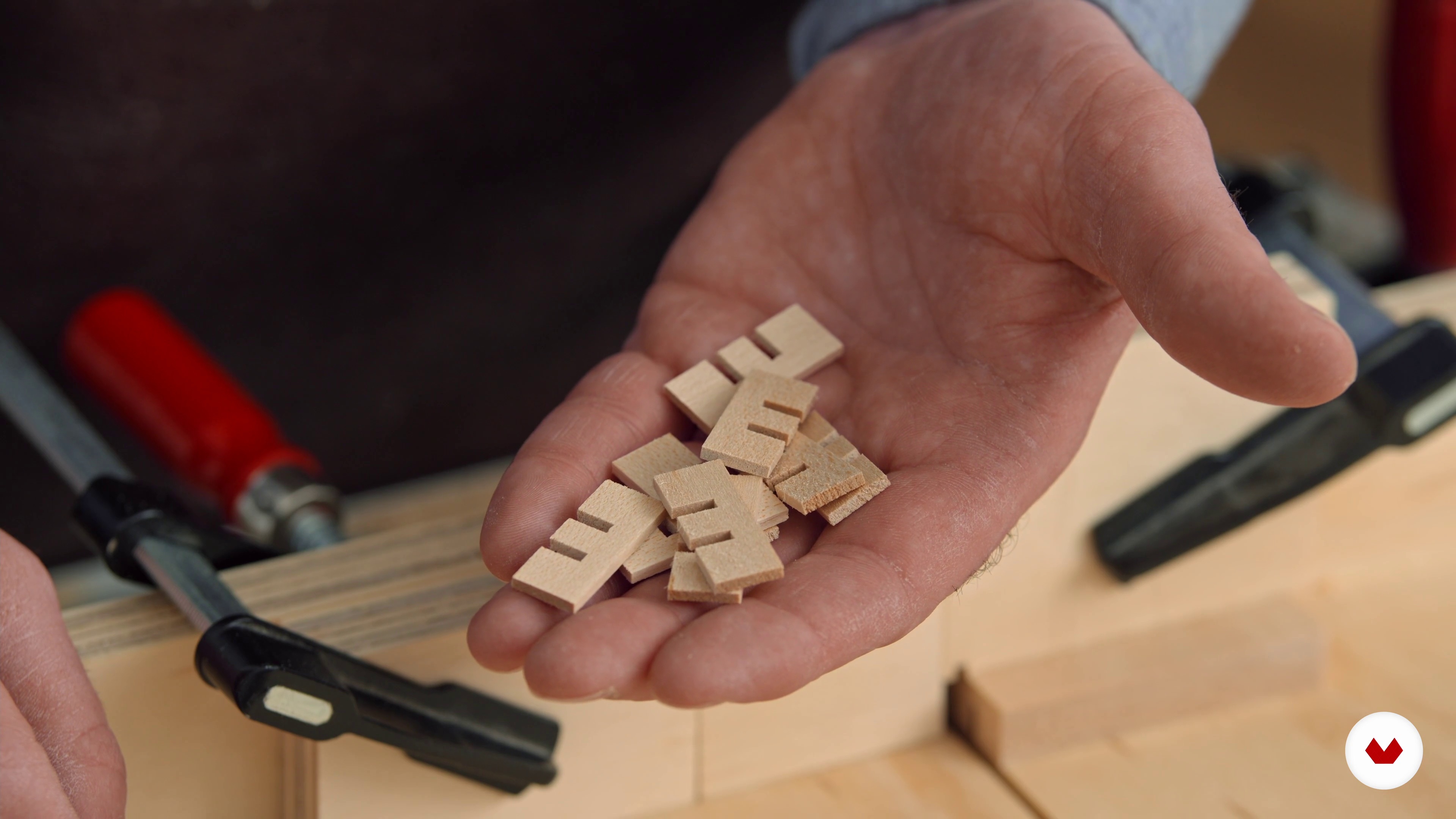
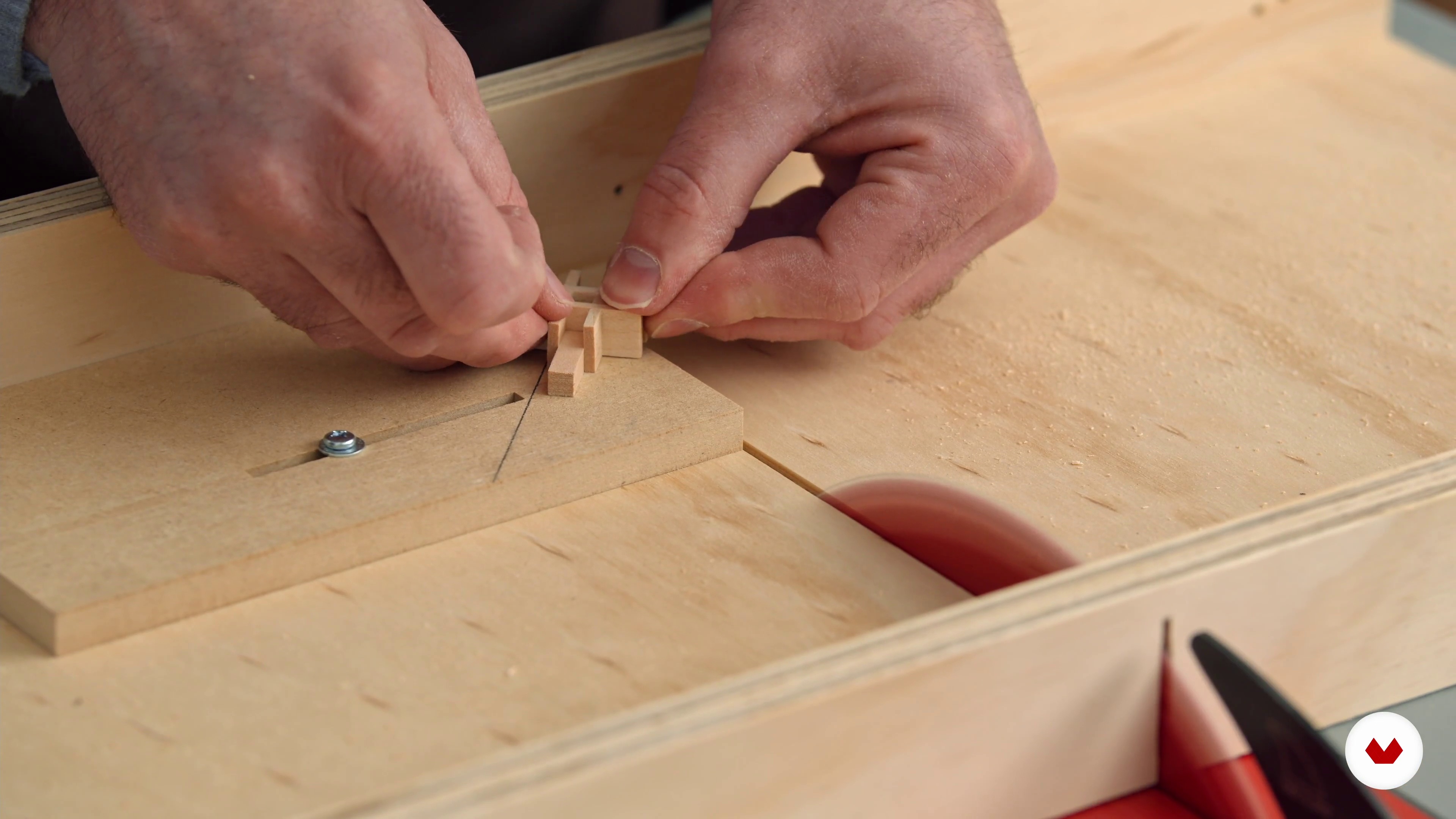
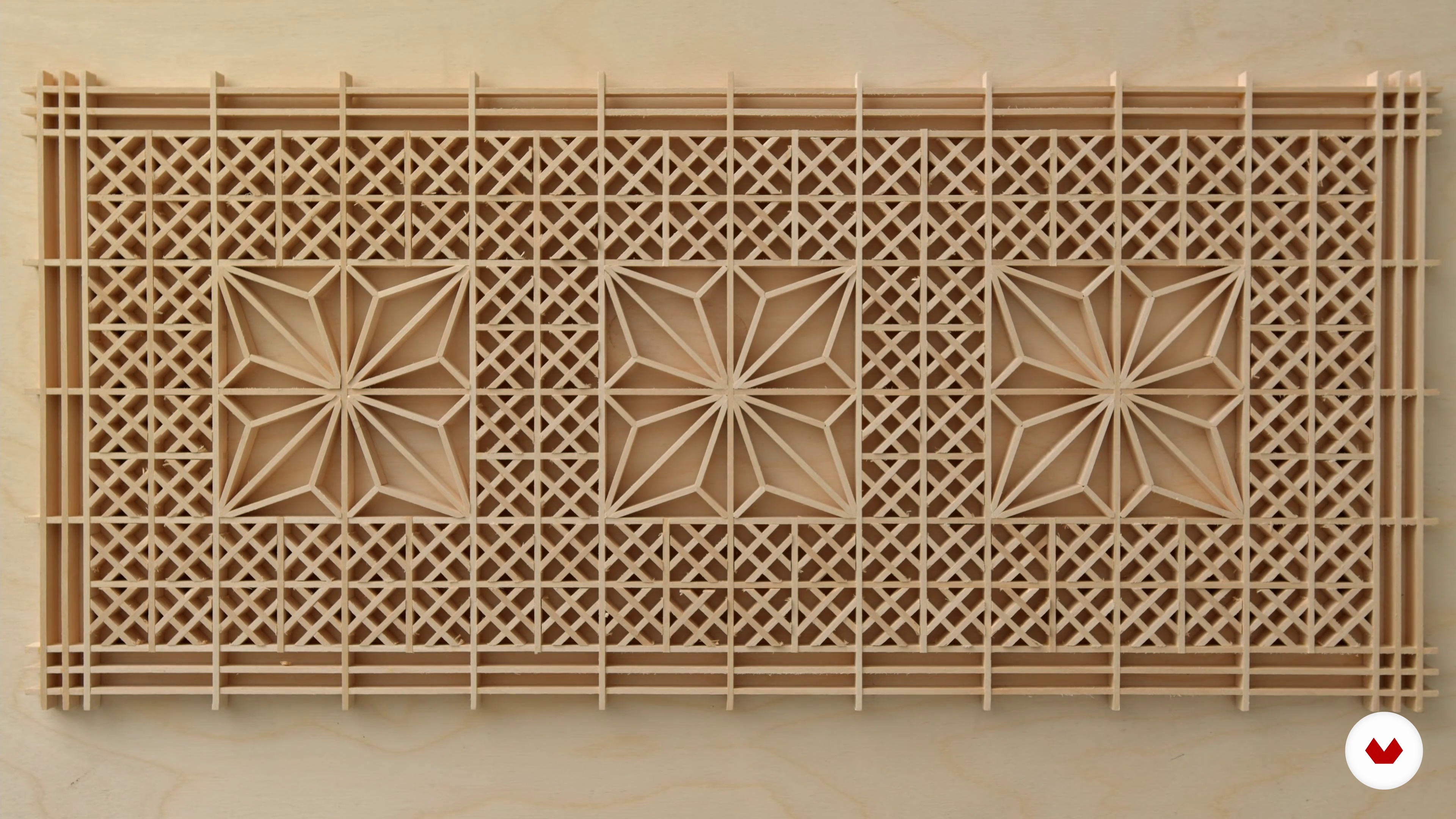
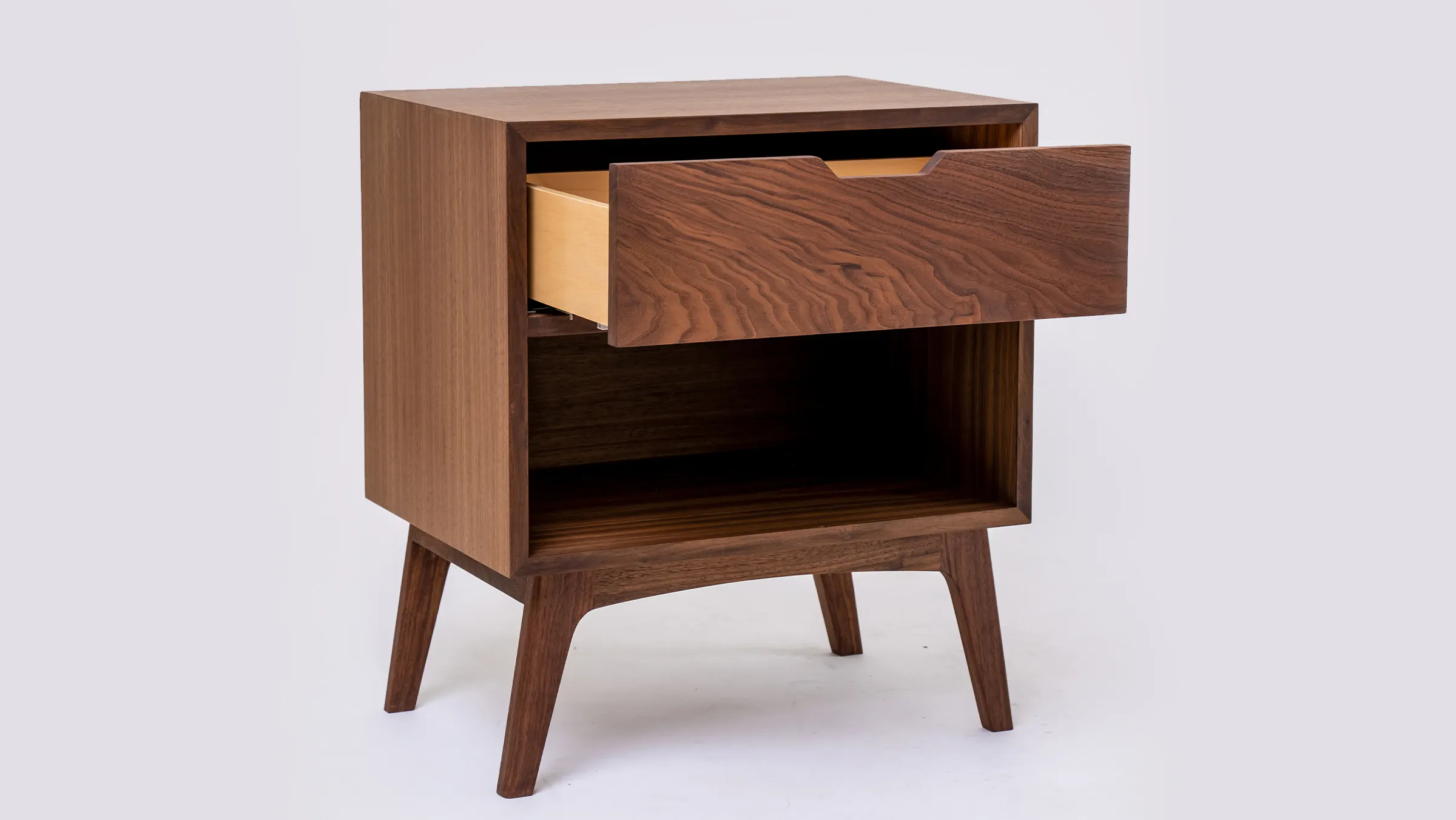
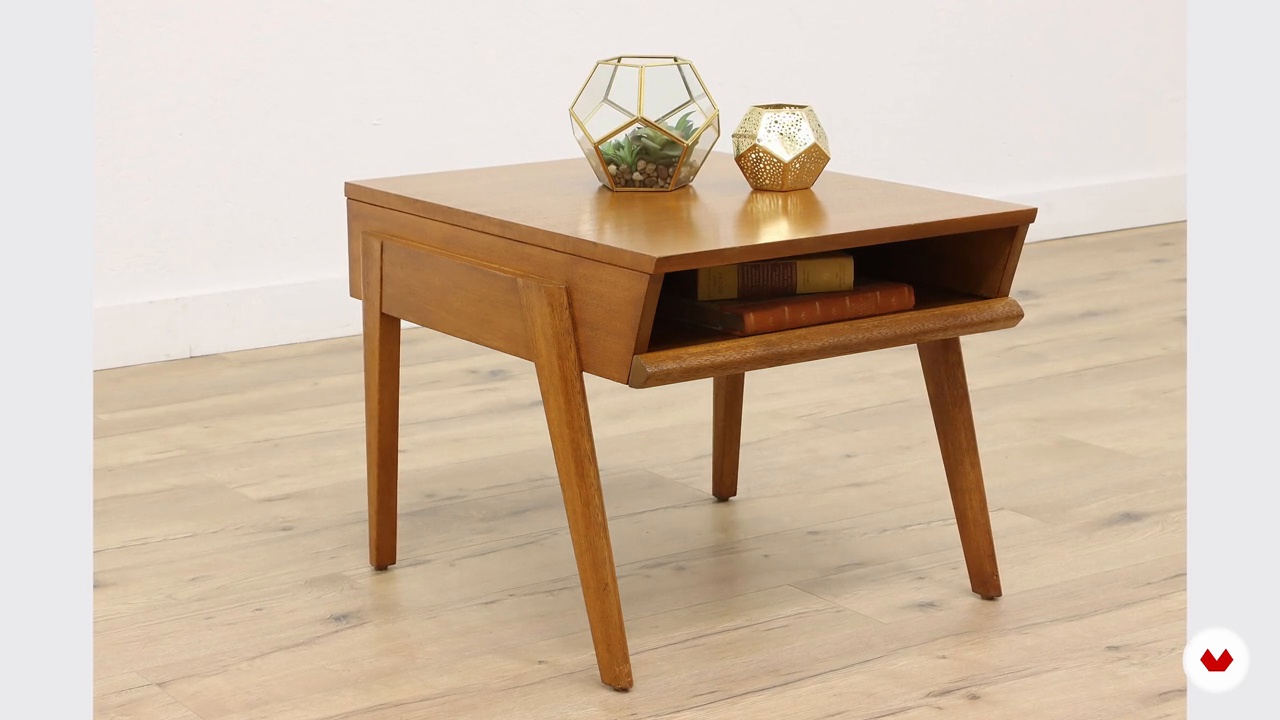
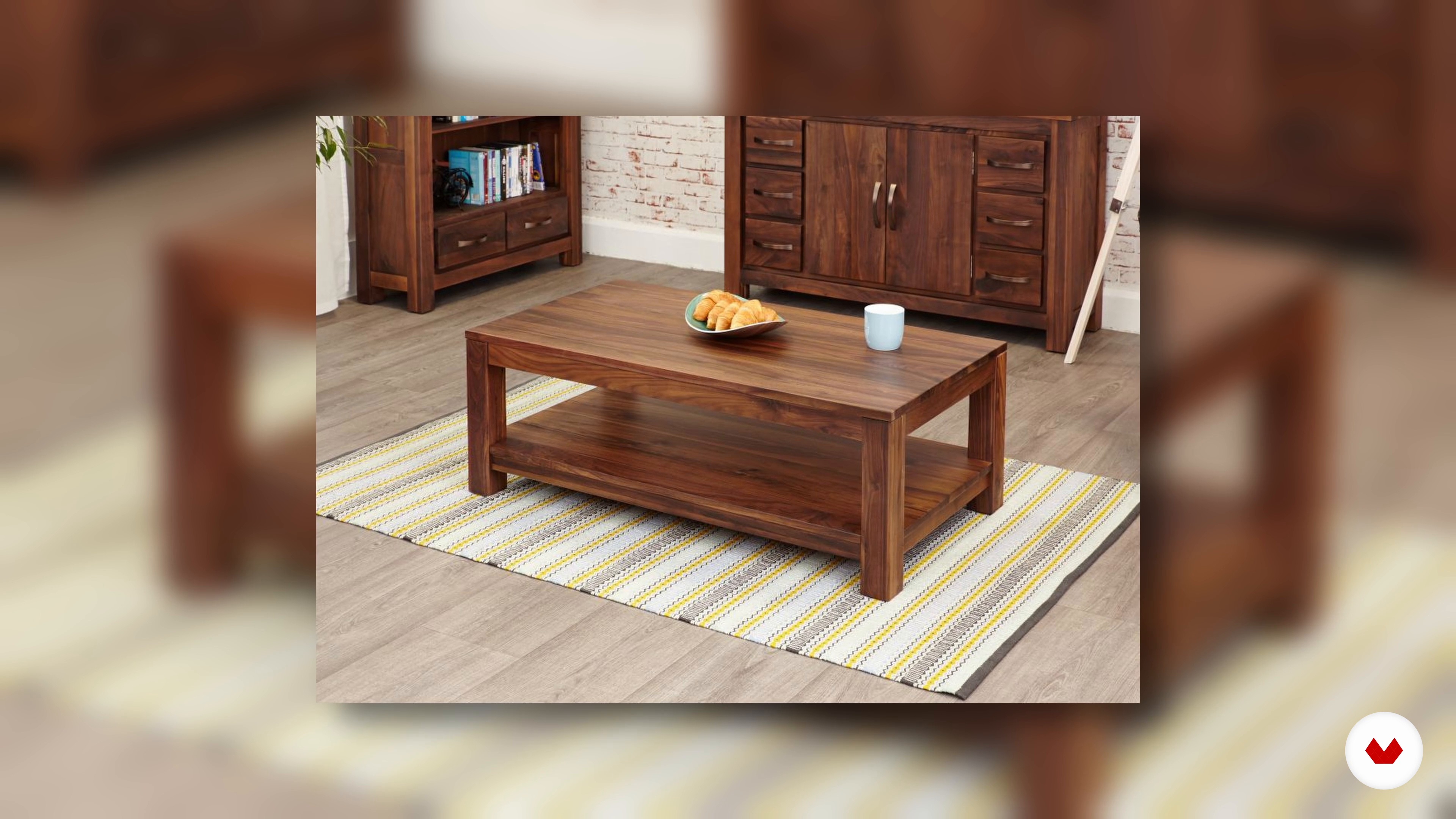
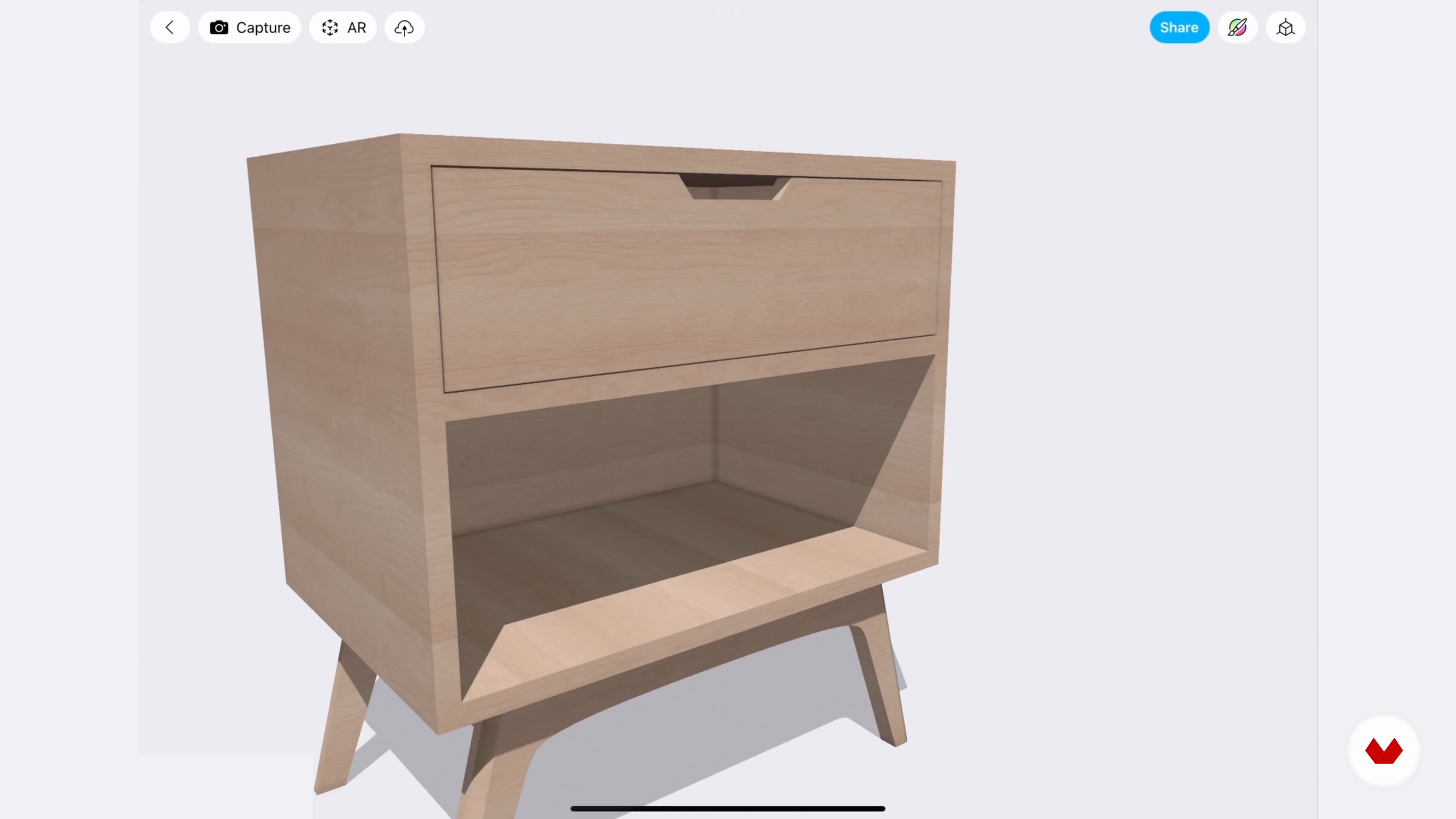
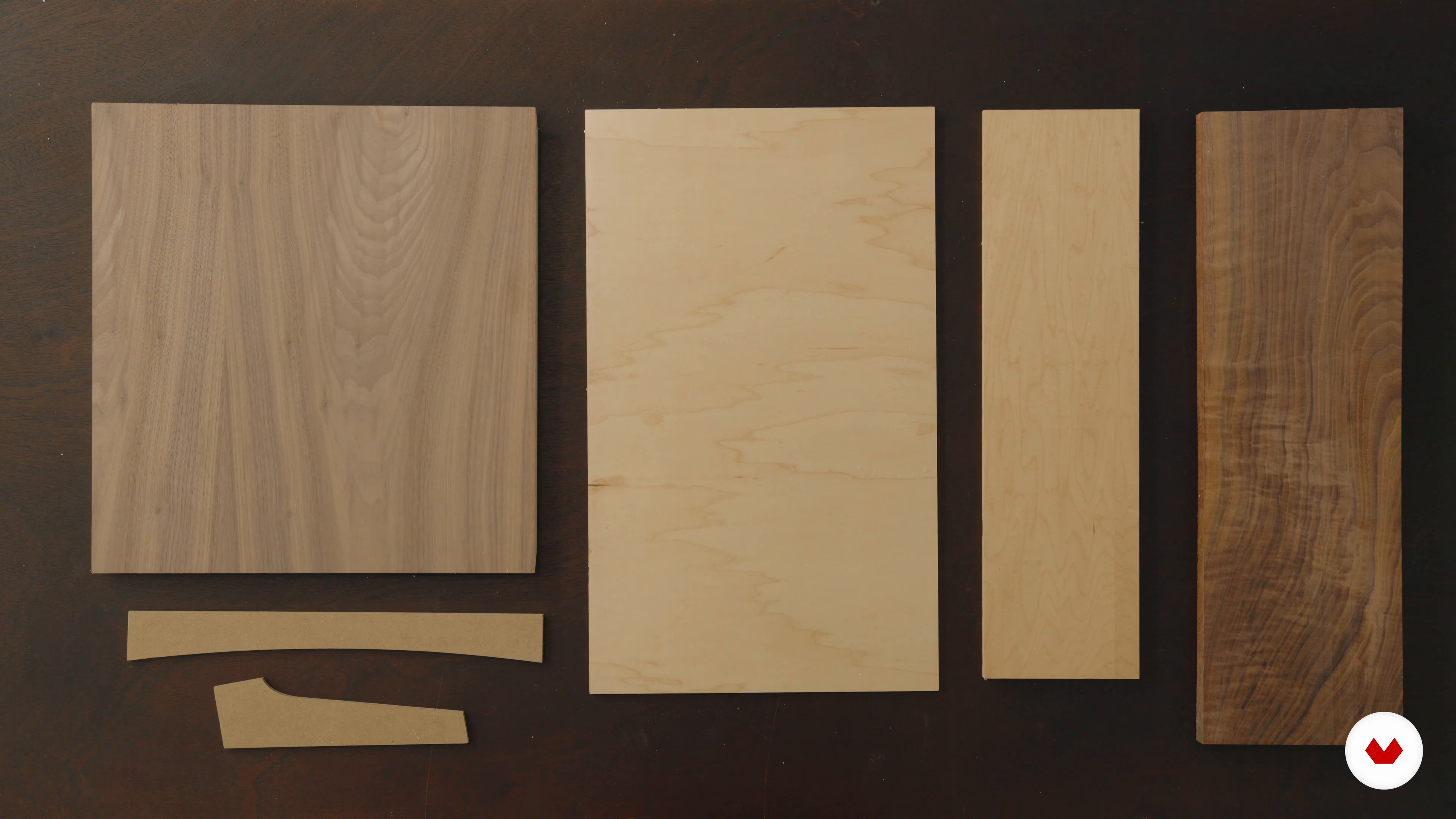
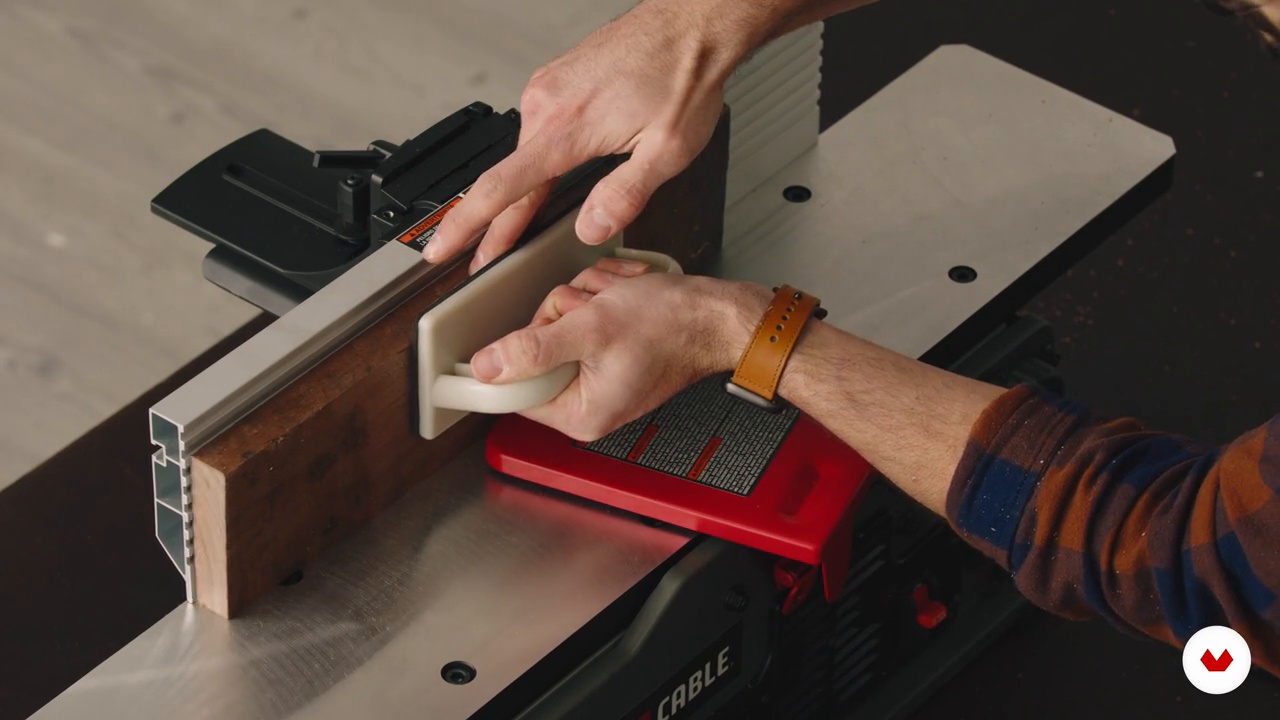
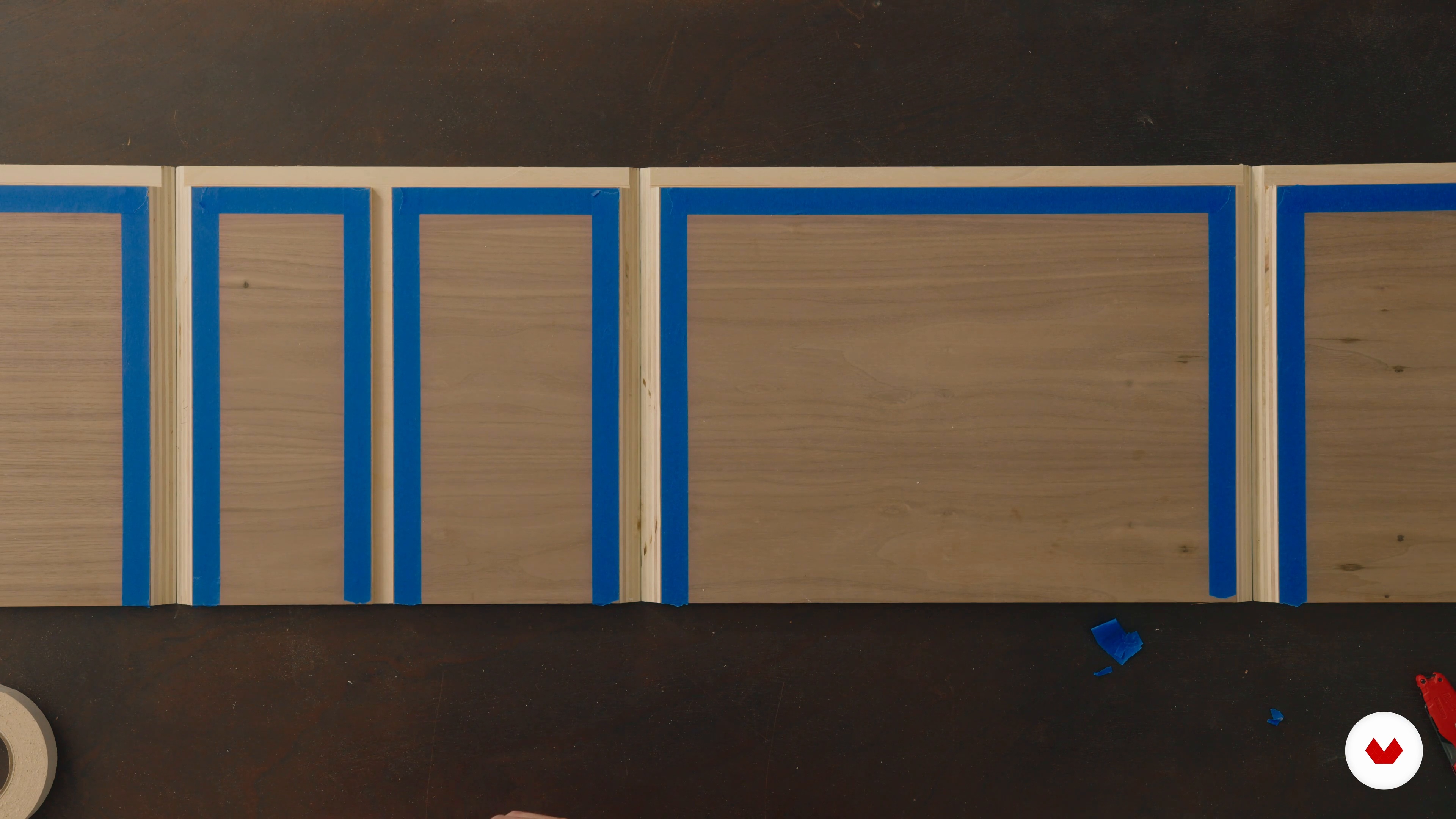
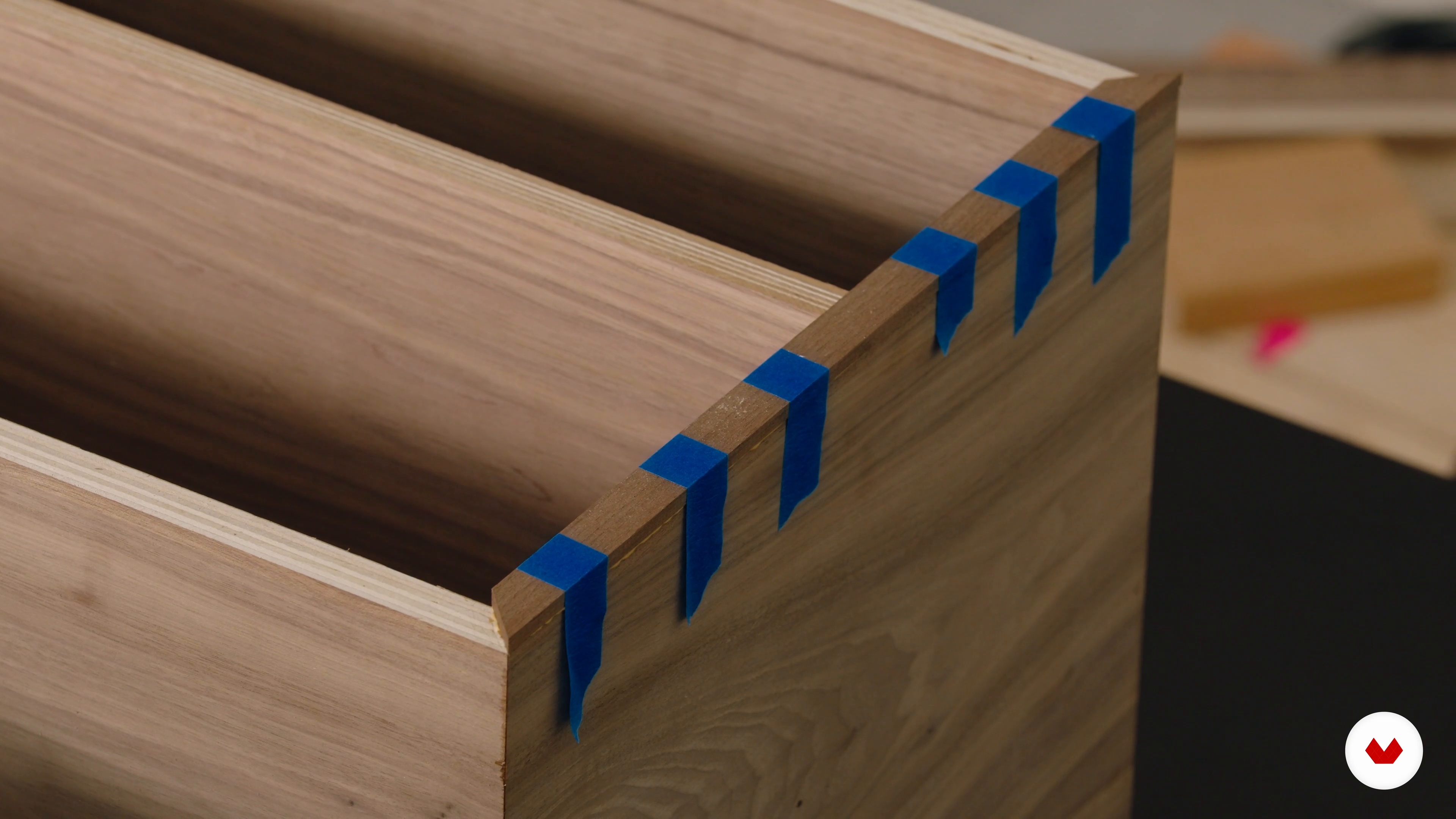
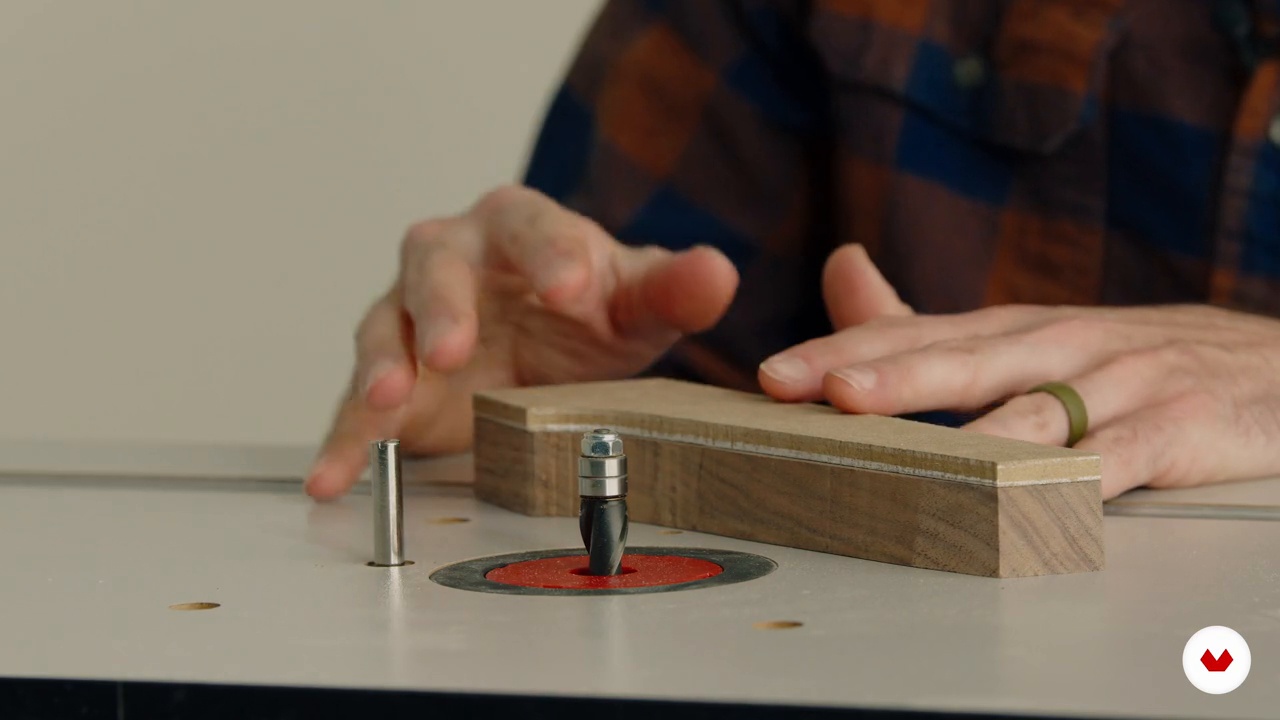
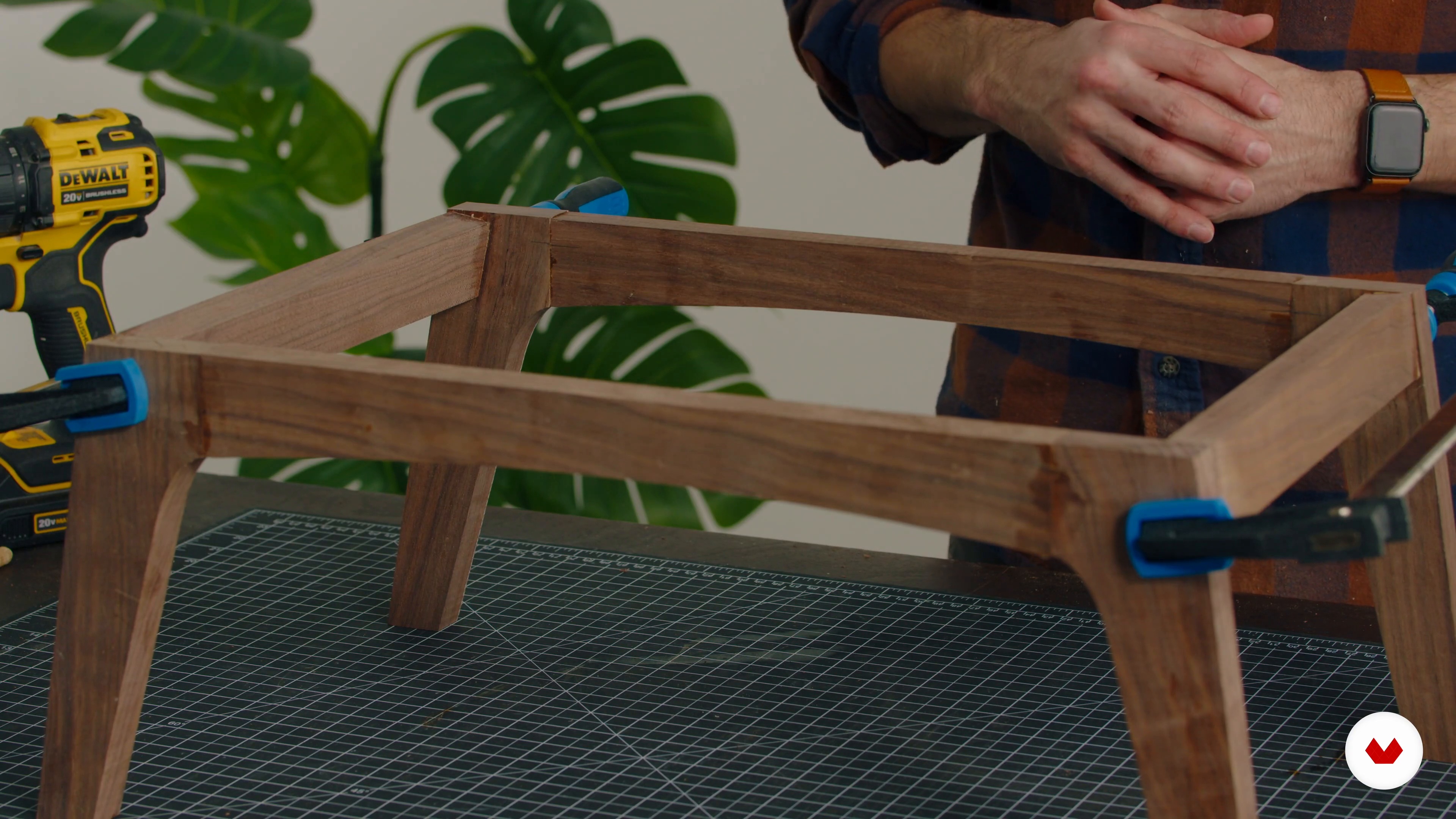
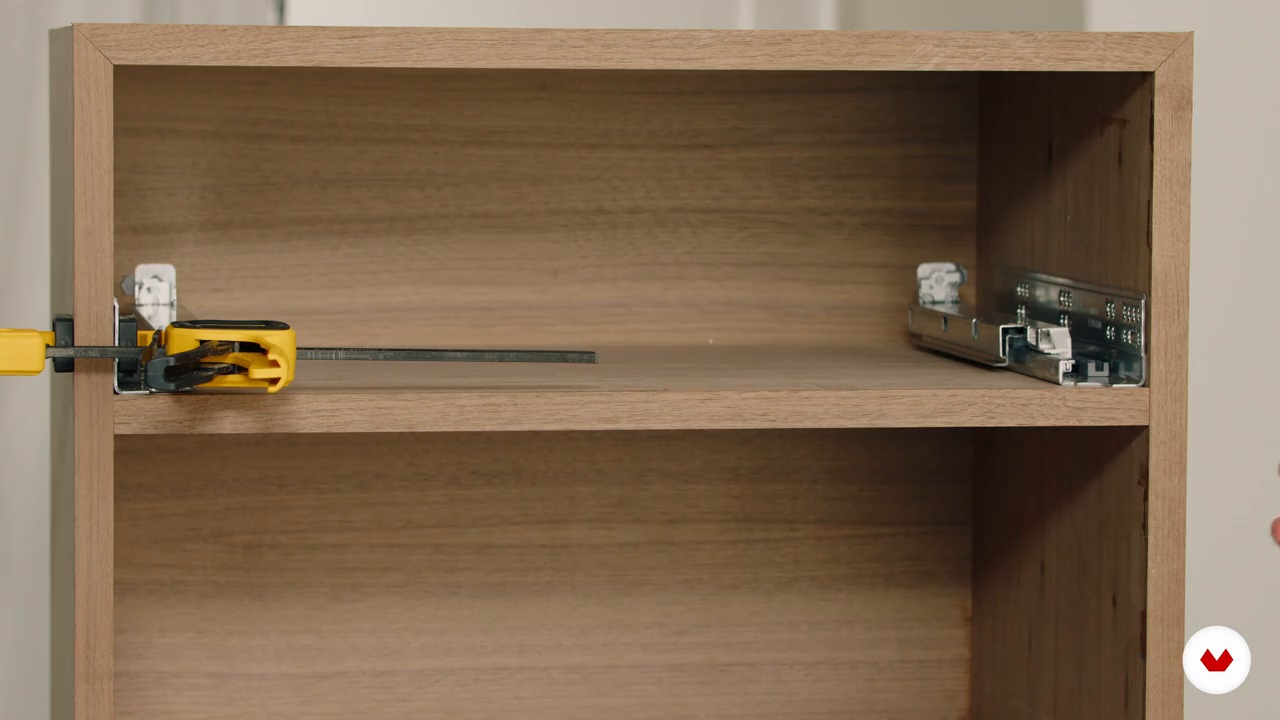
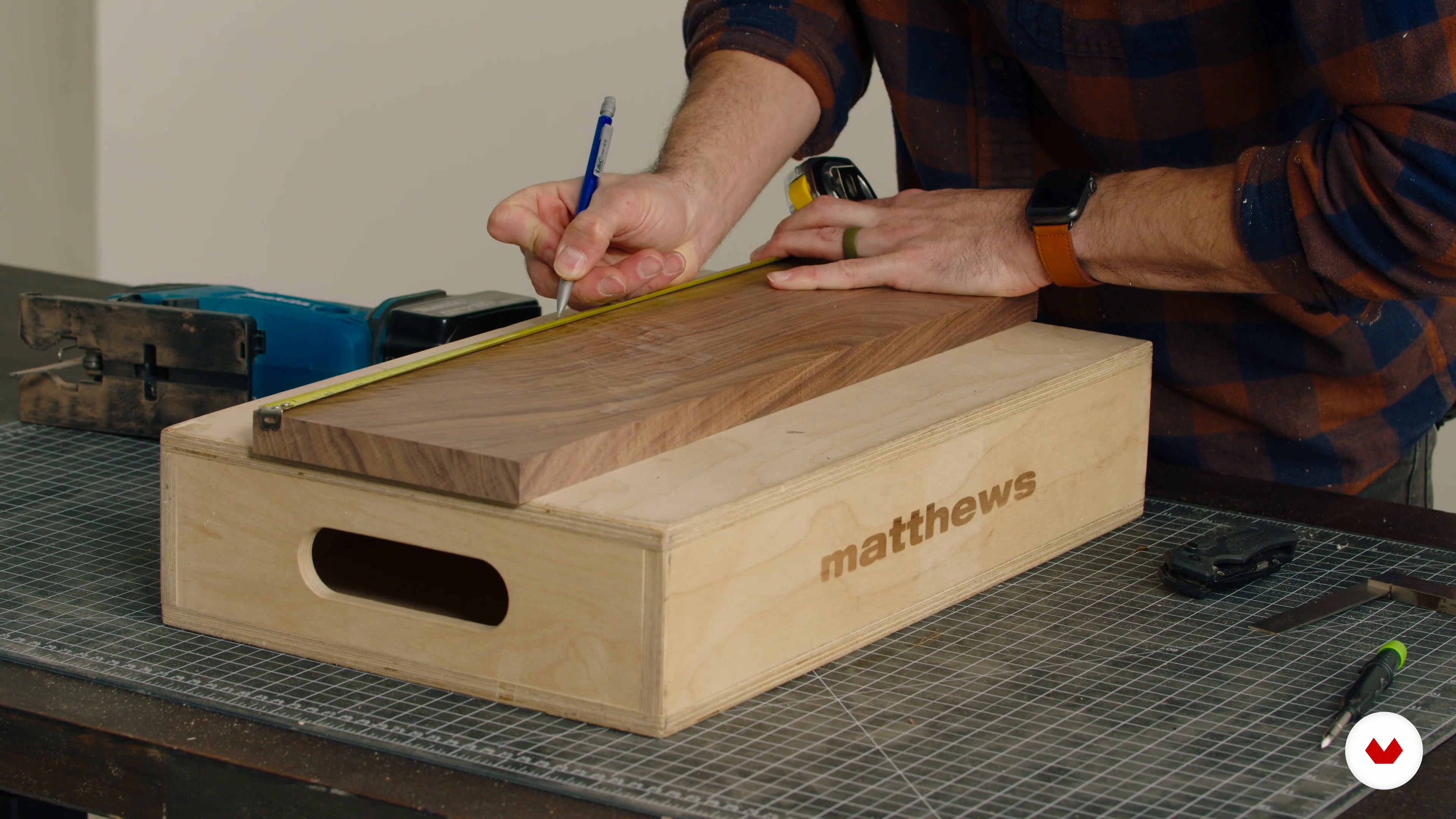
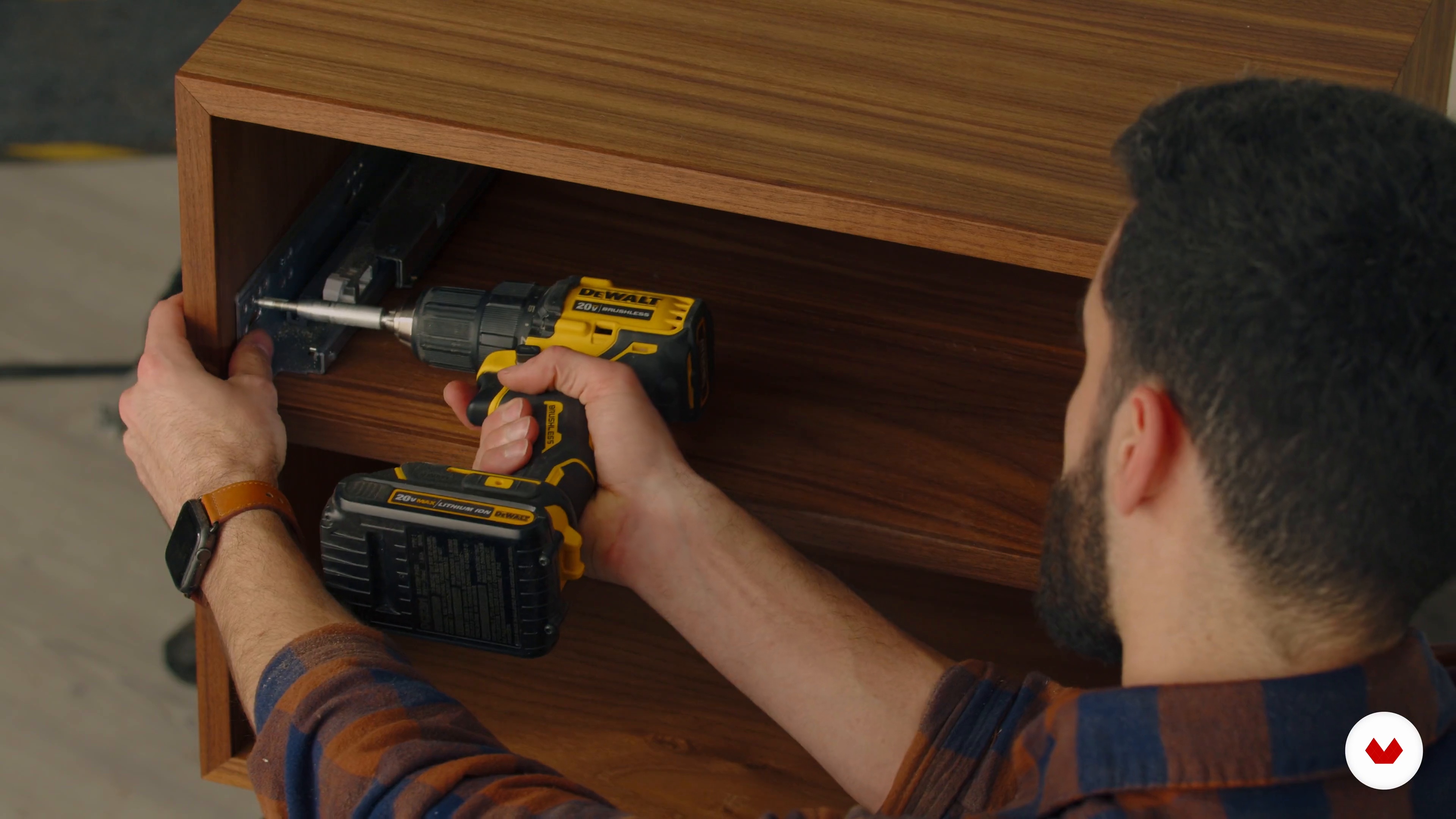
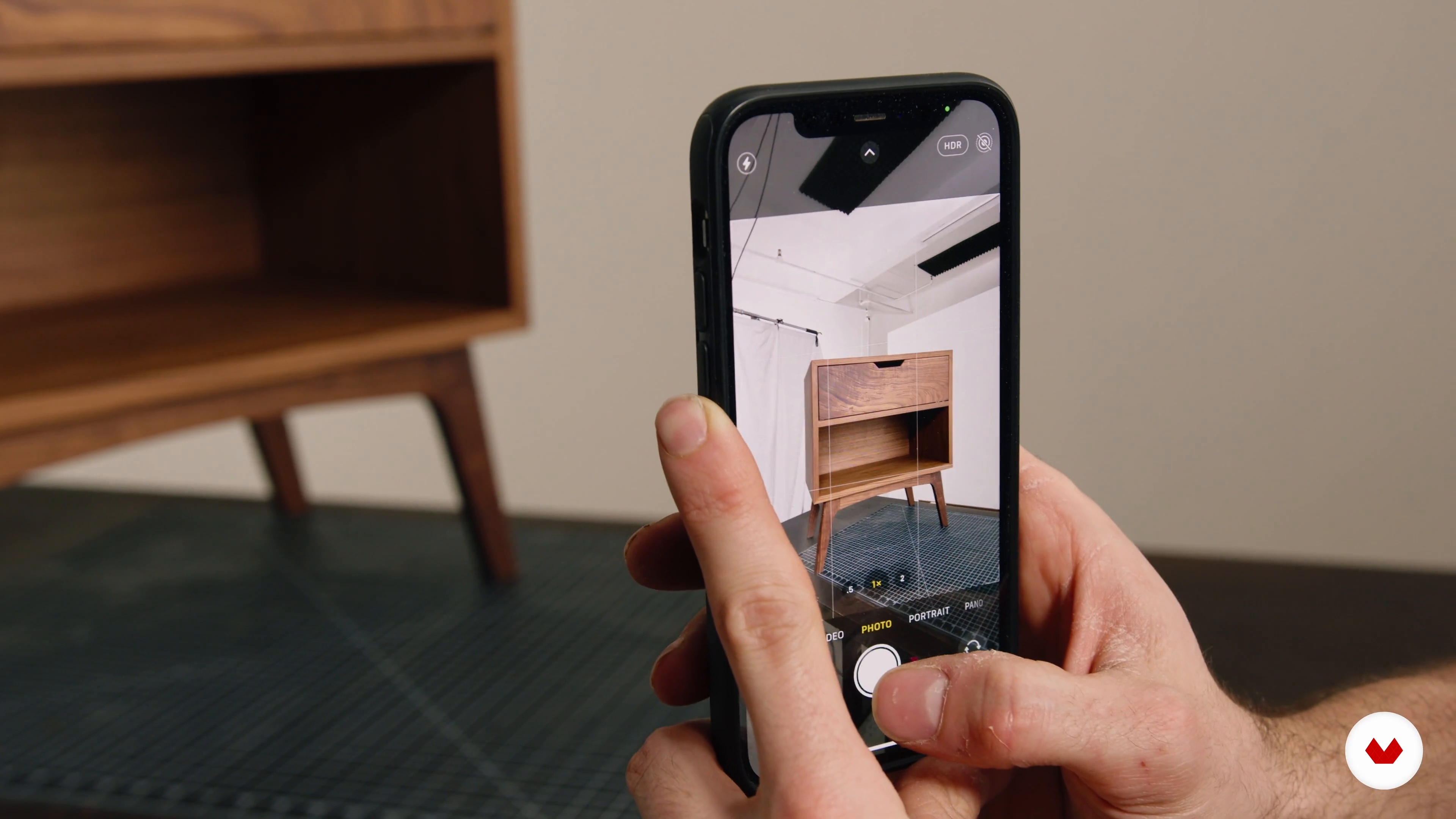
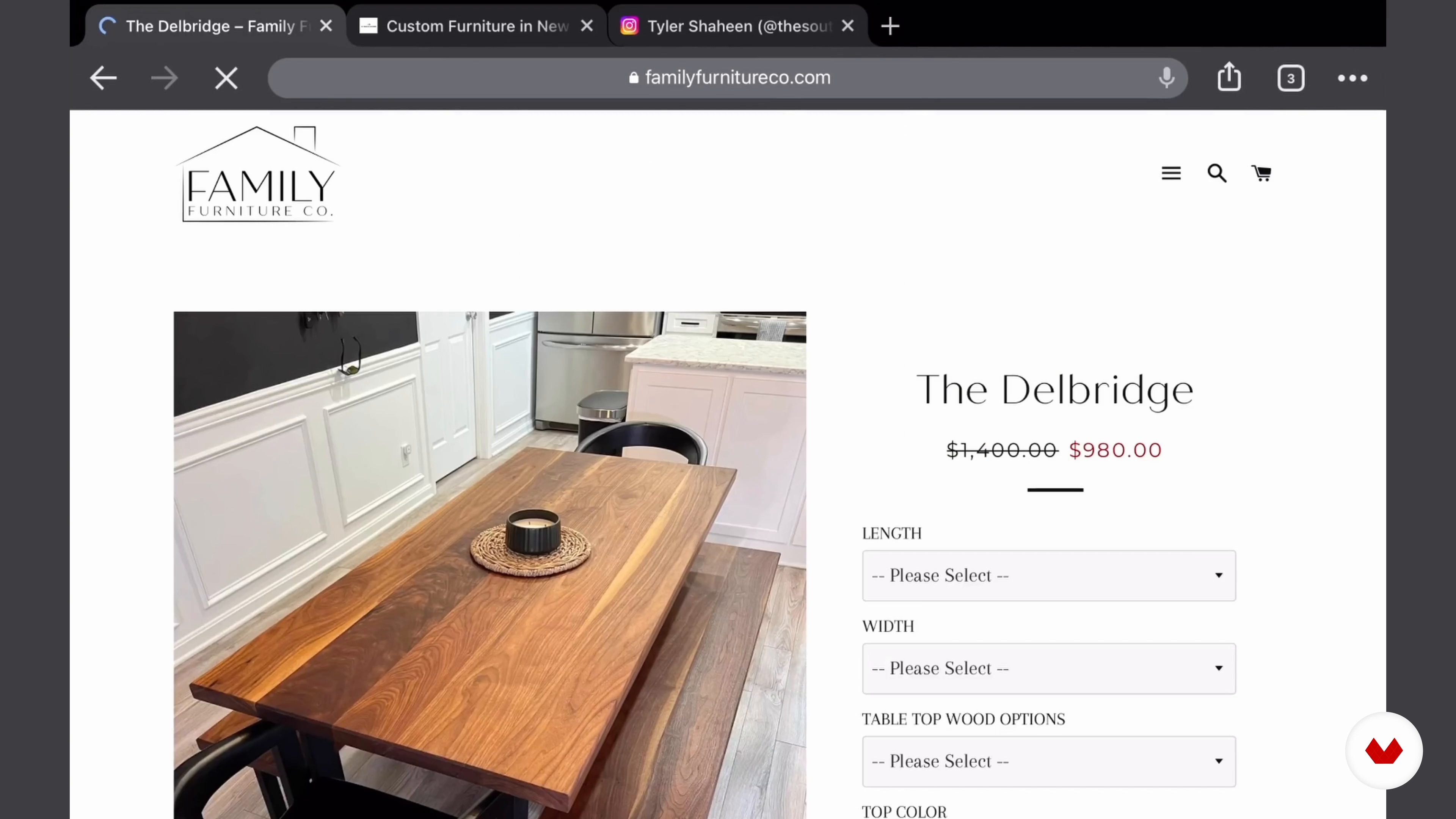
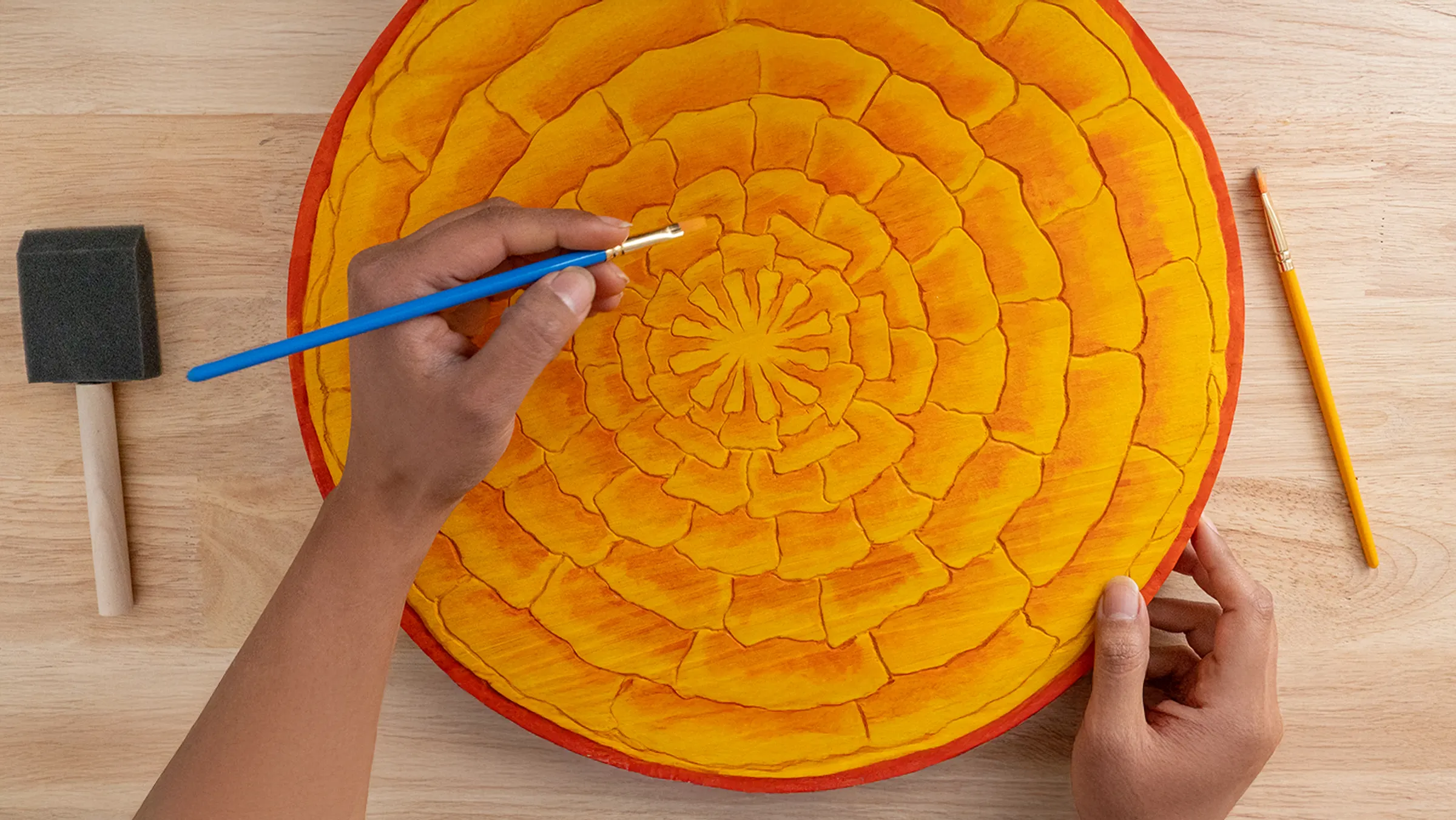
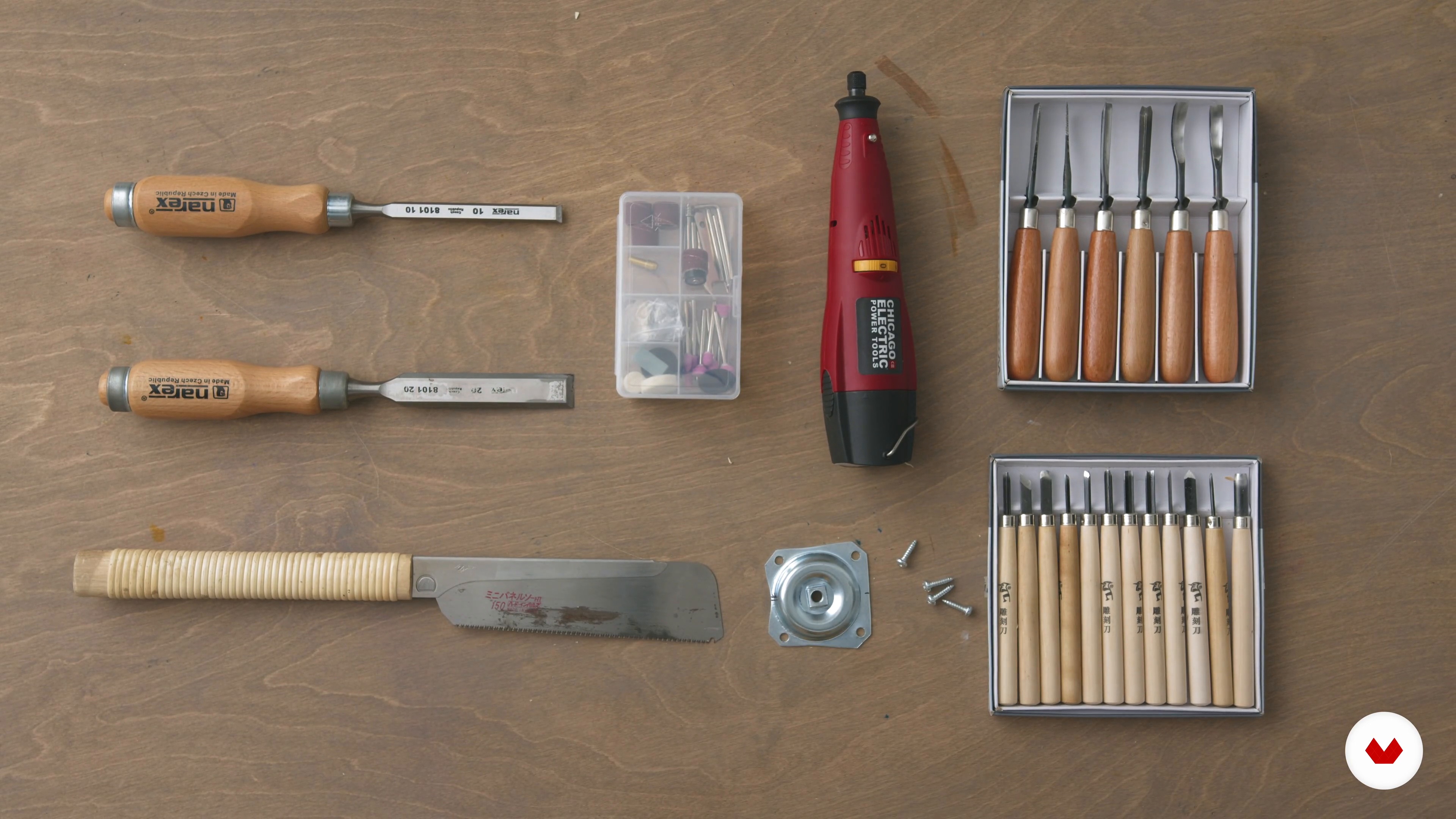
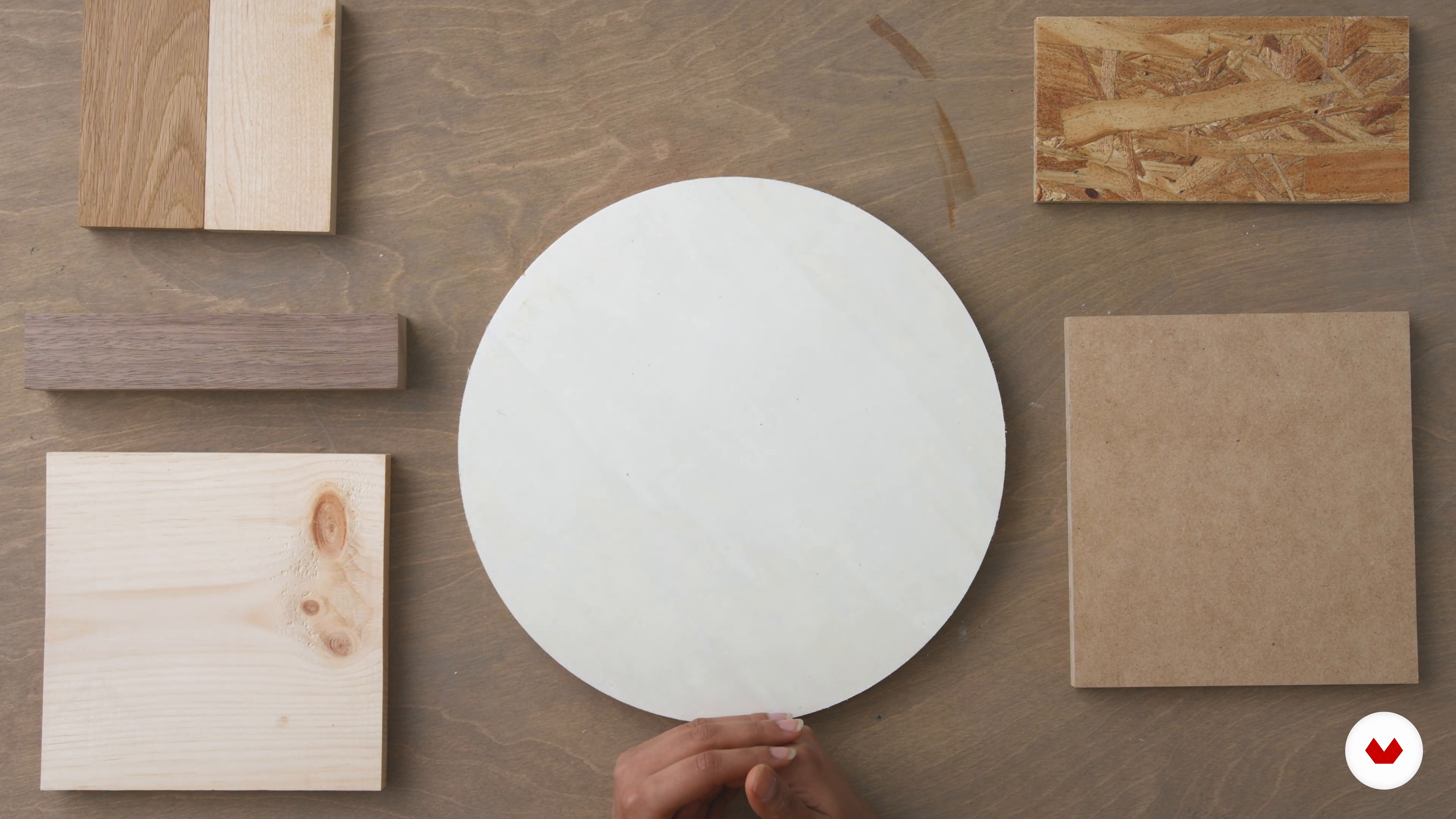
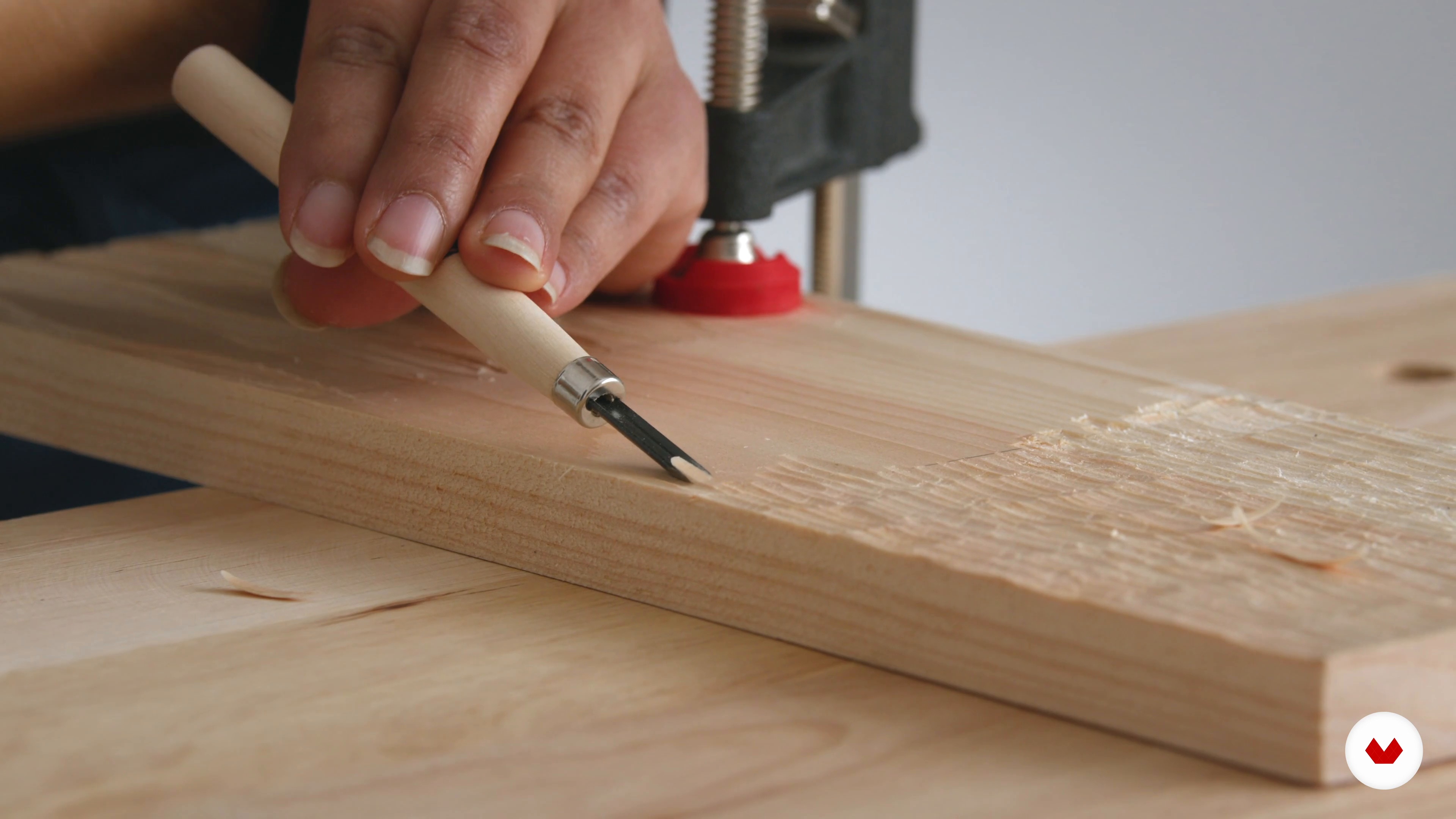
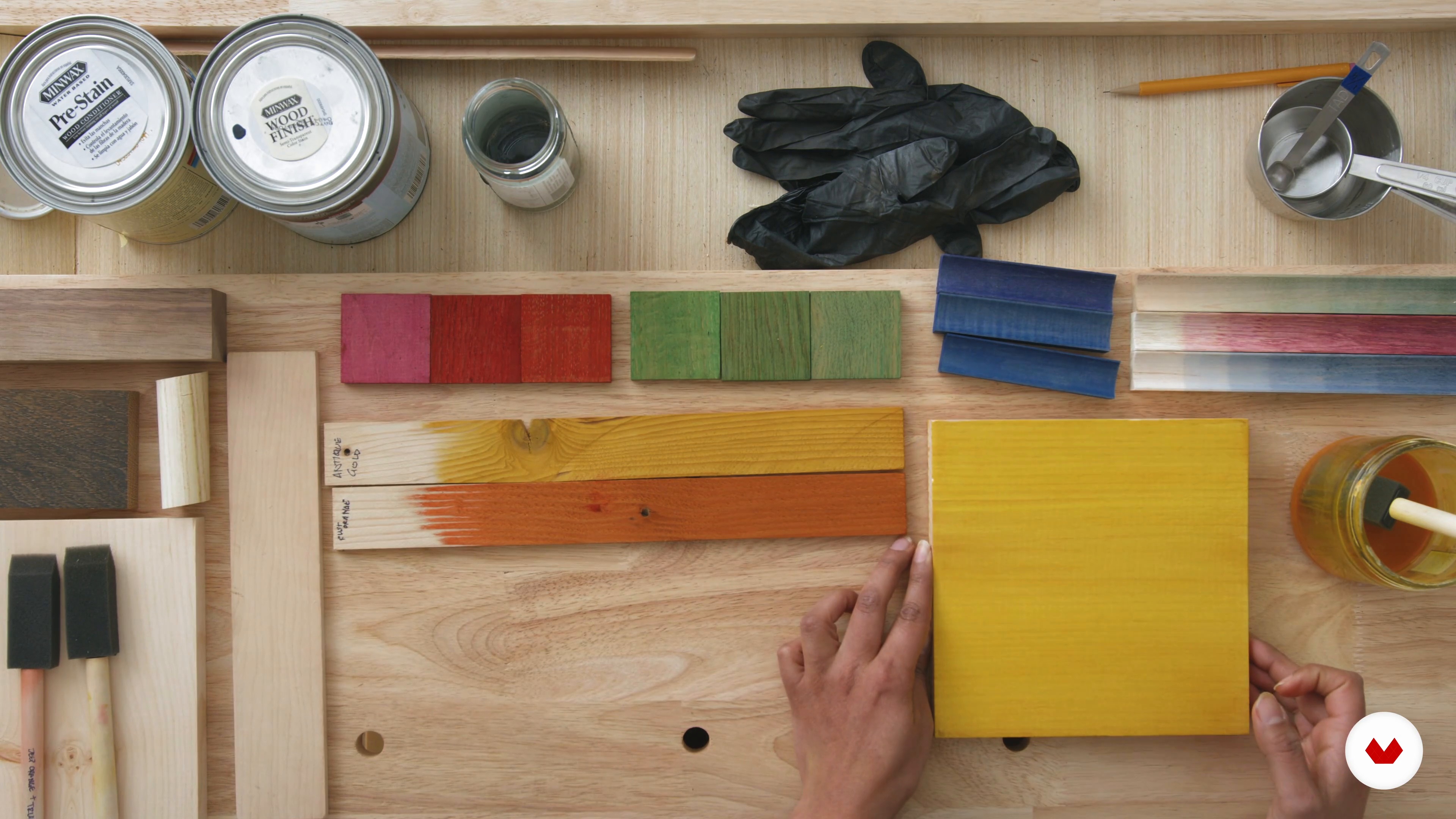
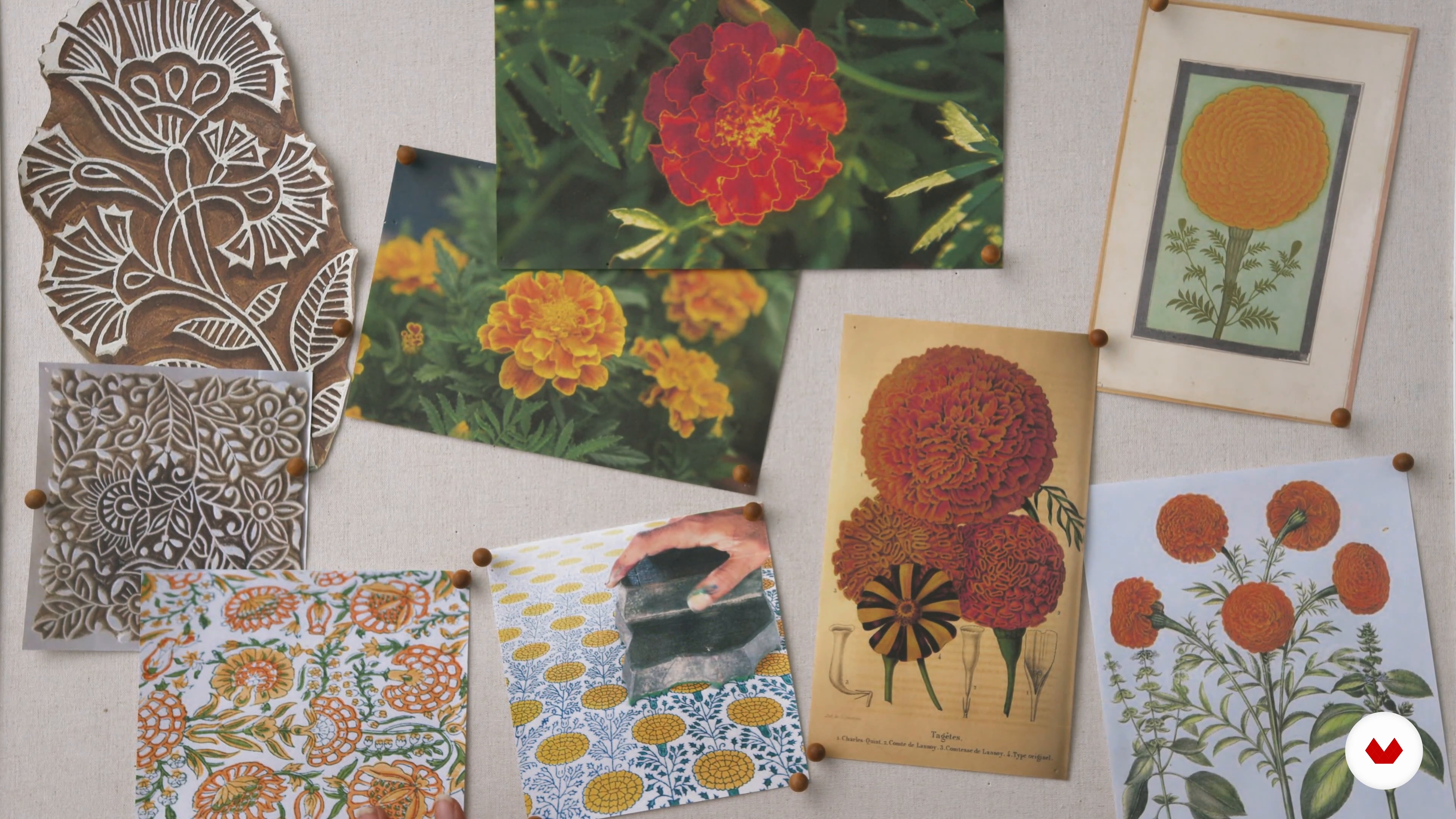
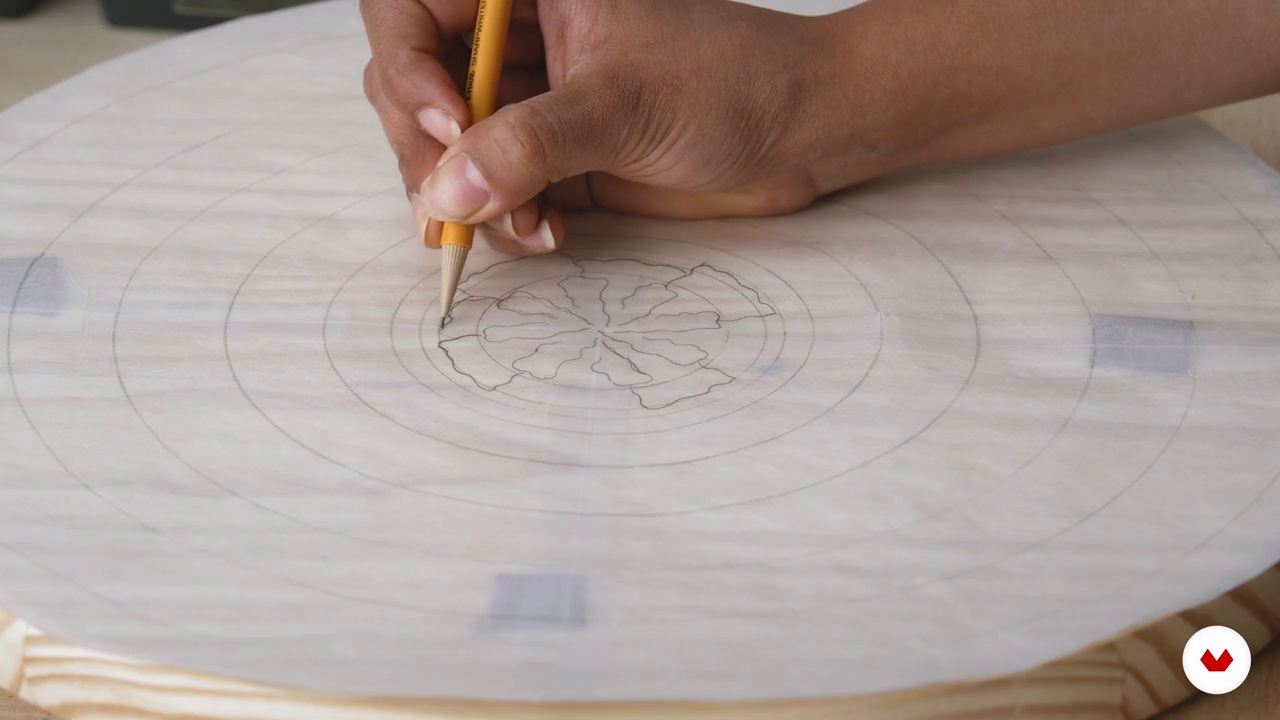
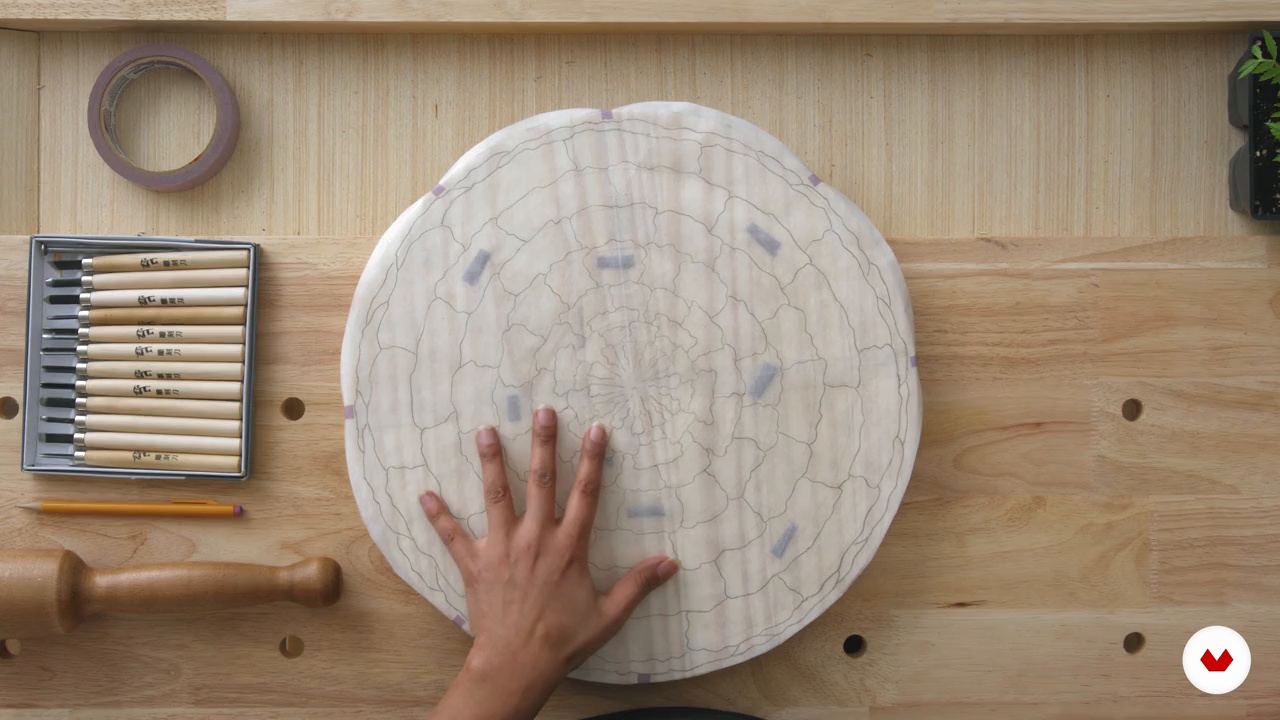
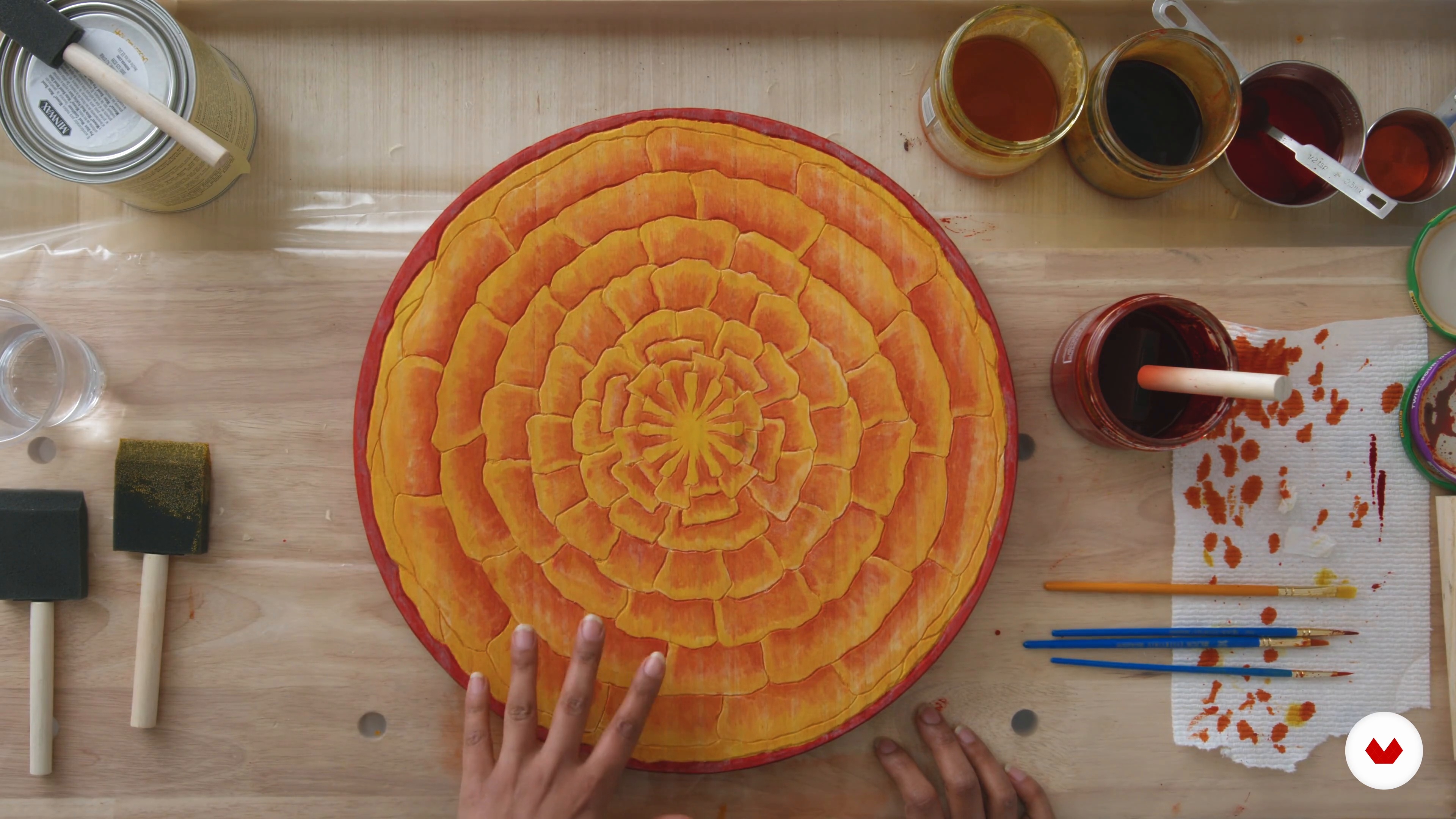
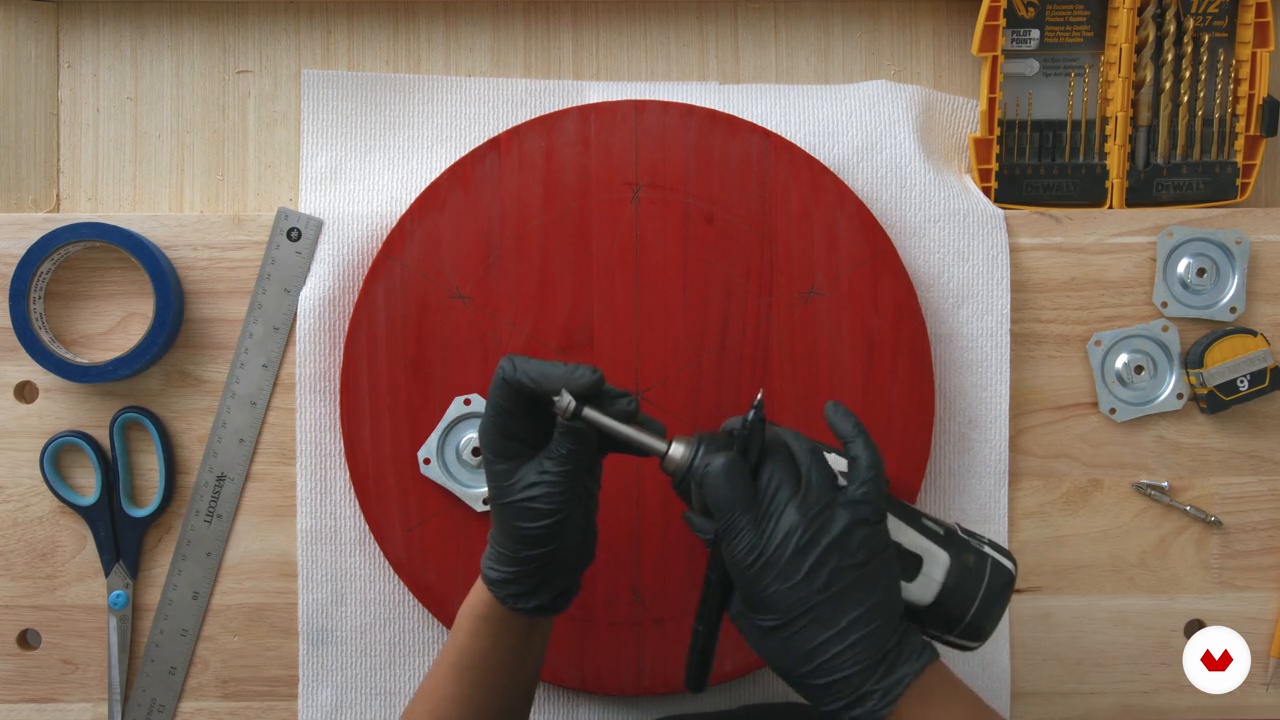
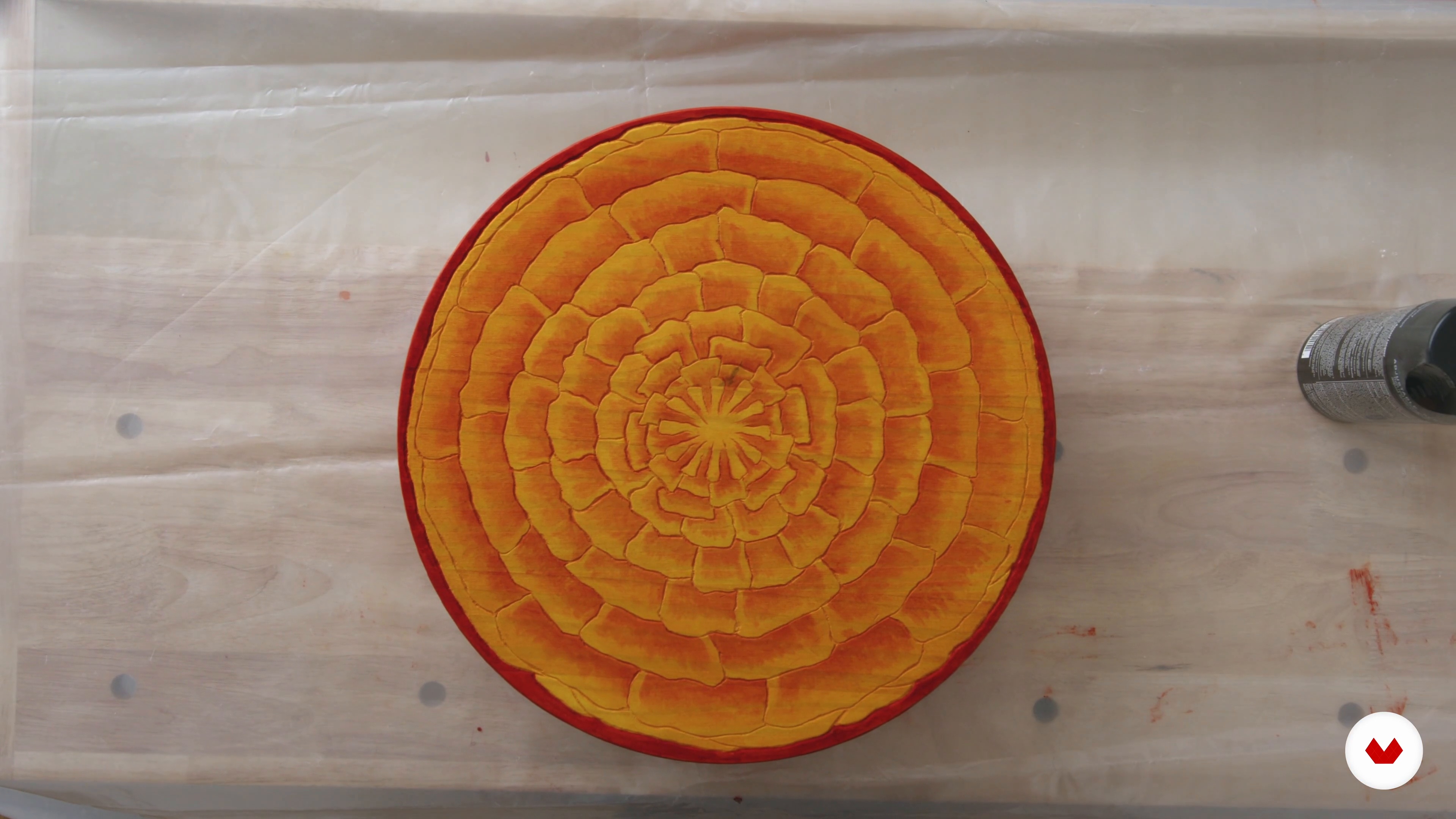
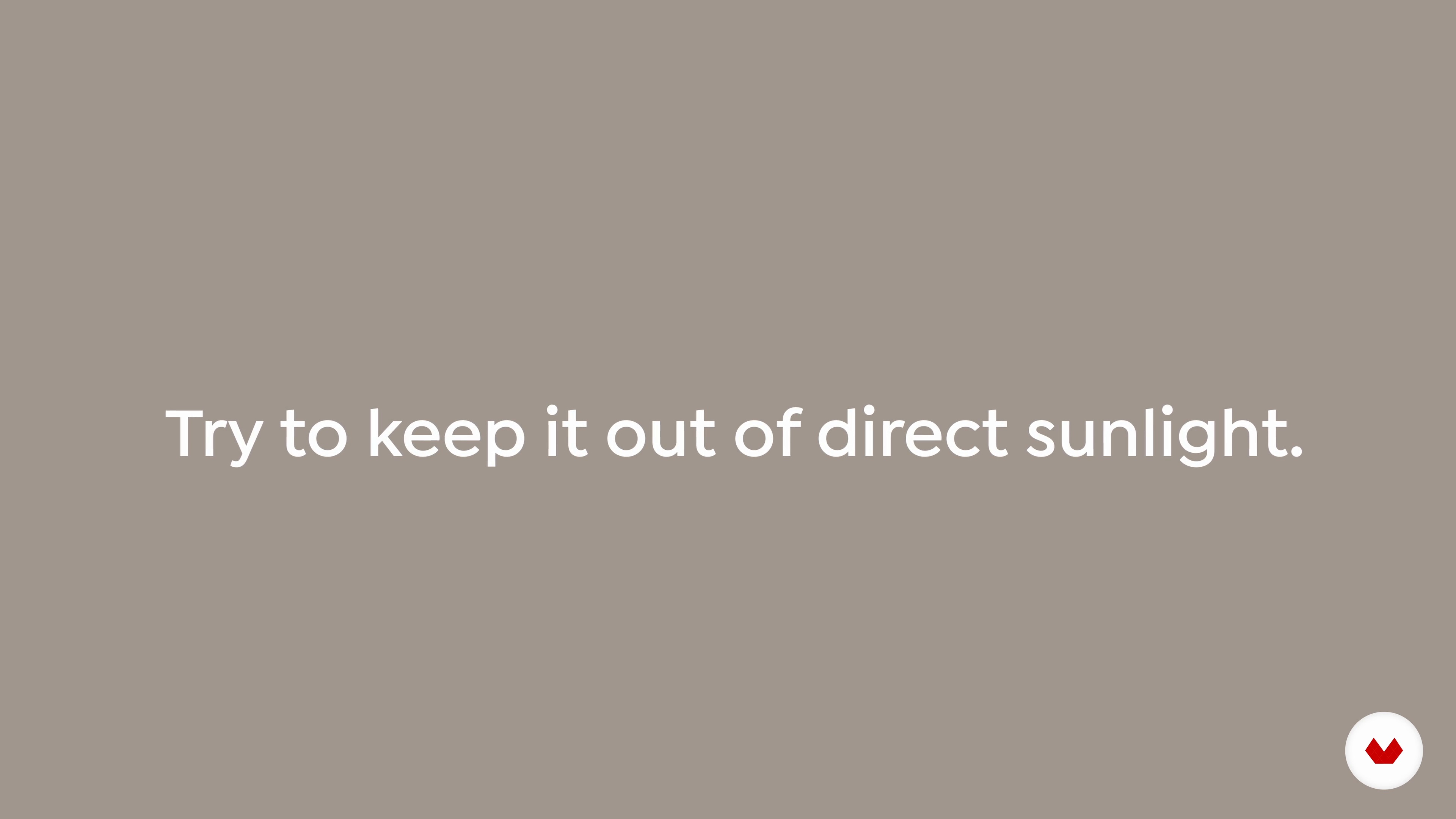
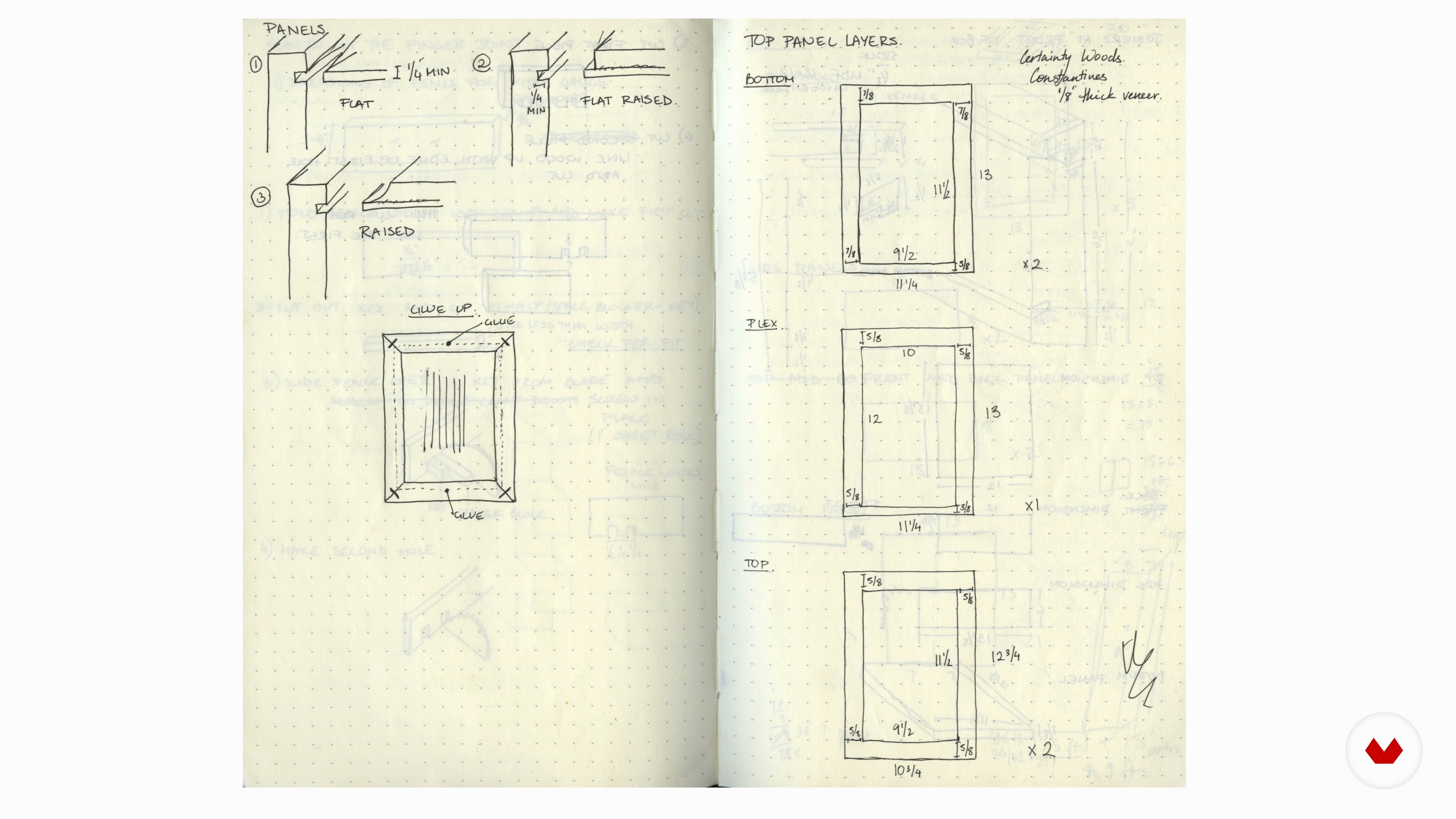
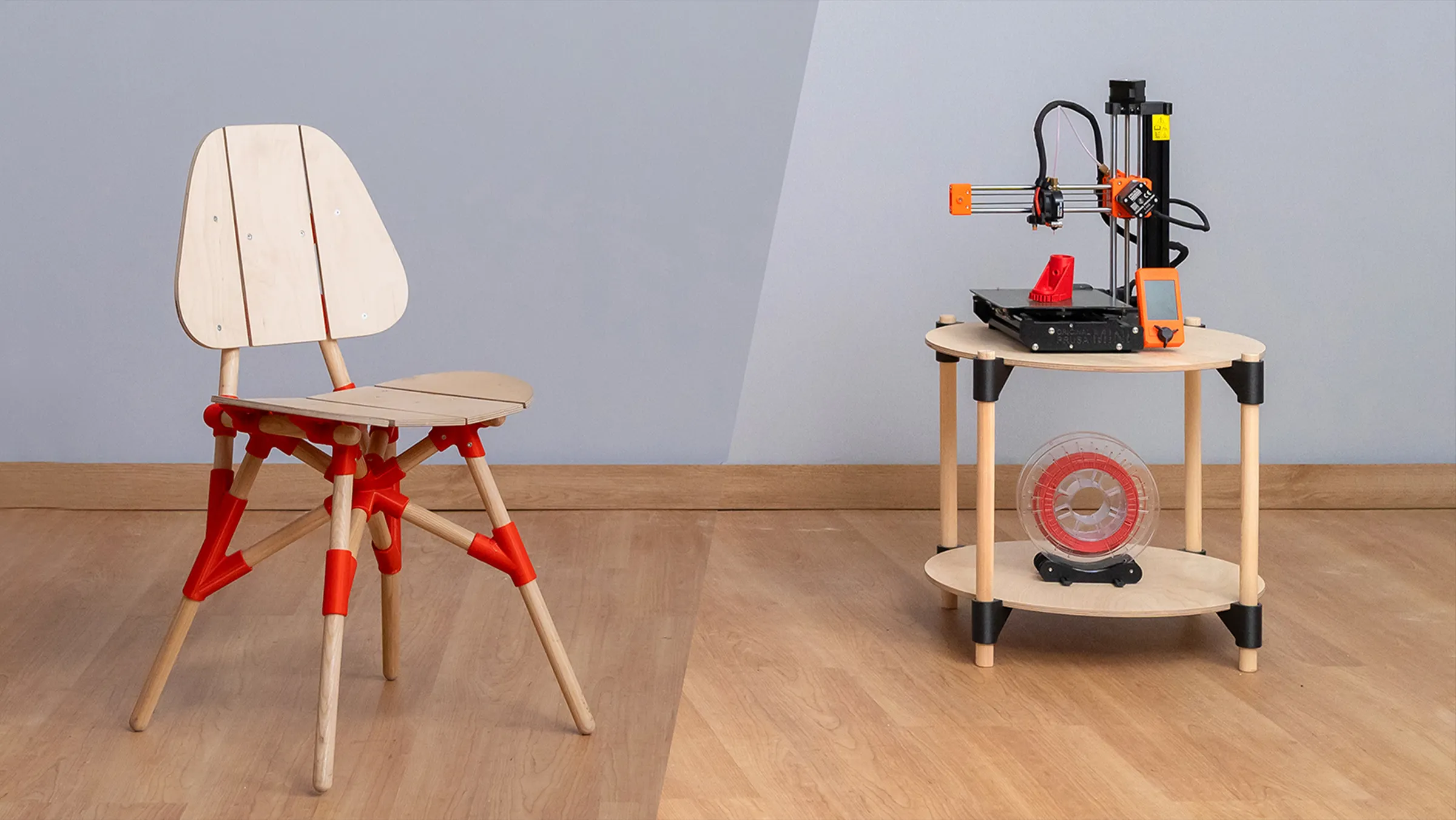
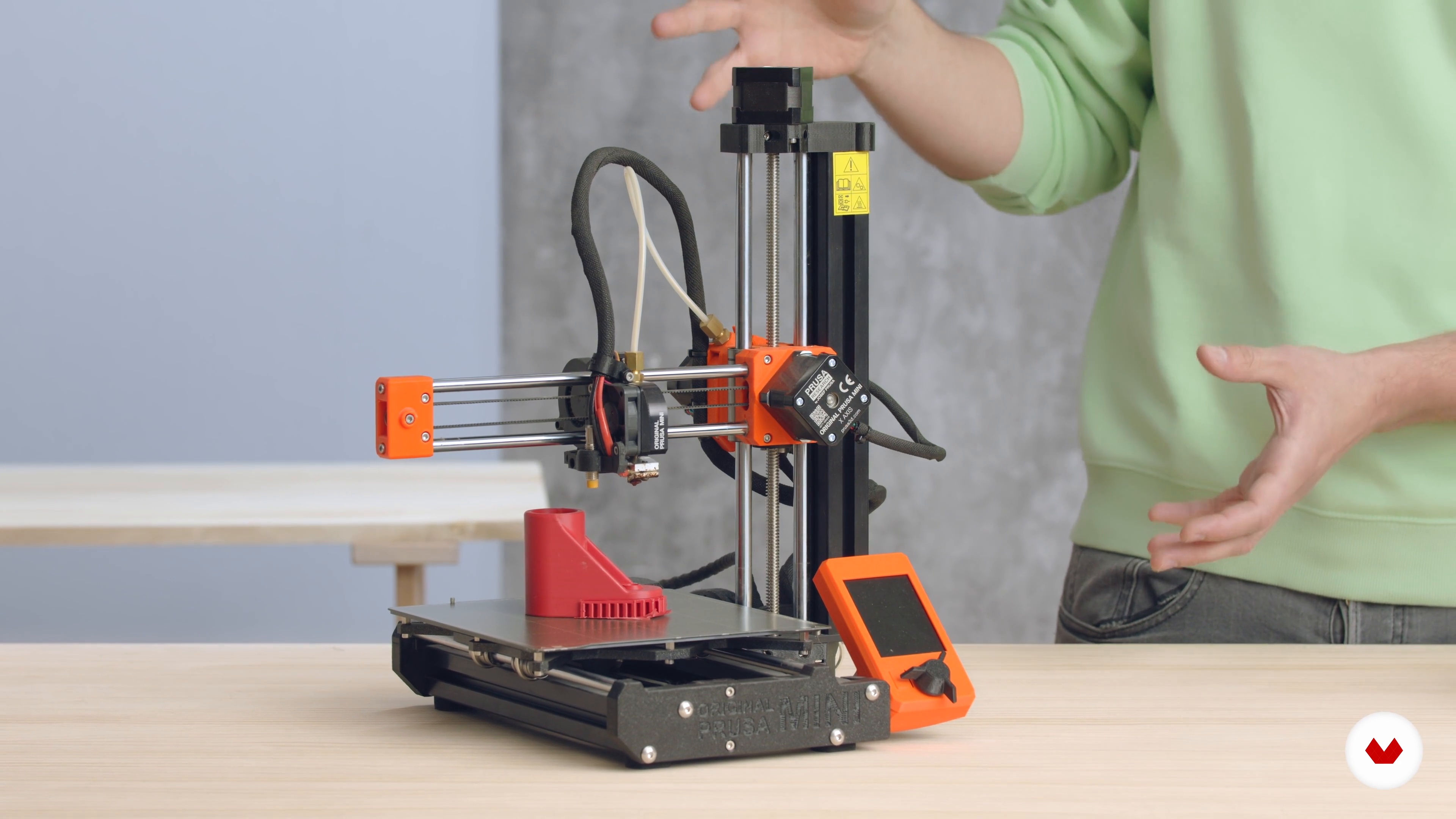
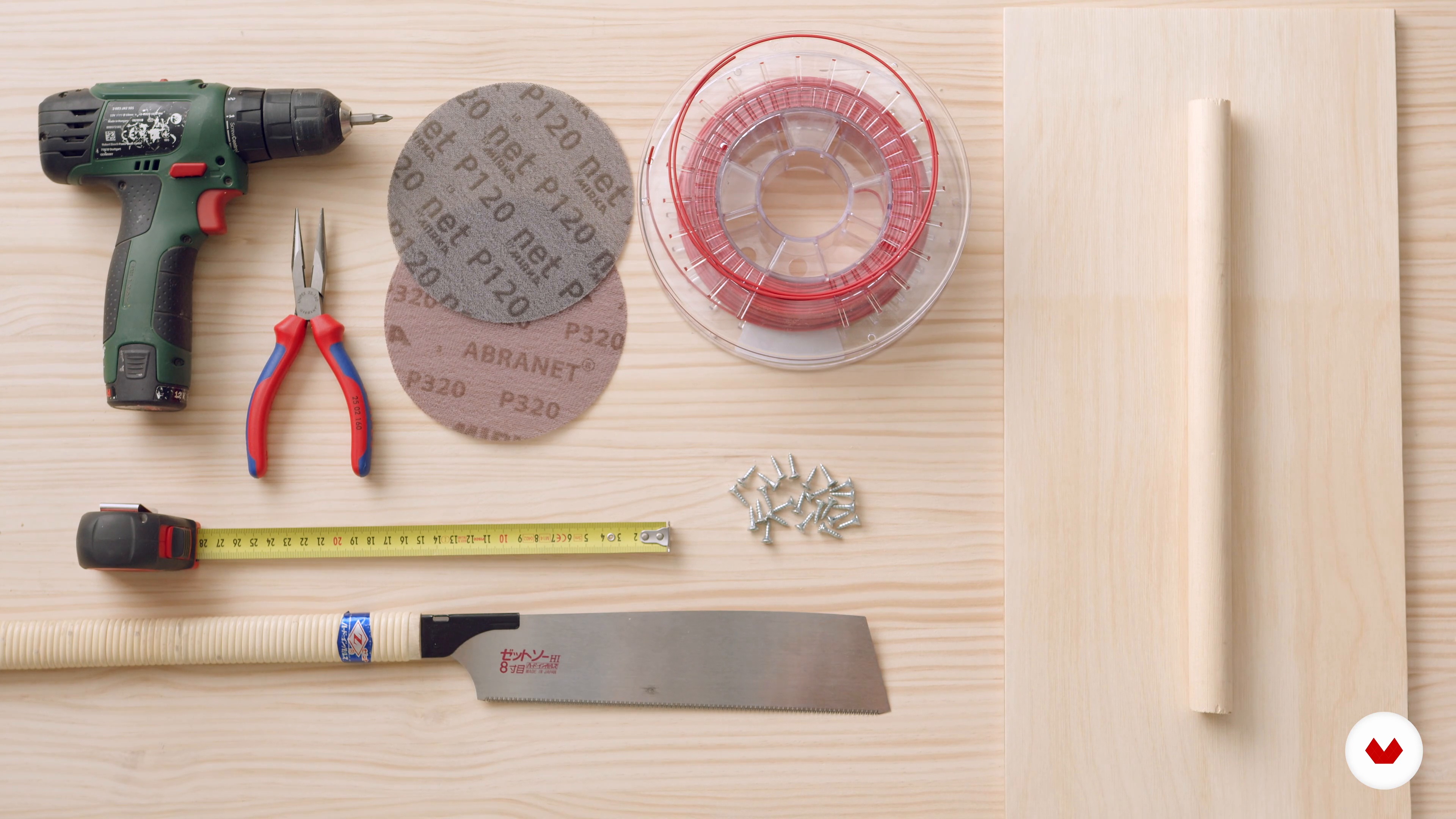
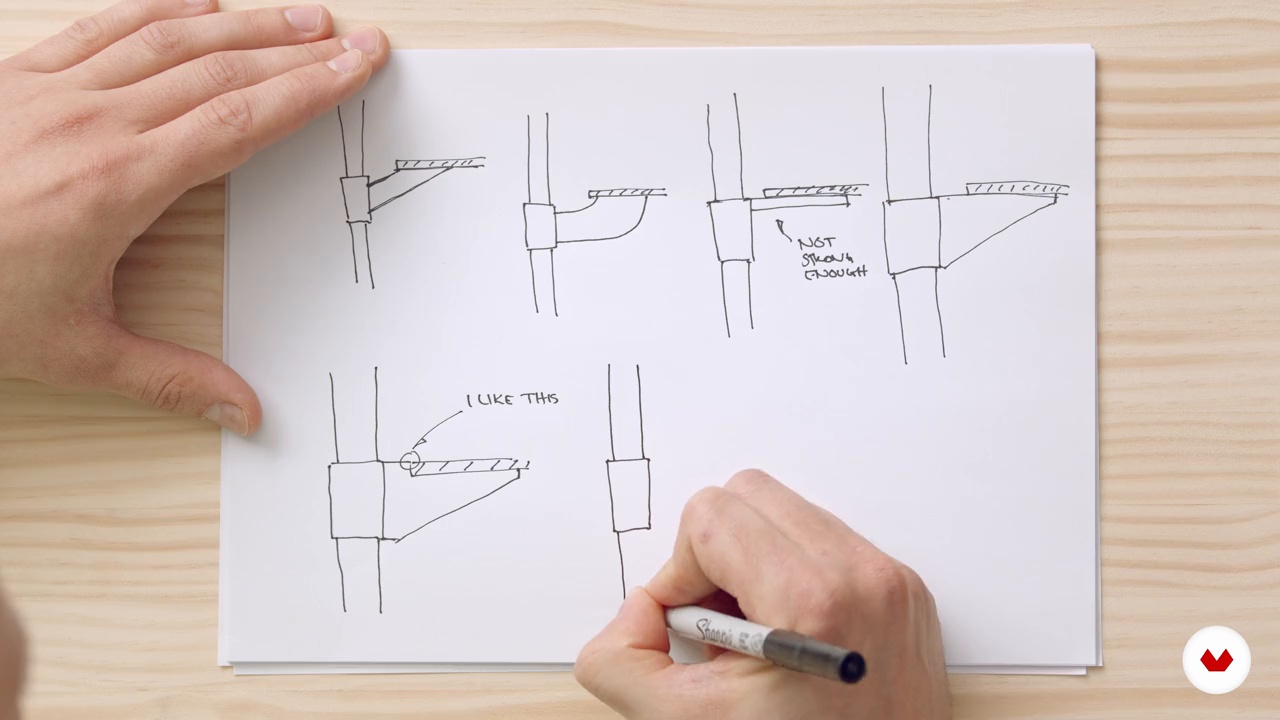
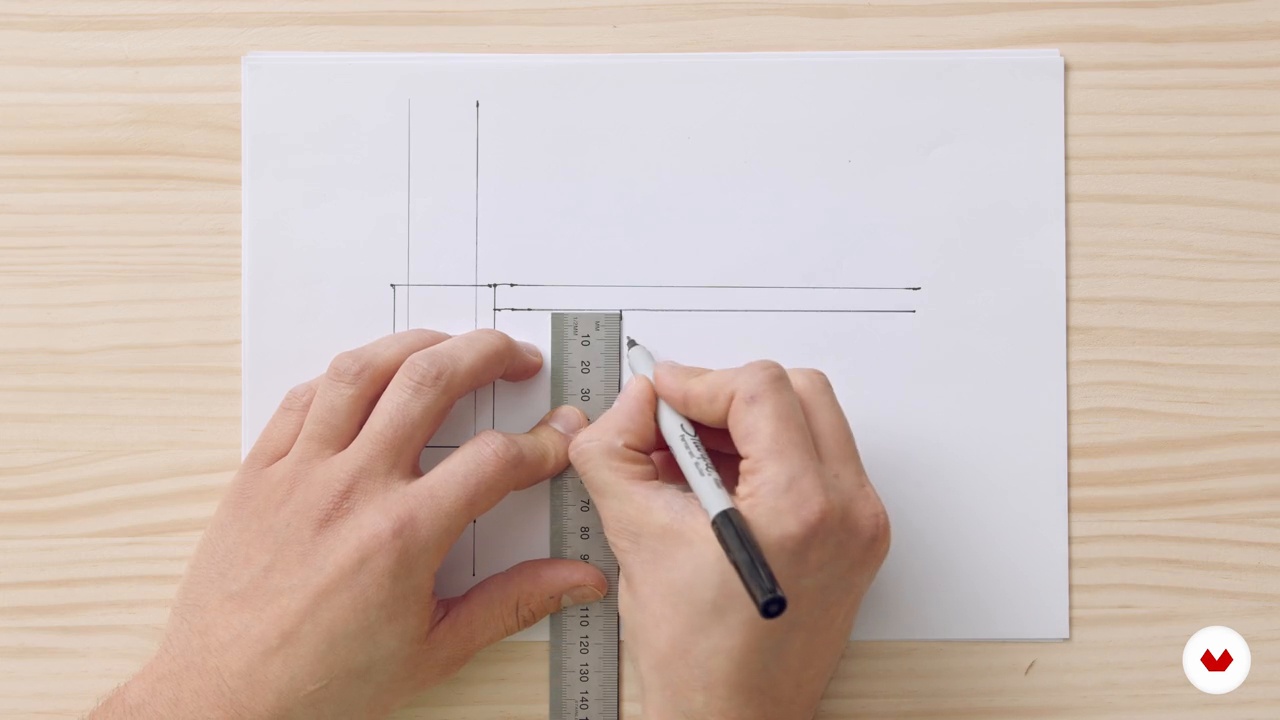
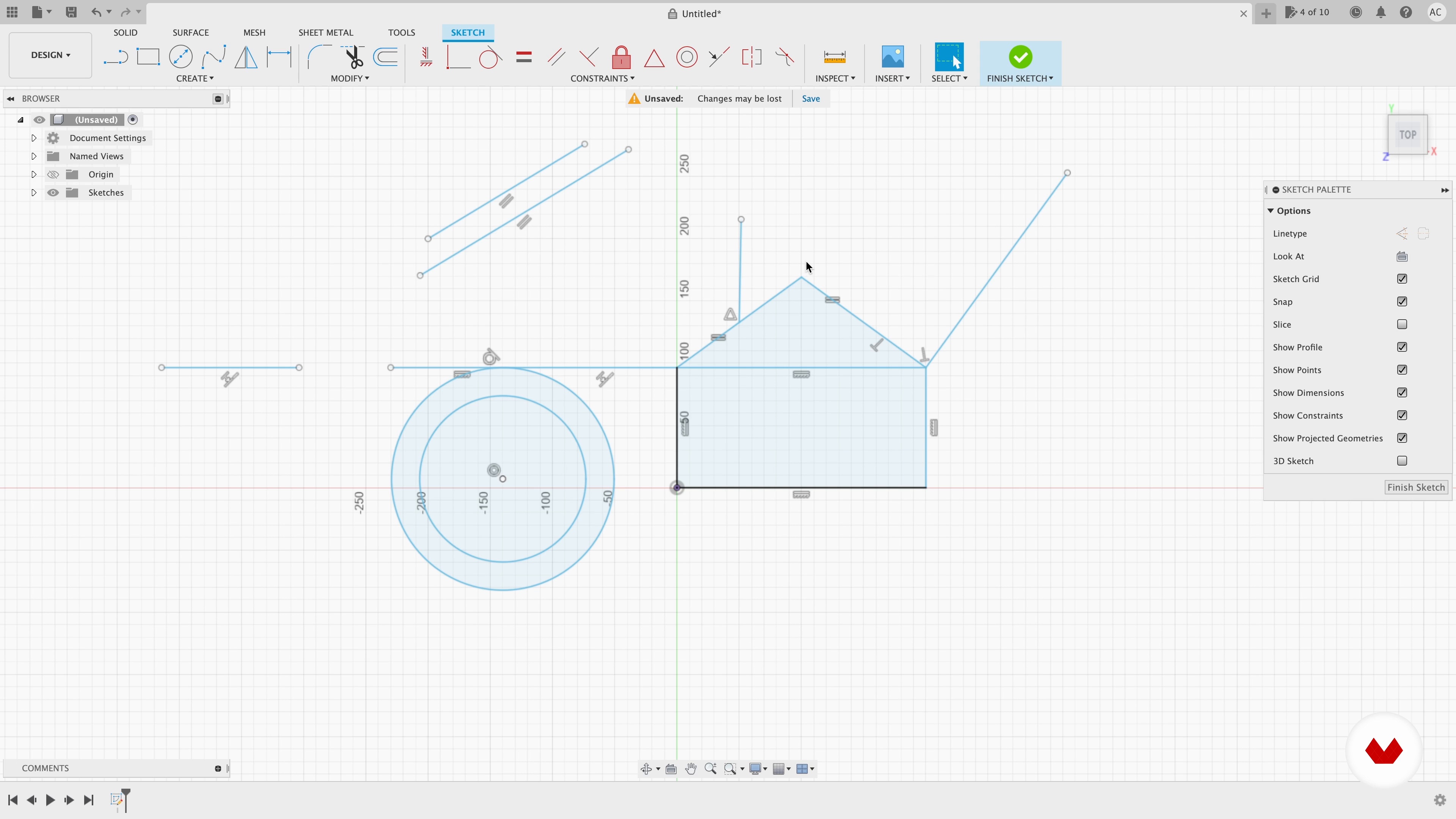
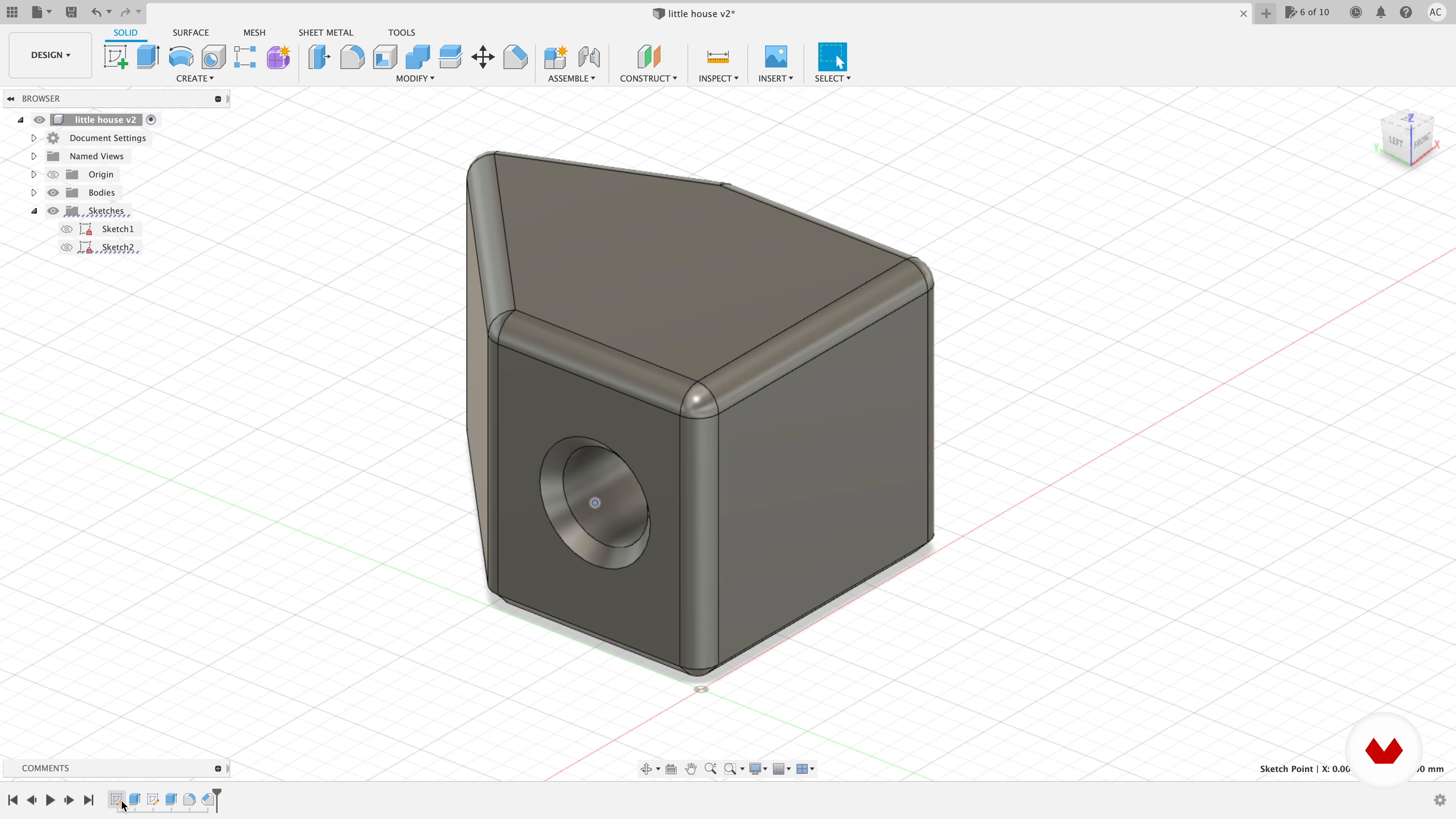
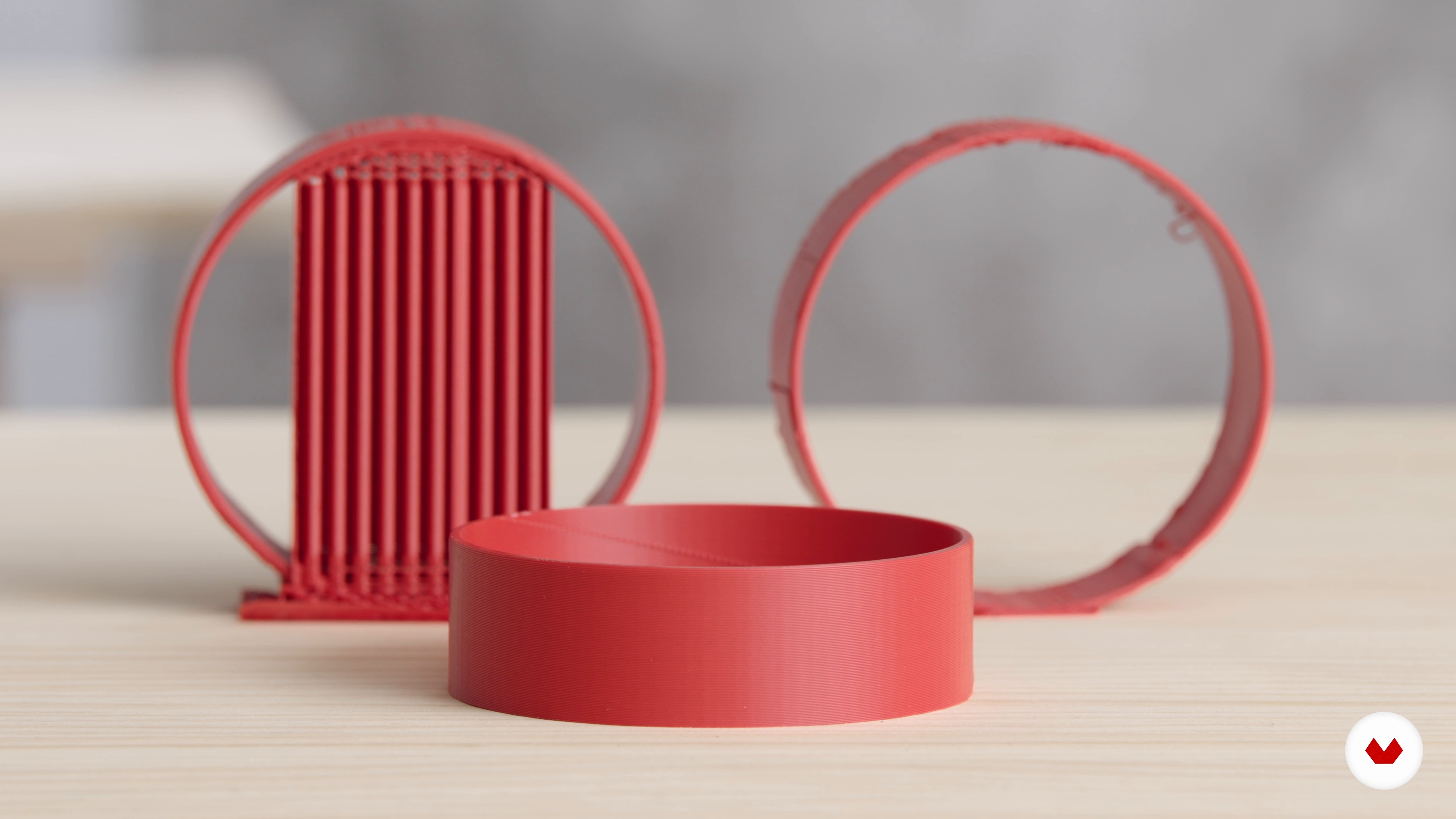
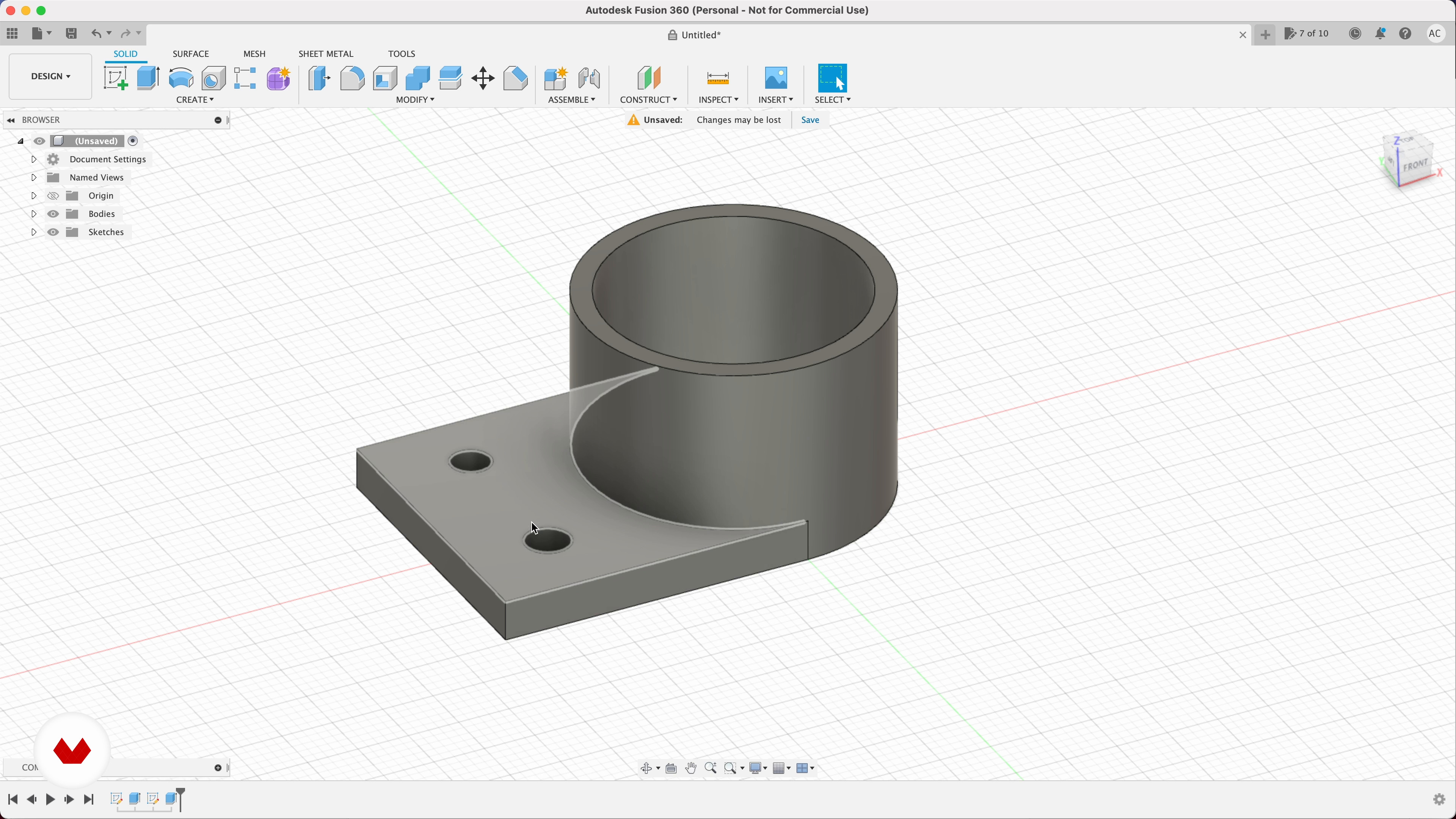
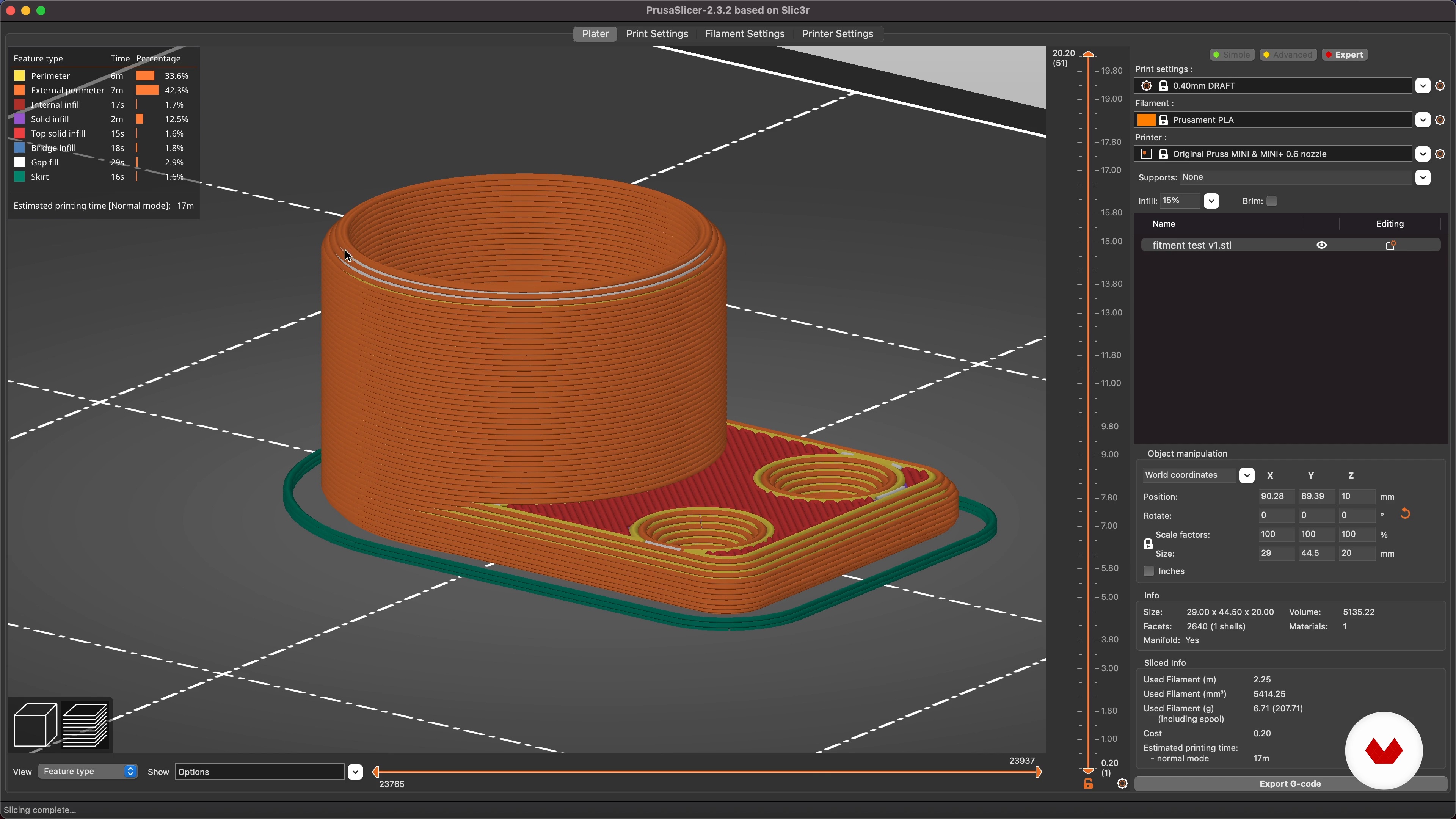
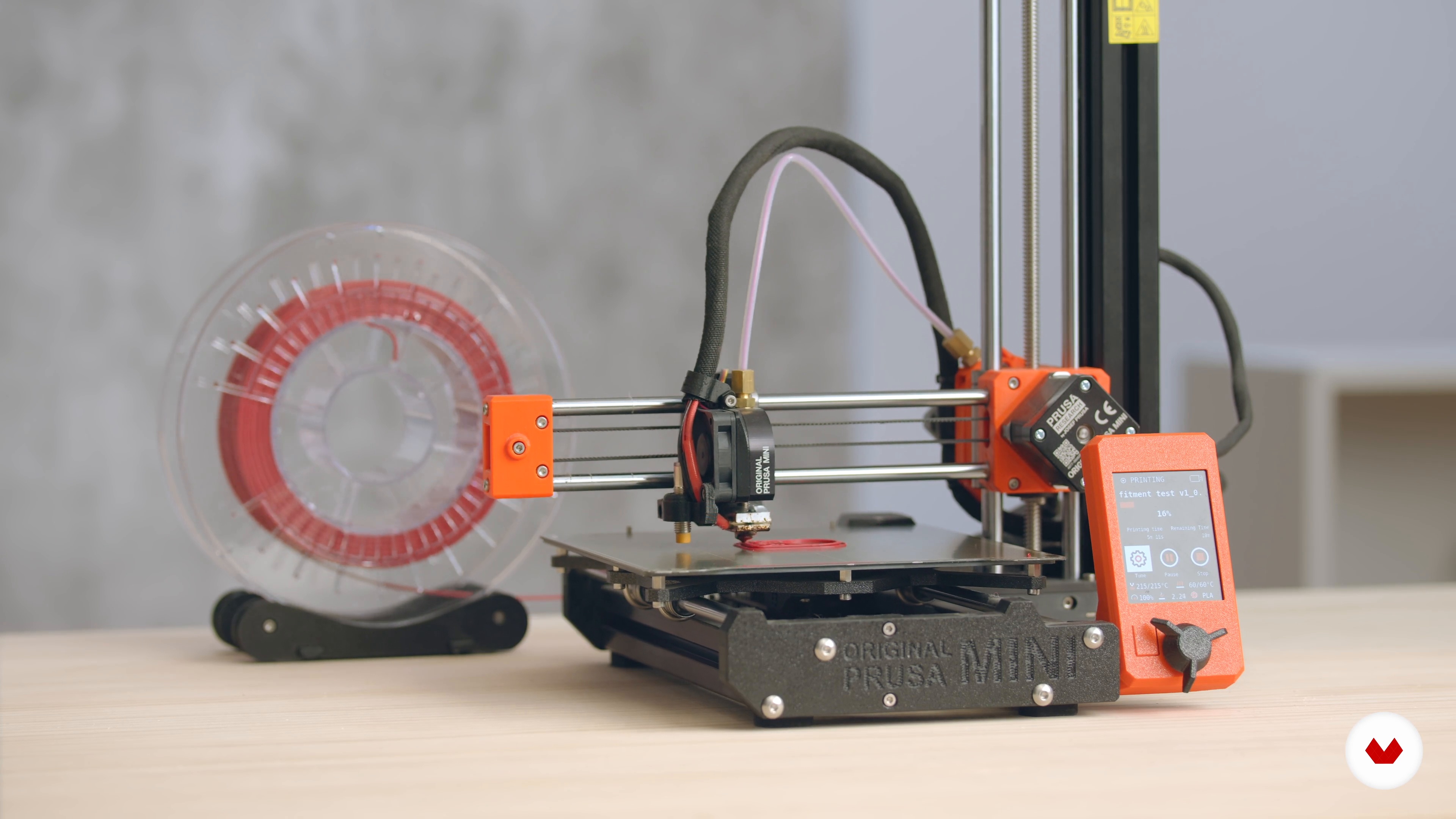
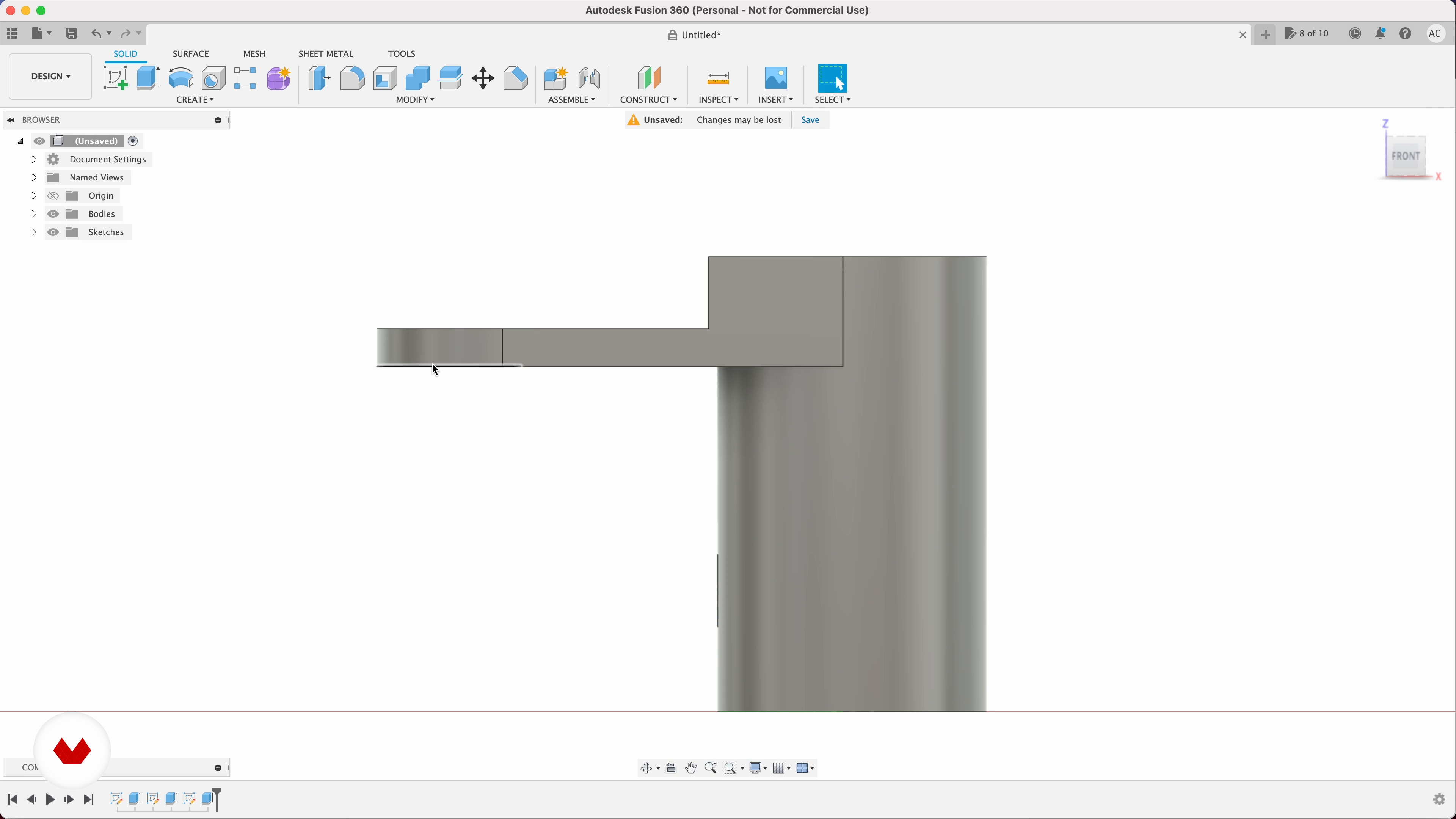
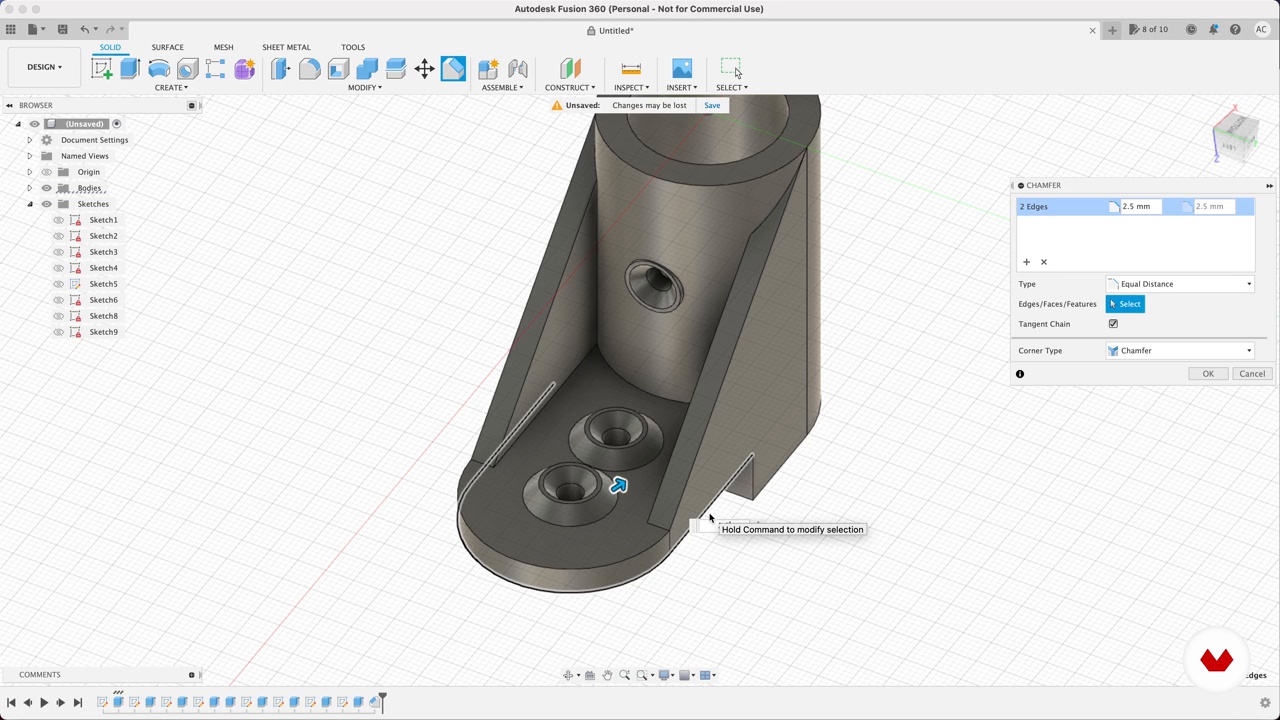
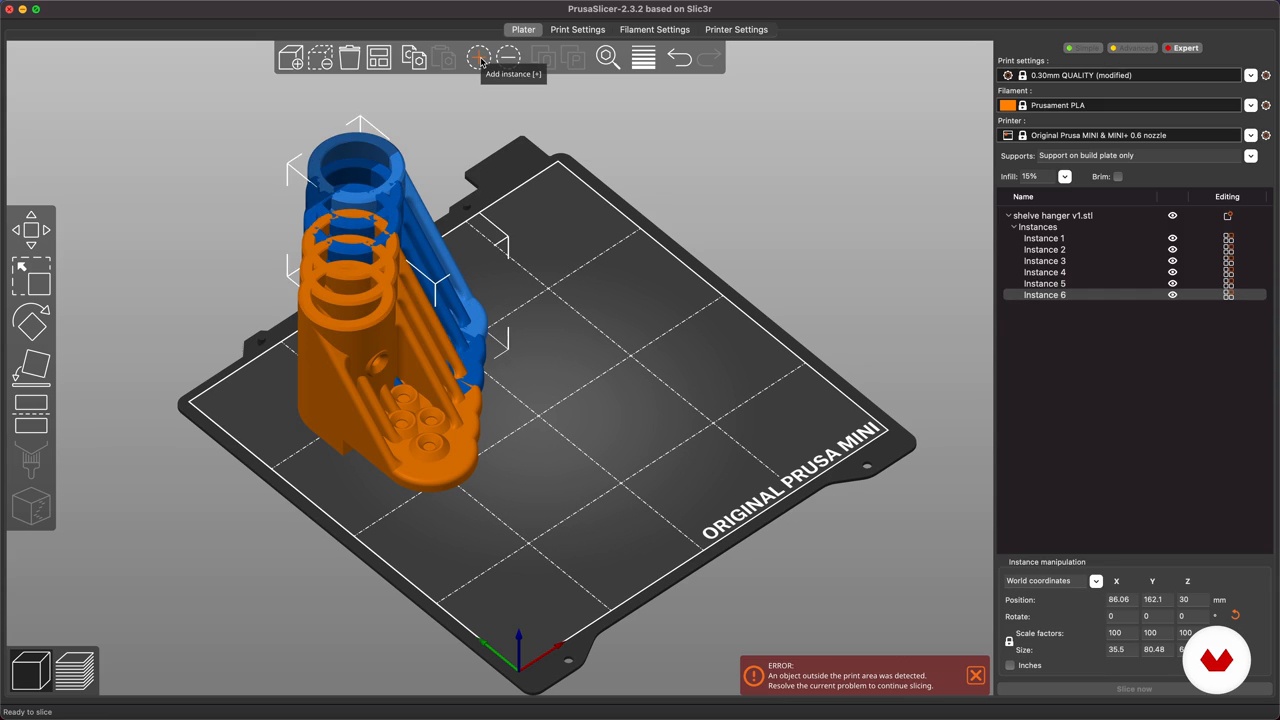
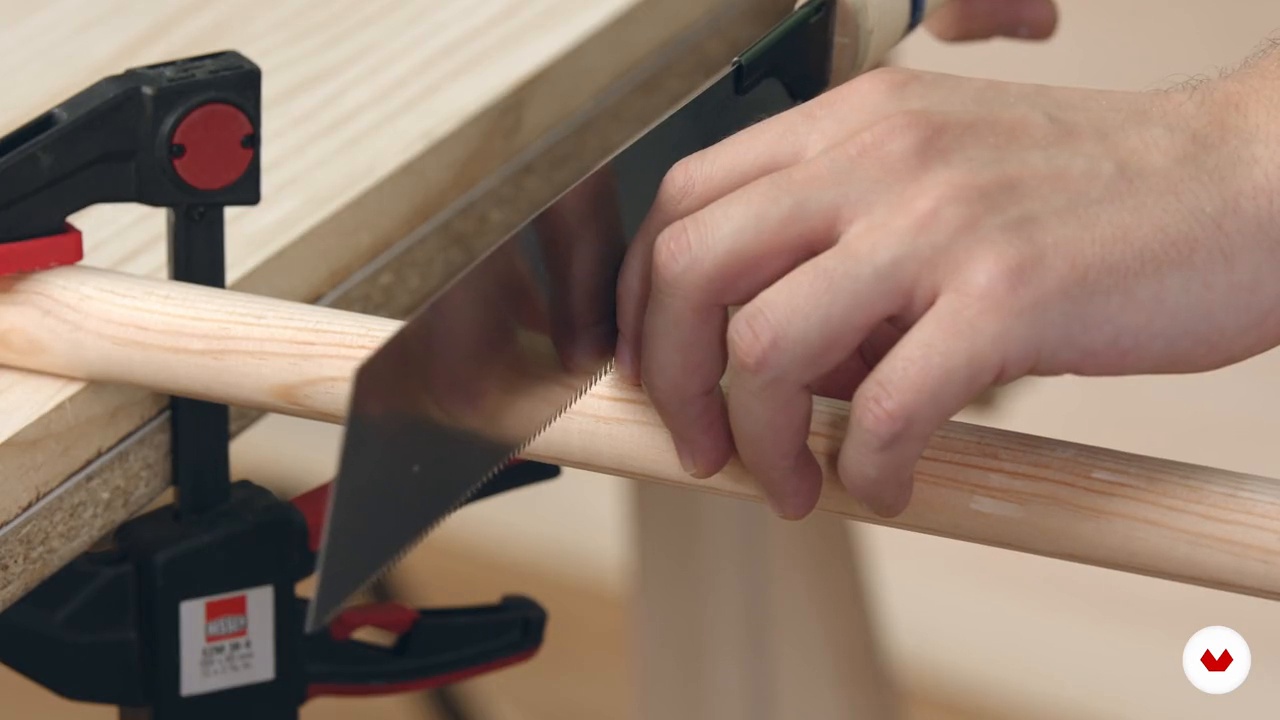
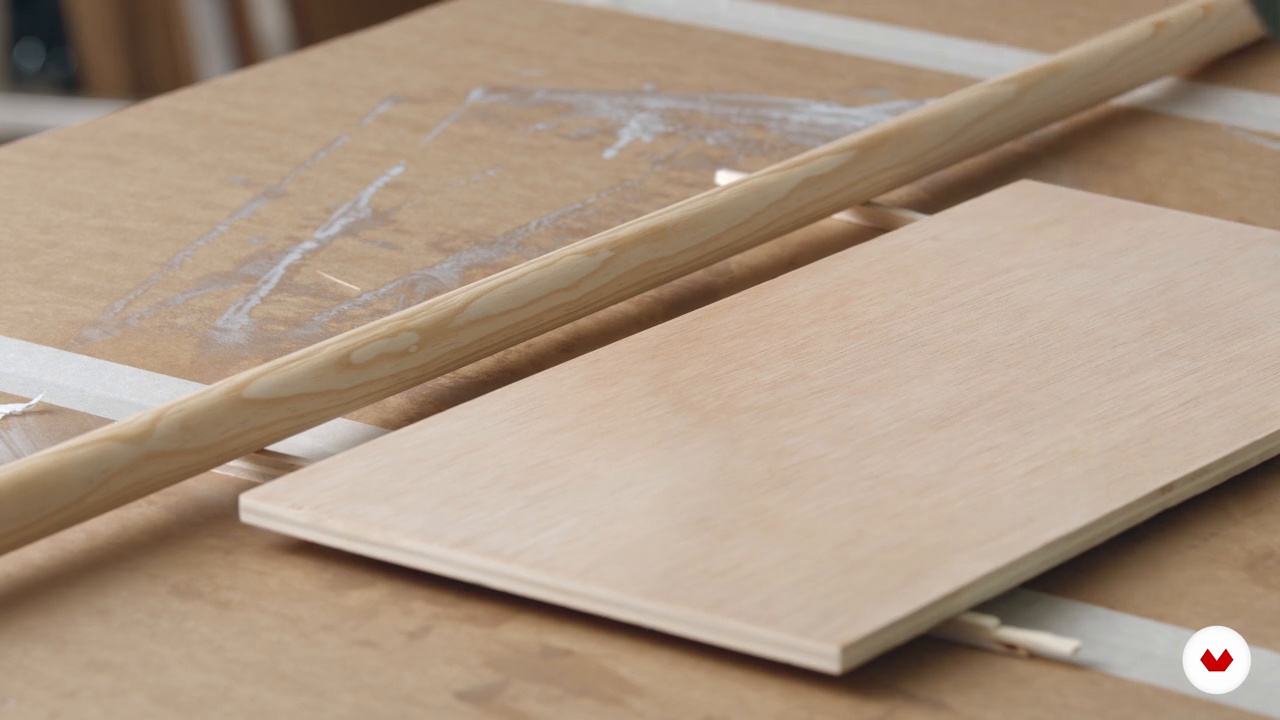
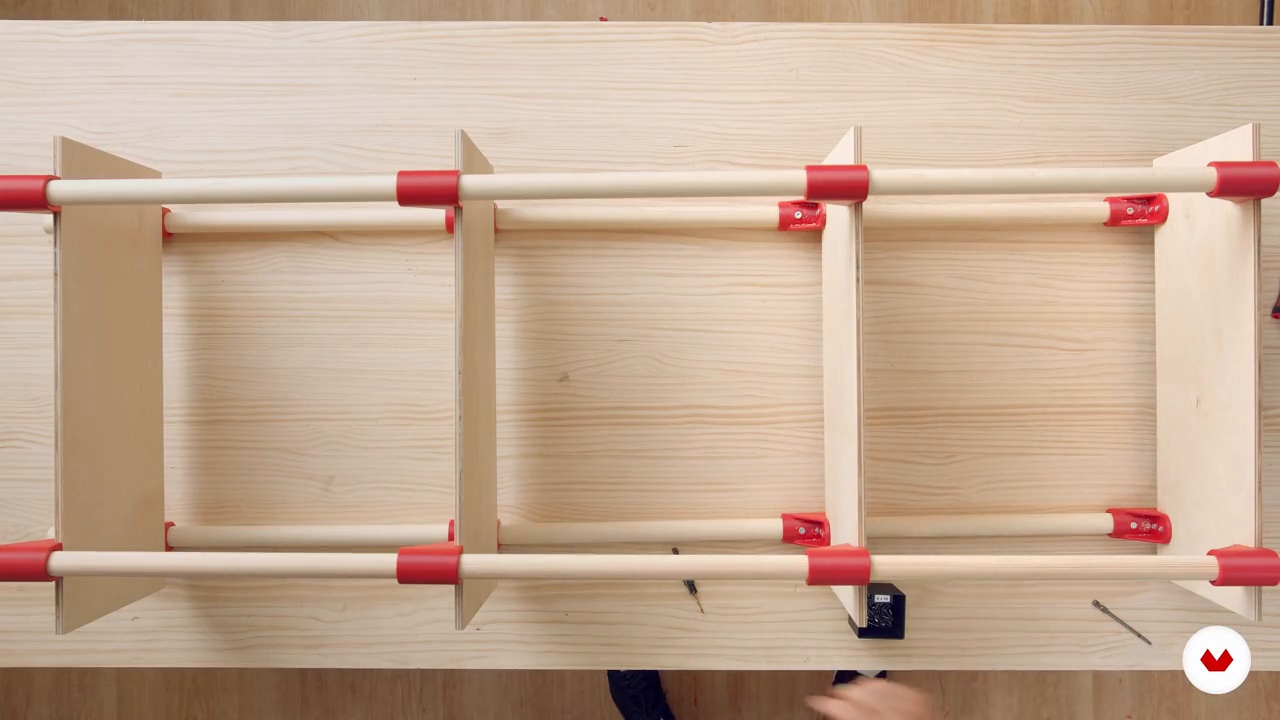
- 100% positive reviews (10)
- 1,867 students
- 111 lessons (19h 23m)
- 90 additional resources (35 files)
- Online and at your own pace
- Audio: English, Spanish
- English · Spanish · Portuguese · German · French · Italian · Polish · Dutch
- Level: Beginner
- Unlimited access forever
What is this course's project?
Craft a traditional staked three-legged stool in oak using hand tools, showcasing skills in wood shaping and furniture construction.
Who is this specialization for?
This online course suits woodworking enthusiasts, aspiring furniture makers, and DIY hobbyists eager to learn traditional and modern woodworking techniques. It's perfect for creative minds looking to enhance their skills and craft unique furniture pieces.
Requirements and materials
No extensive prior knowledge is needed. Bring a passion for crafting and essential hand tools like chisels, saws, and measuring tools. Access to quality wood and 3D printing equipment is beneficial for more advanced techniques.
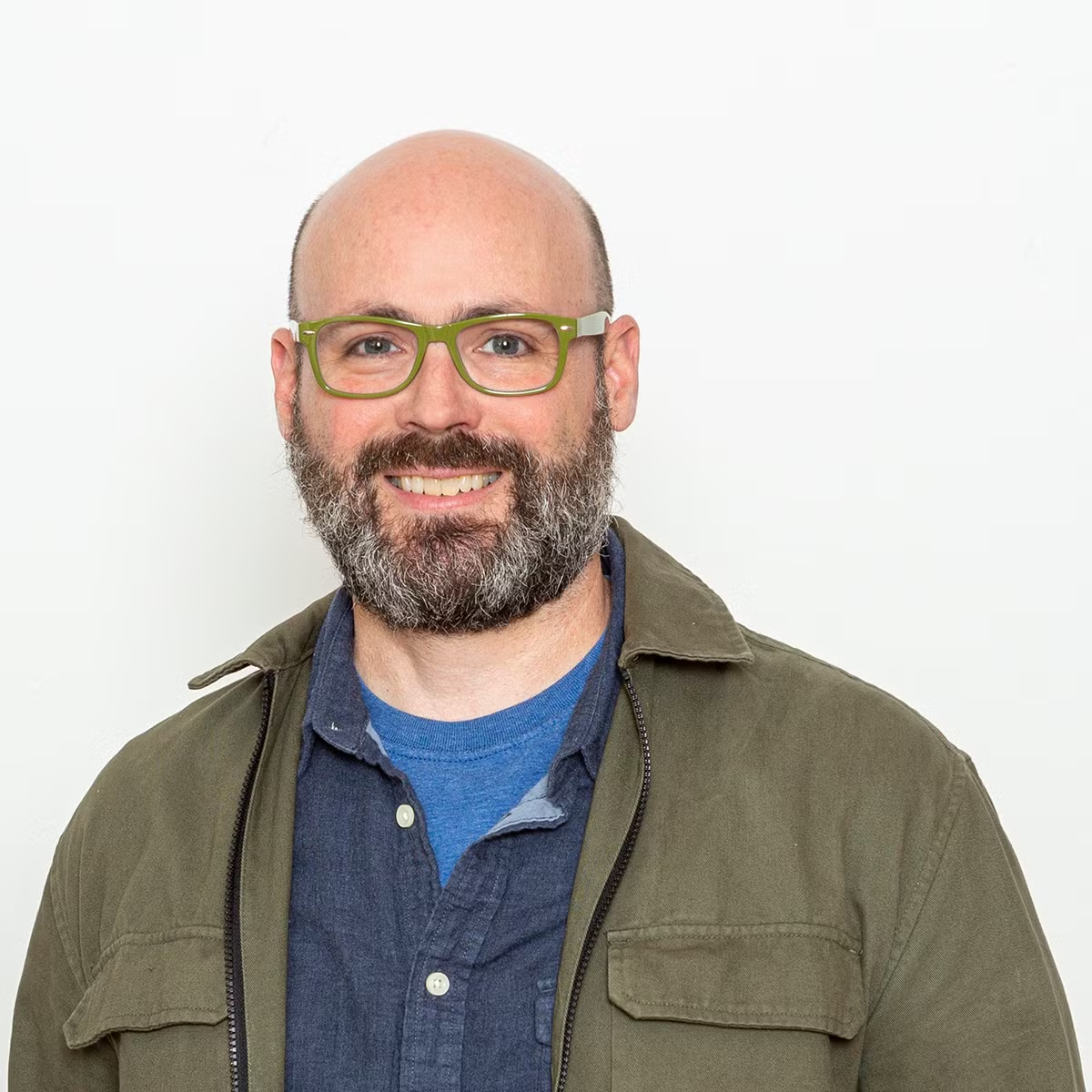
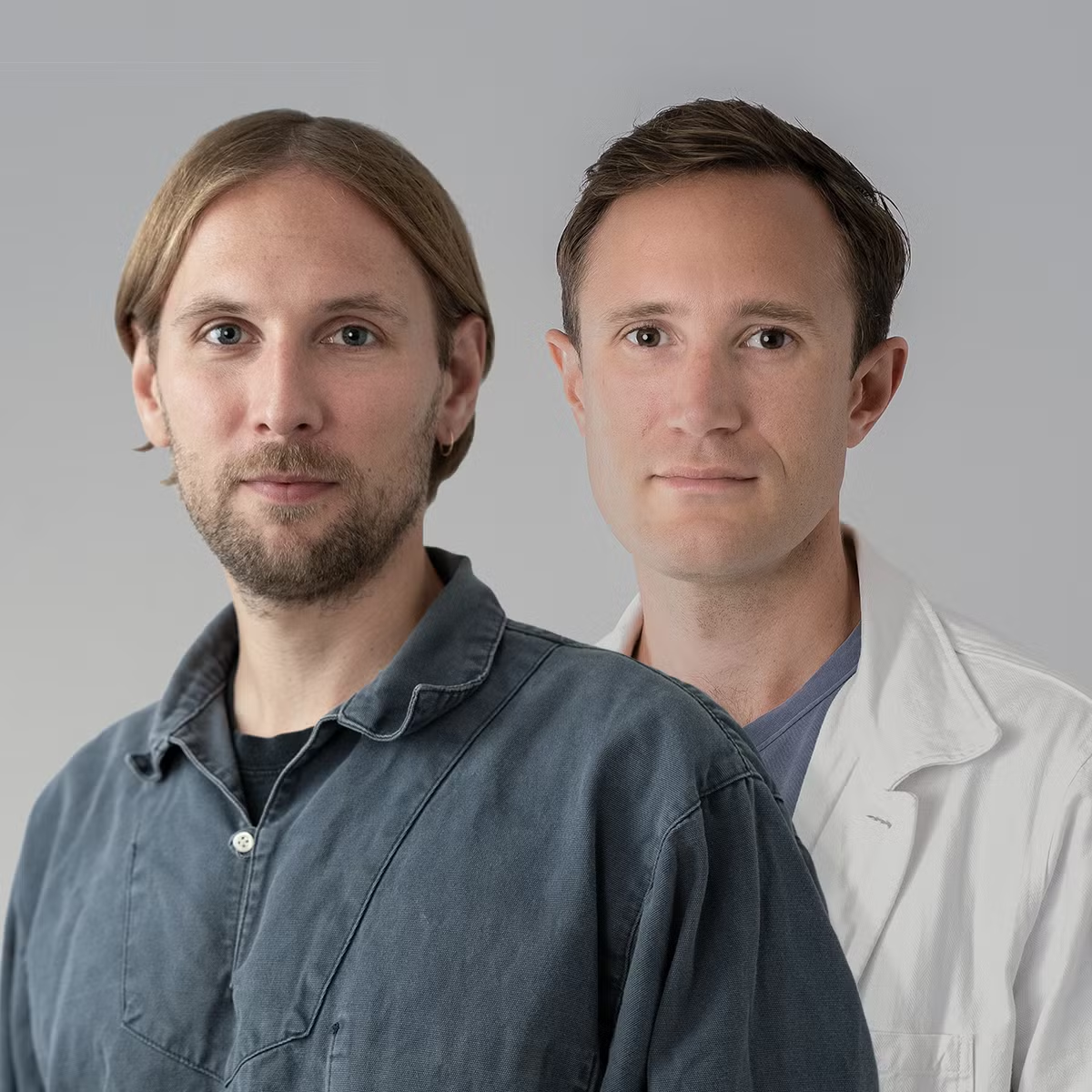
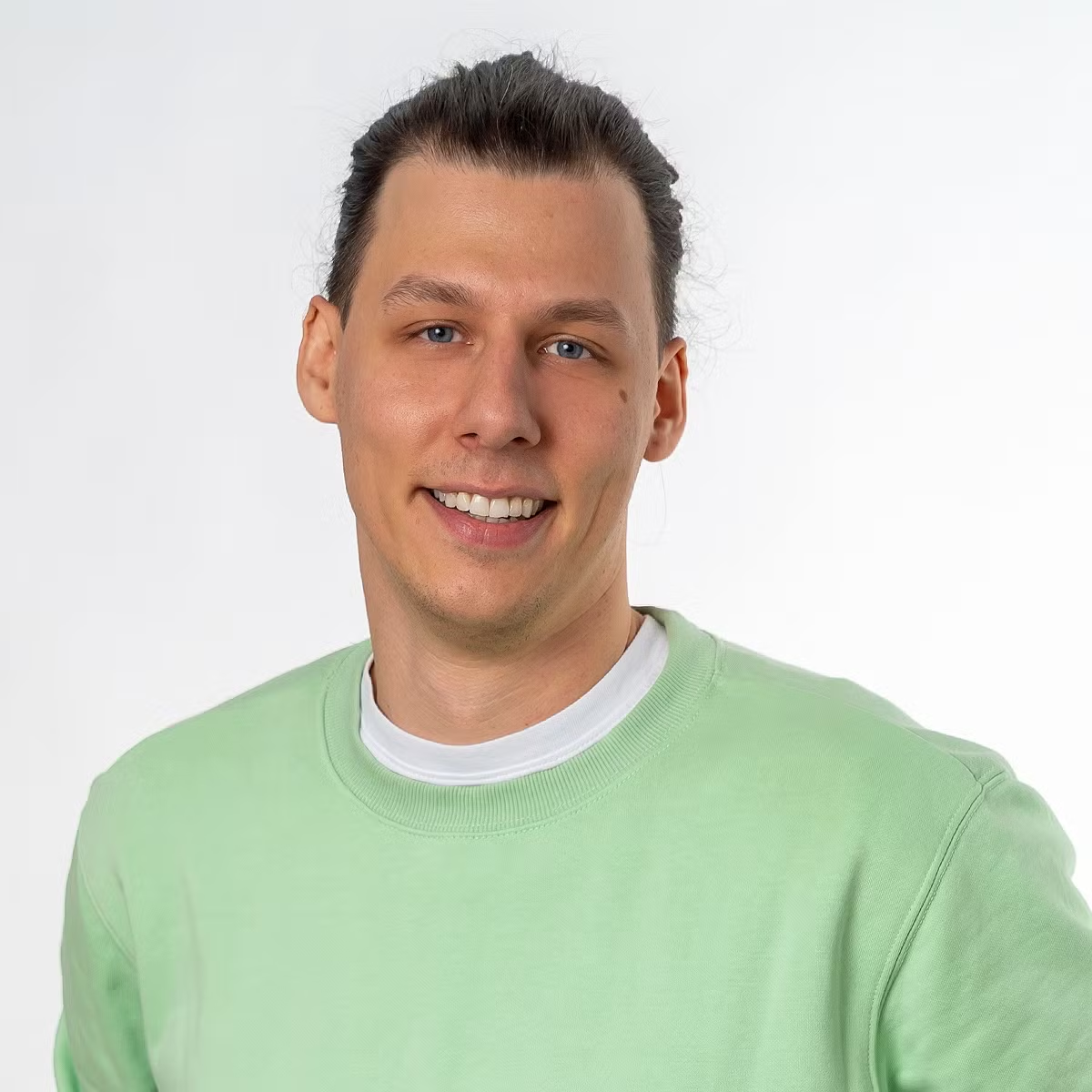
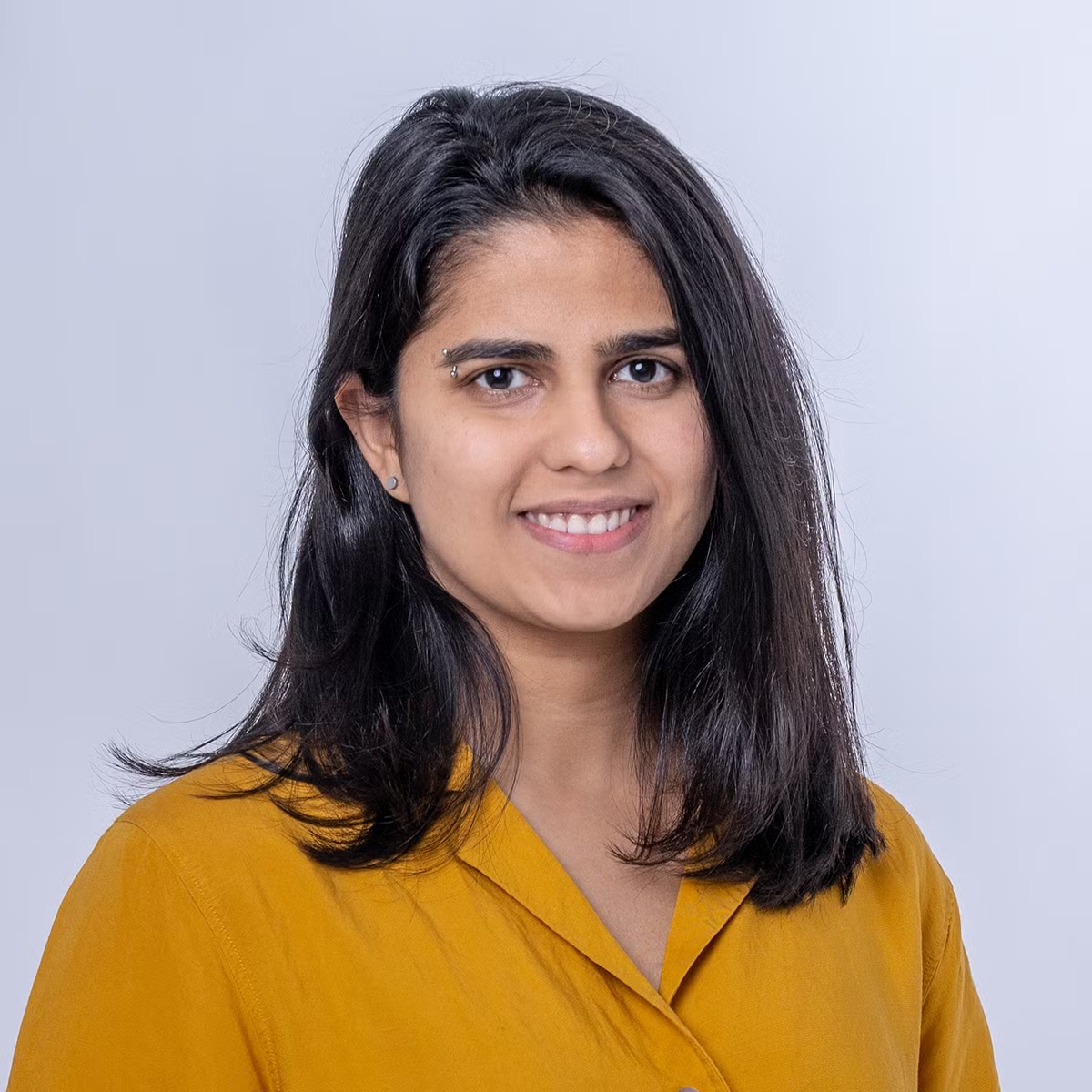
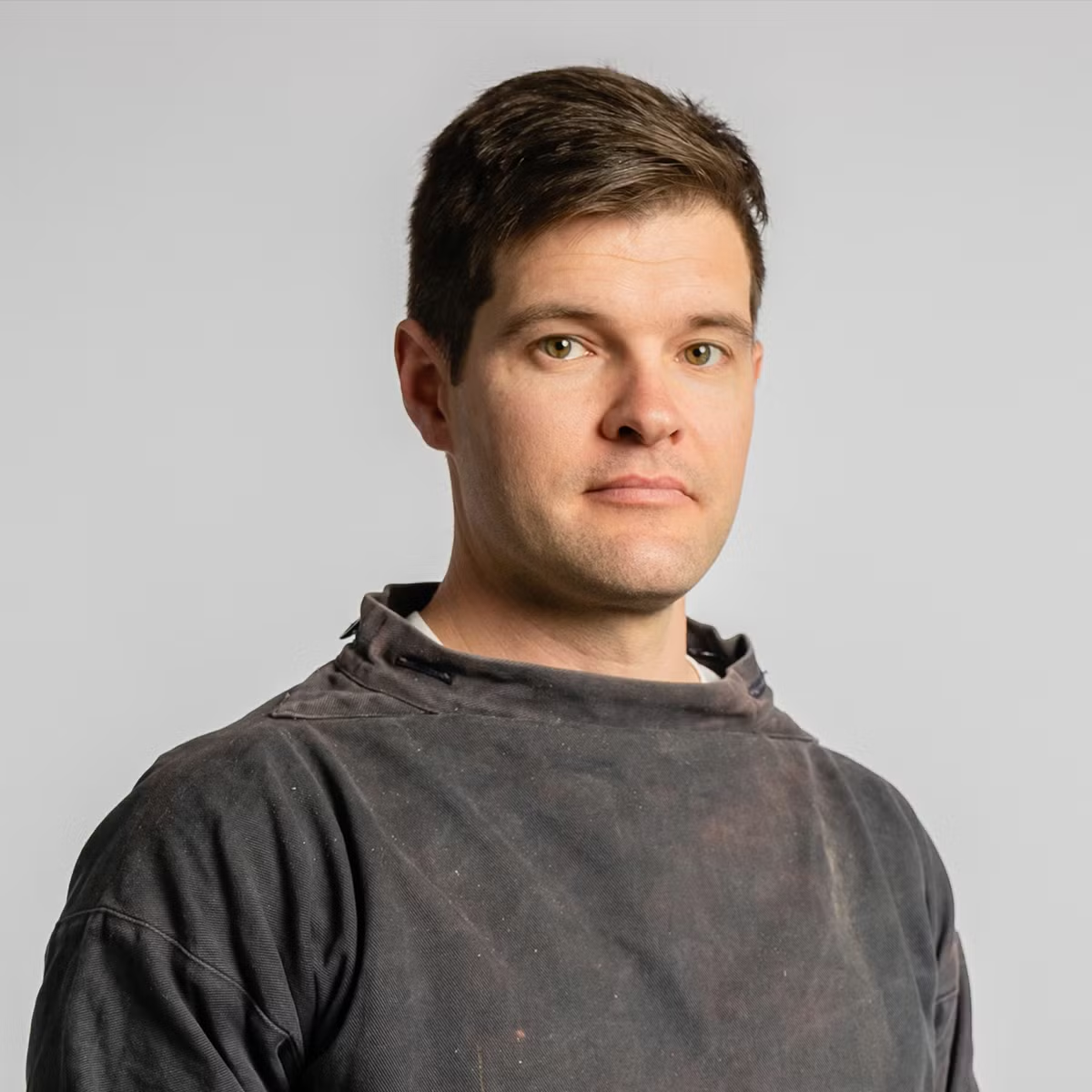
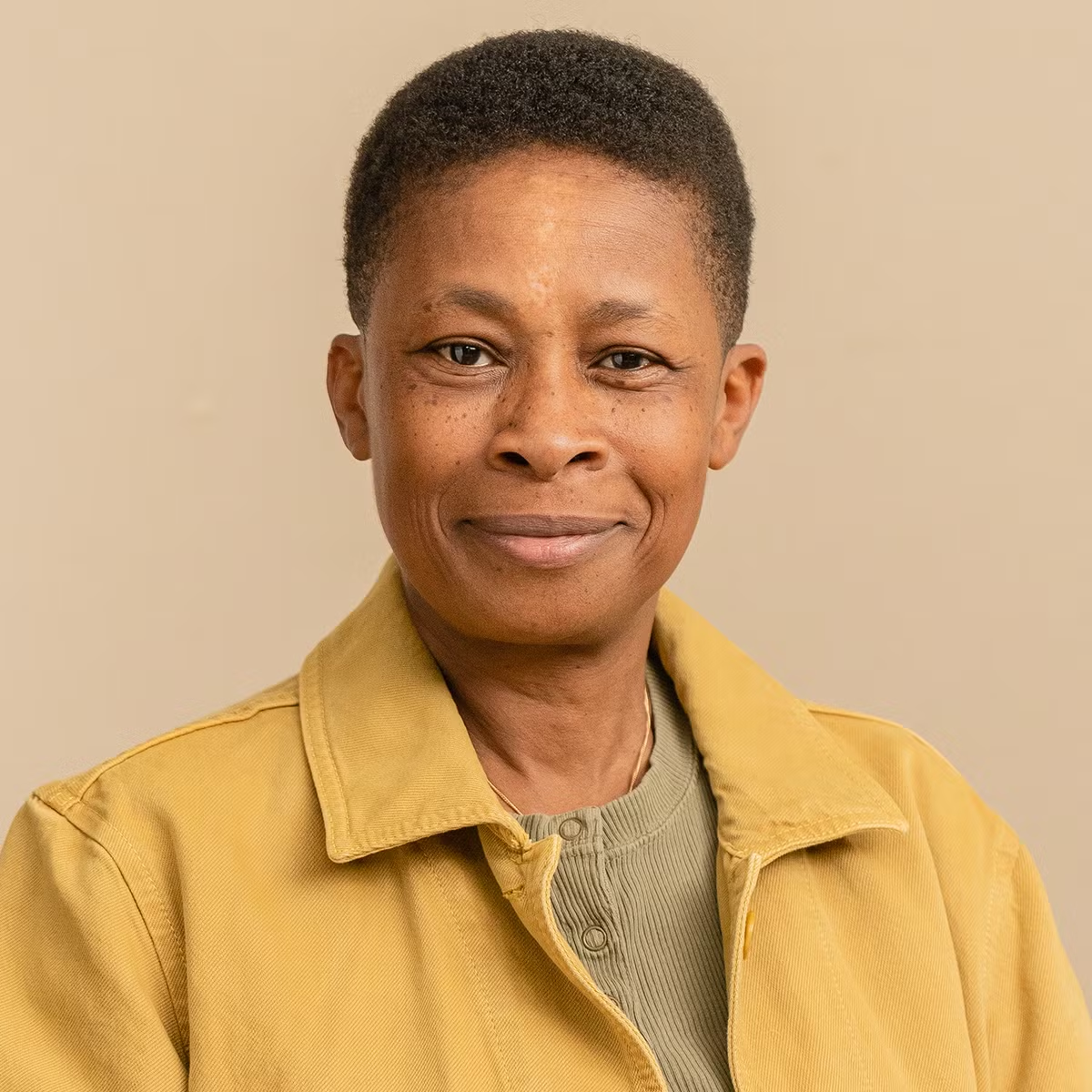
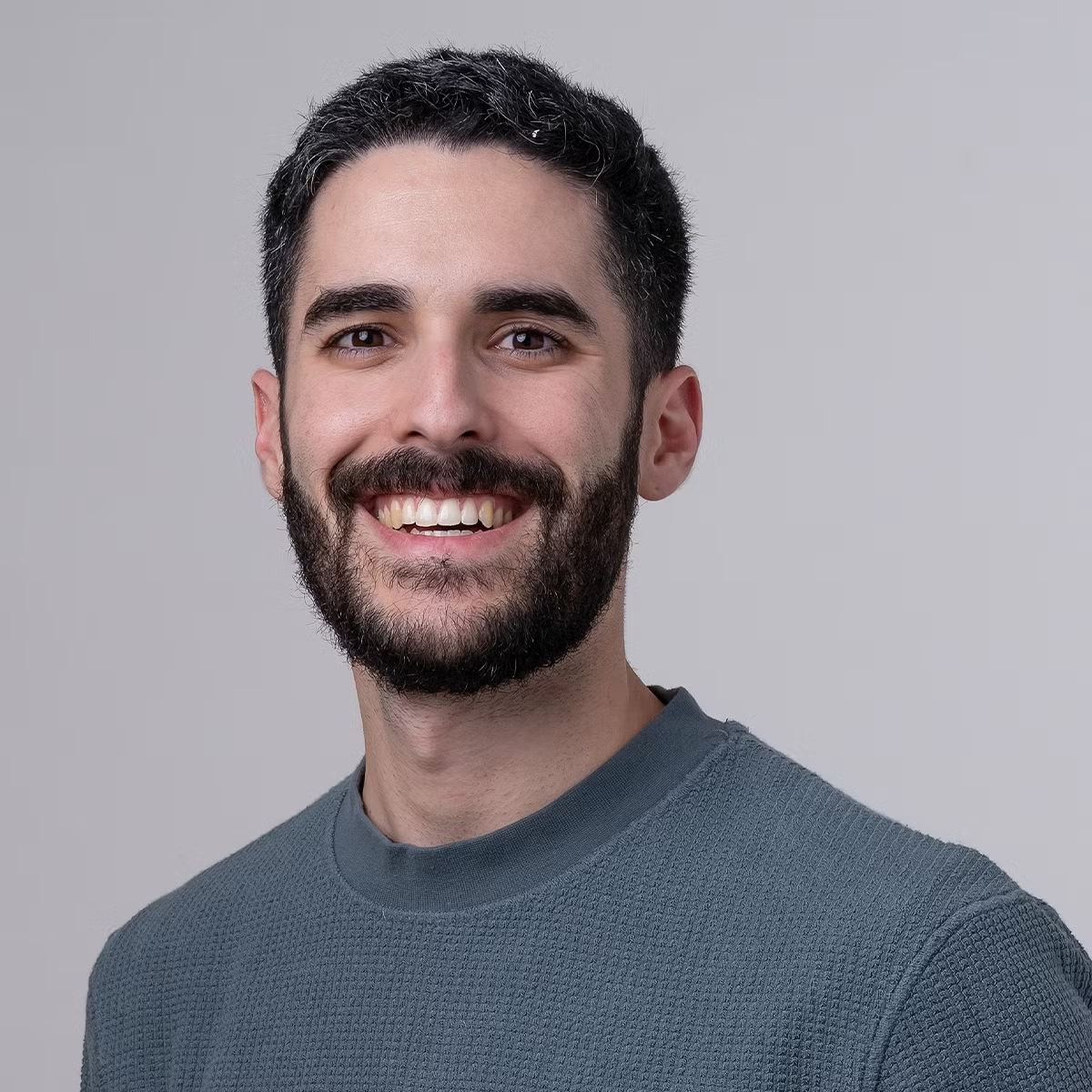
Reviews
What to expect from this specialization course
-
Learn at your own pace
Enjoy learning from home without a set schedule and with an easy-to-follow method. You set your own pace.
-
Learn from the best professionals
Learn valuable methods and techniques explained by top experts in the creative sector.
-
Meet expert teachers
Each expert teaches what they do best, with clear guidelines, true passion, and professional insight in every lesson.
-
Certificates
PlusIf you're a Plus member, get a custom certificate for every specialization course. Share it on your portfolio, social media, or wherever you like.
-
Get front-row seats
Videos of the highest quality, so you don't miss a single detail. With unlimited access, you can watch them as many times as you need to perfect your technique.
-
Share knowledge and ideas
Ask questions, request feedback, or offer solutions. Share your learning experience with other students in the community who are as passionate about creativity as you are.
-
Connect with a global creative community
The community is home to millions of people from around the world who are curious and passionate about exploring and expressing their creativity.
-
Watch professionally produced courses
Domestika curates its teacher roster and produces every course in-house to ensure a high-quality online learning experience.
FAQs
Domestika's specialization courses are online classes that provide you with the tools and skills you need to complete a specific project. Every step of the project combines video lessons with complementary instructional material, so you can learn by doing. Domestika's specializations also allow you to share your own projects with other students, creating a dynamic course community.
All specialization courses are 100% online, so once they're published, specialization courses start and finish whenever you want. You set the pace of the class. You can go back to review what interests you most and skip what you already know, ask questions, answer questions, share your projects, and more.
The specialization courses are divided into different modules. Each one includes lessons, informational text, tasks, and practice exercises to help you carry out your project step by step, with additional complementary resources and downloads. You'll also have access to an exclusive forum where you can interact with other students, as well as share your work and your final project, creating a community around the specialization course.
You can redeem the specialization course you received by accessing the redeeming page and entering your gift code.
cosmiccollisions
PlusI have always wanted to learn woodworking but didn't even know where to start. This course is brilliant!!
marylenefaucher
Très bon cours, ma façon de travailler s’est enrichie.
View translation
Hide translation
operaciones_trodemex
Muy bien detallado los cursos, los proyectos nos son difíciles, lo que facilita el trabajo para quienes estamos recién comenzando.
Totalmente recomendable.
View translation
Hide translation
edwardakuffoj
PlusI love the fact that even in the same specialty, there is a blend of different niches and specializations. The diversified views make the whole learning journey worthwhile
b_sanchezfernandez_bsf
PlusJe suis Menuisier ébéniste de formation, je trouve que les cours sont tres bien fait et surtout bien expliqué.
Pour ma part, je trouve important de revoir les techniques et d'autres façons de les pratiquer.
Je recommande vivement à tous cette spécialisation !
View translation
Hide translation